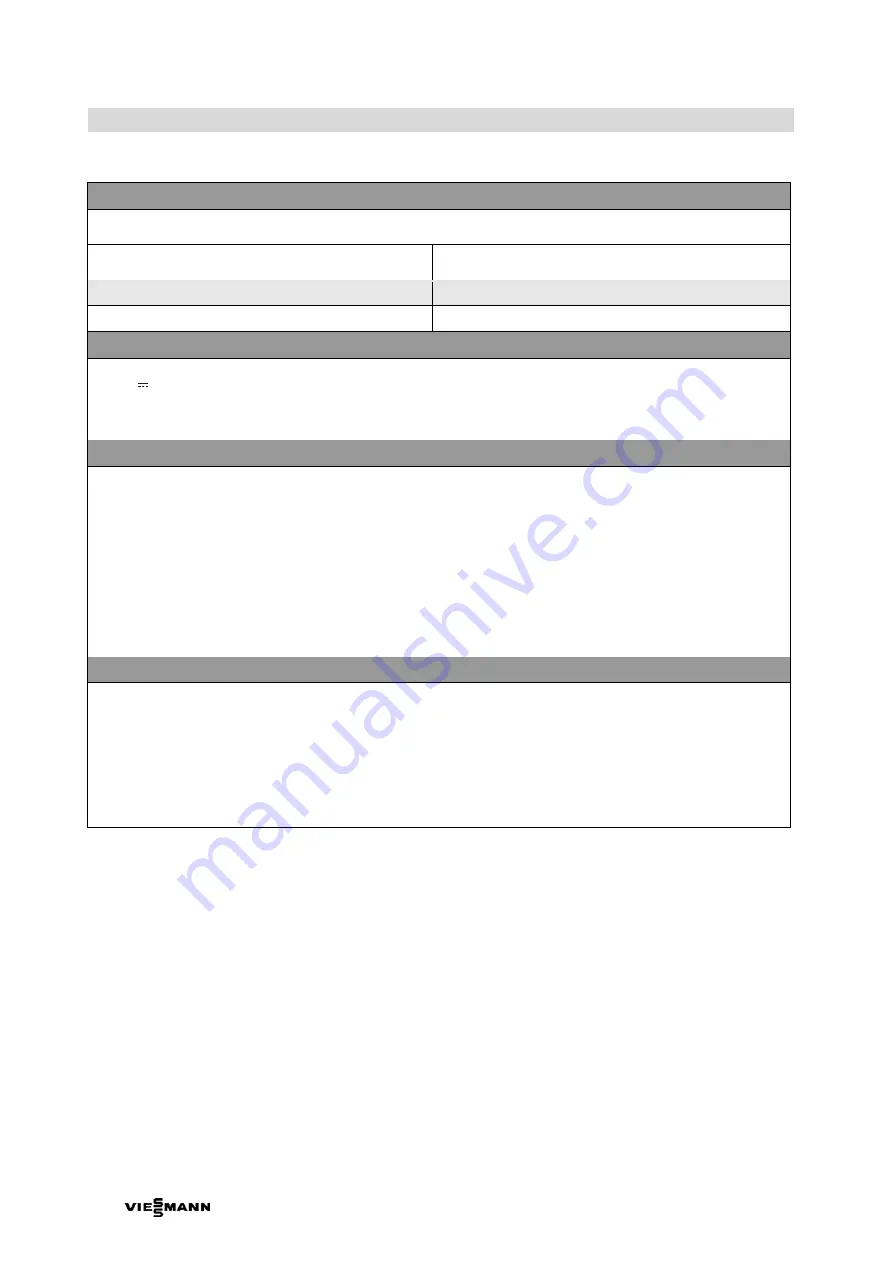
Control system (BMS 2007)
16
CHP switching cabinet
VITOBLOC 200
5780078
GB
output regulation and monitoring
The governor is used to adjust the alternator
’s active power to an adjustable target value in parallel operation. All
parameters are listed below (level 3) that are relevant to output regulation and output monitoring.
Temperature controller (return increasing mechanism)
A constant controller is built into the module control under the controller menu. The controller uses a signal
(0
–10
V
)
to trip the customer’s control valve with reference to the regular temperature (either PT100/2 or PT100/3
adjustable in level 2) and the set target value. Its supply voltage (24 V, AC) is available in the module control
switchgear. The KP and TN regulating parameters (level 3) are adjustable along with the direction of control action
and control valve minimum opening.
Module select and deselect after temperature heating water return (only active in the heat mode)
Two limits are built into the module control under the release menu that enable you to deselect and release after
temperature (either PT100/2 or PT100/3 adjustable in level 2). The precise adjustment of these parameters makes
sense when there is no control equipment and you want to prevent emergency shutdown due to high return
temperature. The cogeneration module is internally deselected when it exceeds the deselect limit. The cogeneration
module is automatically reselected after the temperature has cooled down to below the release limit. PT100/2 is the
internal return sensor and PT100/3 is available for other work, preferably in the main return of the module.
Optional modulation: A percentage output value is assigned to the release and deselects limits so you can enter at
release (60°C/100%) and deselect (70°C/50%). That would mean that the module starts at a return temperature of
60°C and would run at 100% output. The module would only run at 50% load at 70°C and it would be deselected
above 70°C. The module would automatically run flexibly in output between the select and deselect values such as
at a return temperature of 65°C at 75% output. Beyond this, a freely adjustable delay is available for the release and
deselect limit.
Lambda regulation
Lambda regulation makes sure that the combustion air fed to the system corresponds to the combustion air actually
needed (lambda = the ratio of fed combustion air to needed combustion air; lambda=1 regulation). At this ratio, the
emission of pollution is lowest using a (lambda regulated) three-way catalyst at the same module output. A step
motor uses a control valve to adjust the mixture feed. The lambda probe voltage (0
–1,000 mV) is used as a control
variable for the mixture of fuel/air. The control valve is shut if the lambda probe voltage is greater than the target
value set on the control system and the control valve is opened if the lambda probe voltage drops below the target
value. The cogeneration module is shut down when the step motor is not regulated to the target value within an
adjustable period. The step motor is triggered via two digital contacts. The pulse-interval ratio is adjustable just like
all targets and limits (level 3).
Tab. 17 Description of the functions, Part 3
– output regulation and monitoring, temperature controller, module deselect and select
after temperature and lambda regulation
output target
tolerance window
+/- kW with time monitoring for fault
clearance
warm-up limit
maximum limit monitoring
for fault clearance
target value ramp (kW/s)
reverse power monitoring
for fault clearance