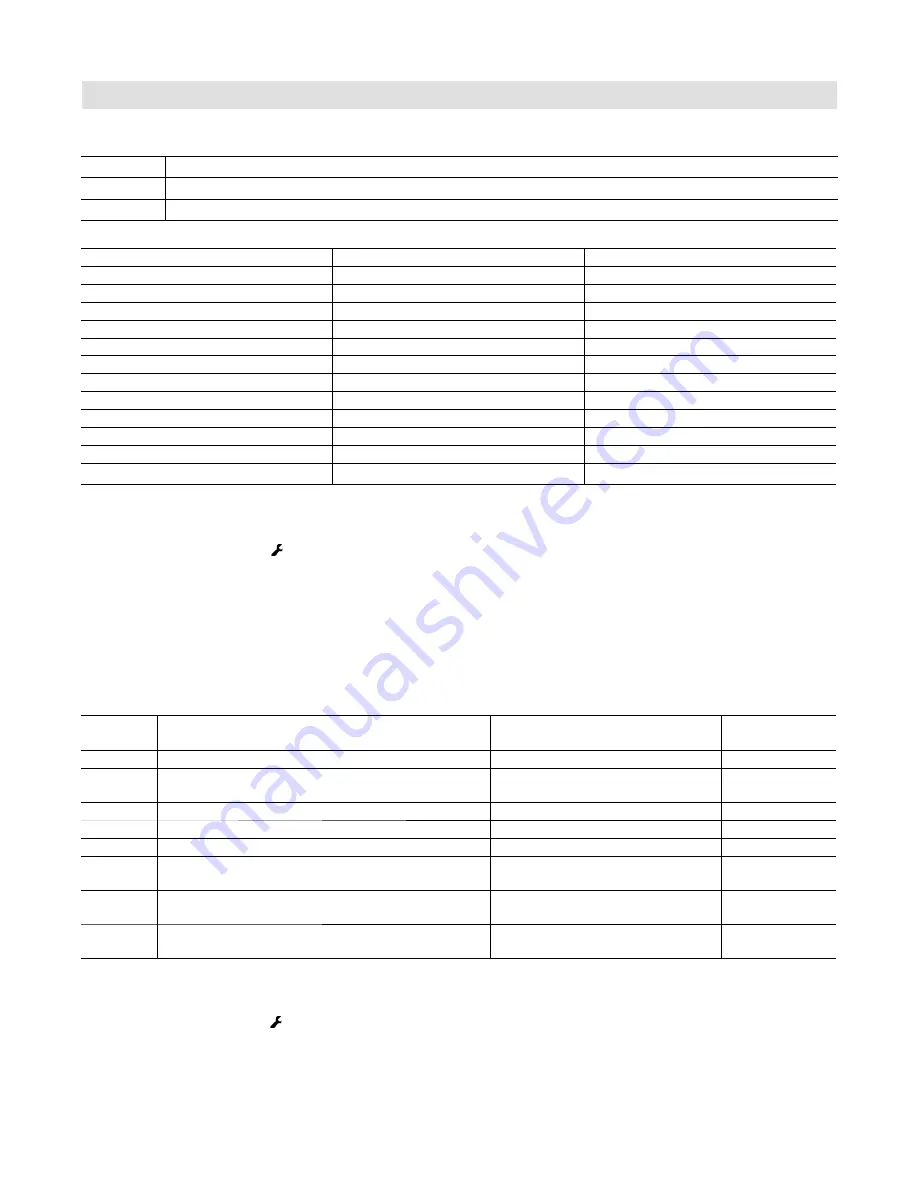
45
5584 109 - 10
Vitocrossal 200 CM2 186 to 311 Service
Burner Control Unit
Burner Control Unit
(continued)
Configurations:
Menu item
Description
5
Changeover from the operating display of the burner control unit phase to other process information
6
Configuration of control function operating parameters
Menu item “5“ is used to display the following process information:
Sub-menu Item
Process Information
Units/Scale
0
Phase
1
1
Boiler water temperature
*1
°C
2
Flue gas temperature
*1
°C
3
Ionization current
I in 1/10
μ
A
4
Set speed
%
5
PWM manipulated variable
%
6
Actual speed
RPM x10/min
7
Gas pressure switch 1
0 or 1
8
Gas pressure switch 2
*1
0 or 1
9
Air pressure switch
0 or 1
A
Gas valve 1
0 or 1
b
Gas valve 2
*1
0 or 1
1.
S
longer than 2 seconds “ “
flashes.
2.
Y
until “5“ is shown under Service.
3.
S
“5“ will be displayed under Status
4.
Y
until “3“ is shown under Service.
5.
S
“3“ is shown under Status and during operation
the ionization current is shown under Service
(e.g. 30 = 3.0
μ
A).
*1
Not available for all boiler types, check at control unit if required.
Menu item “6“ is used to change the following operating parameters:
Sub-menu
Item
Parameter
Units/Scale
Delivered
condition
1
Maximum operational input
% of rated input
100%
2
Gas type
0=NG (natural gas)
1=LPG (liquid propane gas)
3
Not assigned
--
--
4
Maximum boiler water temperature
from 41 to 260°F (5 to 127°C)
203°F (95°C)
5
Integral threshold value of controller
In Kmin from 1 to 255
30 Kmin
6
Runtime optimization
0=minimum pause
1=integral method
1
7
Motorized vent damper
0=without damper
1=with damper
0
0
Reset all operating parameters to their delivered
condition
--
--
6. To exit the process information menu, press and
hold
S
longer than 2 seconds “_“
flashes.
7.
Y
until “5“ is shown under Service.
8.
S
“5“ will be displayed under Status
9.
B
until “0“ is shown under Service.
10.
S
to change to the operating display.
1.
S
longer than 2 seconds “ “ flashes.
2.
Y
until “6“ is shown under Service.
3.
S
“6“ will be displayed under Status and the current
value for the maximum operational output in % is
shown under Service.
4.
Y
/
B
for required maximum operational output.
5.
S
to confirm. If applied successfully, “1“ will be
shown under Service, “0“ if it failed.
6.
S
to change to the operating display.
7.
R
to reset unit and apply settings.
Example: to display the ionization current, press the following keys:
Example:
to set the maximum operational burner input to between 0 and 100%, press the following buttons: