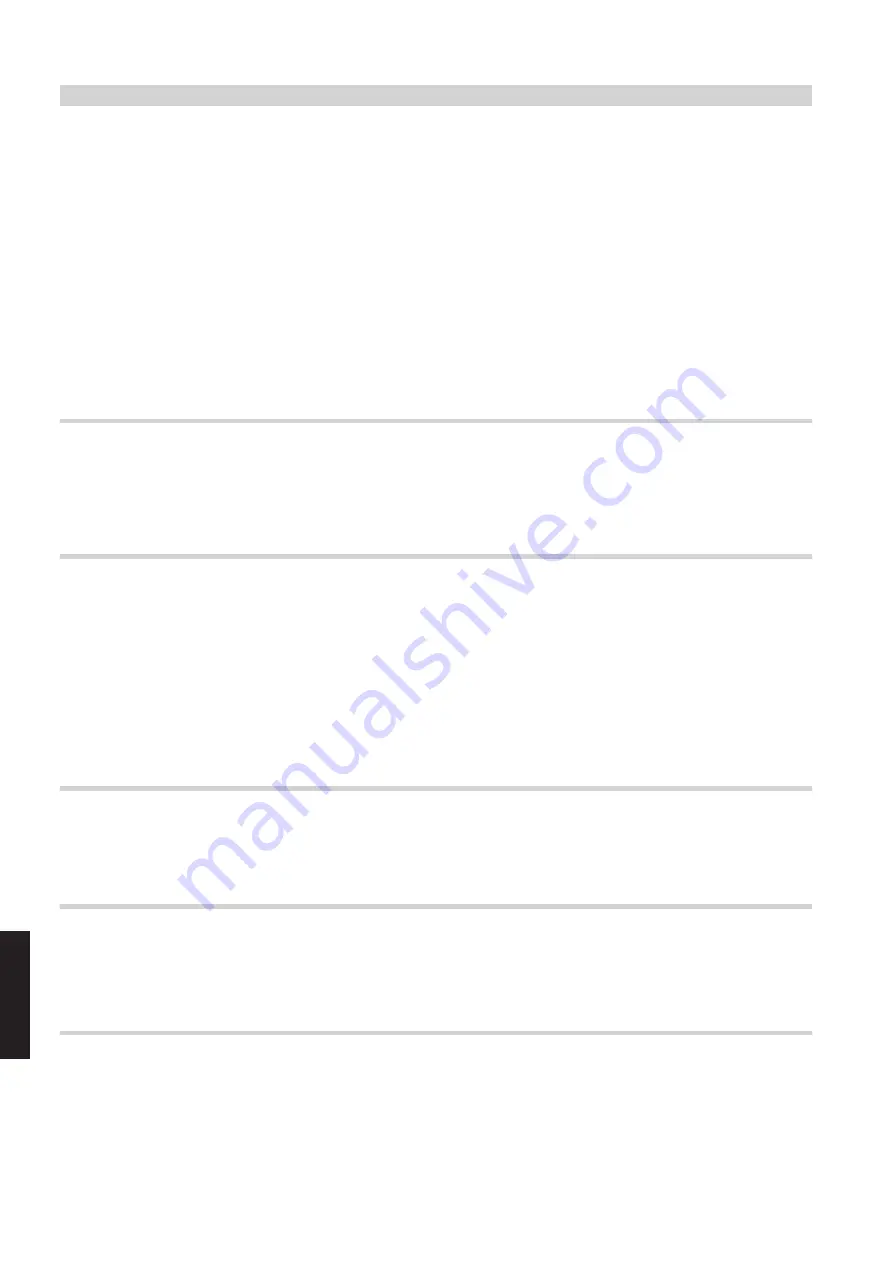
7.4 Water connection
Heating connections
Existing systems
Before connecting to the solid fuel boiler, thoroughly flush the existing
heating system to remove dirt and sludge.
Otherwise, this dirt and sludge will be deposited inside the solid fuel
boiler and can lead to local overheating, noise and corrosion. Boiler
damage caused by such deposits is excluded from our warranty.
Where necessary, install dirt traps.
Connections on the water side
On site, ensure that there is a water supply independent of the power
supply. This (redundant) design guarantees that the boiler is reliably
cooled via the thermally activated safety valve in the event of a power
failure. We also refer to the standards and regulations listed in this
document.
Connect all heat consumers and heating circuits to the boiler flow and
boiler return connectors. Never make any connections to the safety
flow or to other connections.
We recommend you install shut-off valves in the heating flow and
return lines, so that the entire water content will not have to be drained
if work is required on the solid fuel boiler or the heating circuits.
Easy installation
For safety temperatures up to 110 °C, the boiler requires no inter-
mediate flow piece for the connection of safety equipment.
The boiler is already equipped with all the necessary connections, e.g.
for water level or pressure limiters.
Boiler circuit and shunt pumps
In order to reliably prevent boiler corrosion caused by flue gas con-
densation, the boiler return temperature must never fall below 65 °C.
The boiler has variable output-dependent control. This requires a con-
stant boiler flow rate of the water to be heated. The boiler circuit with
boiler circuit pump and boiler mixer must therefore be installed in
accordance with the design recommendations.
The boiler circuit should be designed in such a way that the tempera-
ture differential between flow and return is 15 °C or less. Control of the
boiler circuit pump and valve of the return temperature raising facility
is integrated in the supplied control unit.
Safety equipment to EN 12828
Safety equipment for the heating system must be installed by the
authorised heating contractor.
EN 12828 applies to the design of hot water heating systems with
safety temperatures up to 110 °C.
This standard contains safety requirements for heat generators and
their systems.
■ Sealed expansion vessel
■ A safety valve at the highest point of the boiler or on a pipe connected
to this point
■ It must not be possible to shut off the connection line between the
boiler and the safety valve. No pumps, fittings or constrictions may
be present in this line.
■ The discharge pipe must be designed in such a way that no pressure
increase is possible. Any expelled heating water must be drained off
safely. The outlet point of the discharge pipe must be arranged in
such a way that any water expelled from the safety valve can be
drained off safely and visibly [tundish].
■ Thermometer and pressure gauge
■ Low water indicator
7.5 Electrical installation
The electrical installation should be carried out in accordance with the
wiring diagram. In the vicinity of hot parts (flue gas fan, flue pipe),
cables must be routed in steel pipes and with appropriate clearances
for temperature protection.
The cable entries for motors and appliances must be dust-proof and
provided with strain relief.
7.6 Safety equipment
Expansion
In the case of sealed expansion, the pre-charge pressure of the expan-
sion vessel should be equal to the maximum system height plus
0.2 bar (0.02 MPa).
Extinguishing devices
Generally, an extinguishing device is required near the feed screw
conveyor. This device is used in the event of a fault (e.g. power failure)
to safely prevent burn-back. For safety reasons and in order to avoid
damage caused by flooding, it is not advisable to connect the extin-
guishing device directly to the water mains.
This extinguishing device is equipped with a 25 l extinguishing water
container with float switch and an adjustable Danfoss extinguishing
valve. In accordance with TRVB 118, the container should be equipped
with fill level monitoring. The Vitoligno 300-H automatically switches
off in the event of a water shortage. In the event of excessive temper-
ature, the feed screw conveyor is safely flooded, but to a limited
extent.
Design information
(cont.)
54
VIESMANN
VITOLIGNO 300-H
7
5672 507 GB