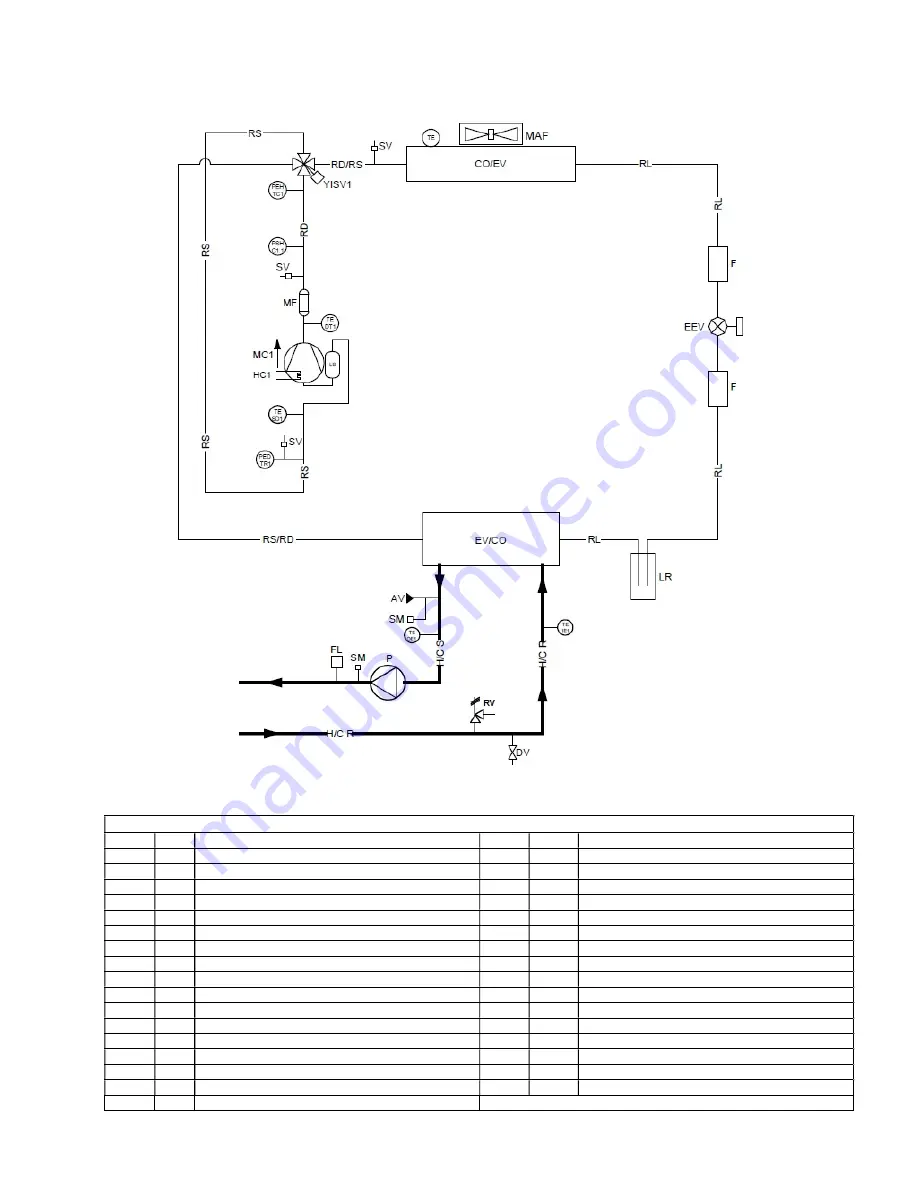
23
6020930
Vitocal 100-A 10 / 12
KEY
CODE
NUM. DESCRIPTION
CODE
NUM.
DESCRIPTION
MC
1
COMPRESSOR
H/CS
UTILITY WATER OUTLET
CO/EV
CONDENSER (IN CHILLER MODE)
H/CR
UTILITY WATER INLET
EV/CO
EVAPORATOR (IN CHILLER MODE)
PEHTC
1
HIGH PRESSURE TRANSDUCER
EEV
ELECTRONIC EXPANSION VALVE
PEDTR
1
LOW PRESSURE TRANSDUCER
YISV
1
4-WAY CYCLE REVERSING VALVE
TE
OUTDOOR AIR TEMPERATURE PROBE
LR
LIQUID RECEIVER
TE SD
1
INTAKE LINE TEMPERATURE PROBE
F
FILTER
TE DT
1
COMPRESSOR DISCHARGE TEMPERATURE PROBE
SV
FILLING
CONNECTION
PSHC
1.1
AUTOMATIC RESET HIGH-PRESSURE SWITCH
HC
1
CRANKCASE HEATER
TE
IE
1
UTILITY INLET TEMPERATURE PROBE
MAF
AXIAL FAN
TEOE
1
UTILITY OUTLET TEMPERATURE PROBE
MF
MUFFLER
DV
DRAIN
VALVE
LS
LIQUID SEPARATOR
RV
SAFETY VALVE
RS
INTAKE LINE
FL
FLOW SWITCH
RD
DELIVERY LINE
P
PUMP
RL
LIQUID LINE
AV
AUTOMATIC AIR VENTING VALVE
RD/RS
DELIVERY/INTAKE LINE
SM
SERVICE SLEEVE
RS/RD
INTAKE/DELIVERY LINE
Summary of Contents for AWO-M-AC 101.A06
Page 1: ...1 6020930...
Page 46: ...46 6020930 CHILLER MODE DOMESTIC HOT WATER MODE DHW mode Cooling...
Page 49: ...49 6020930...
Page 50: ...50 6020930...
Page 51: ...51 6020930...
Page 52: ...52 6020930...