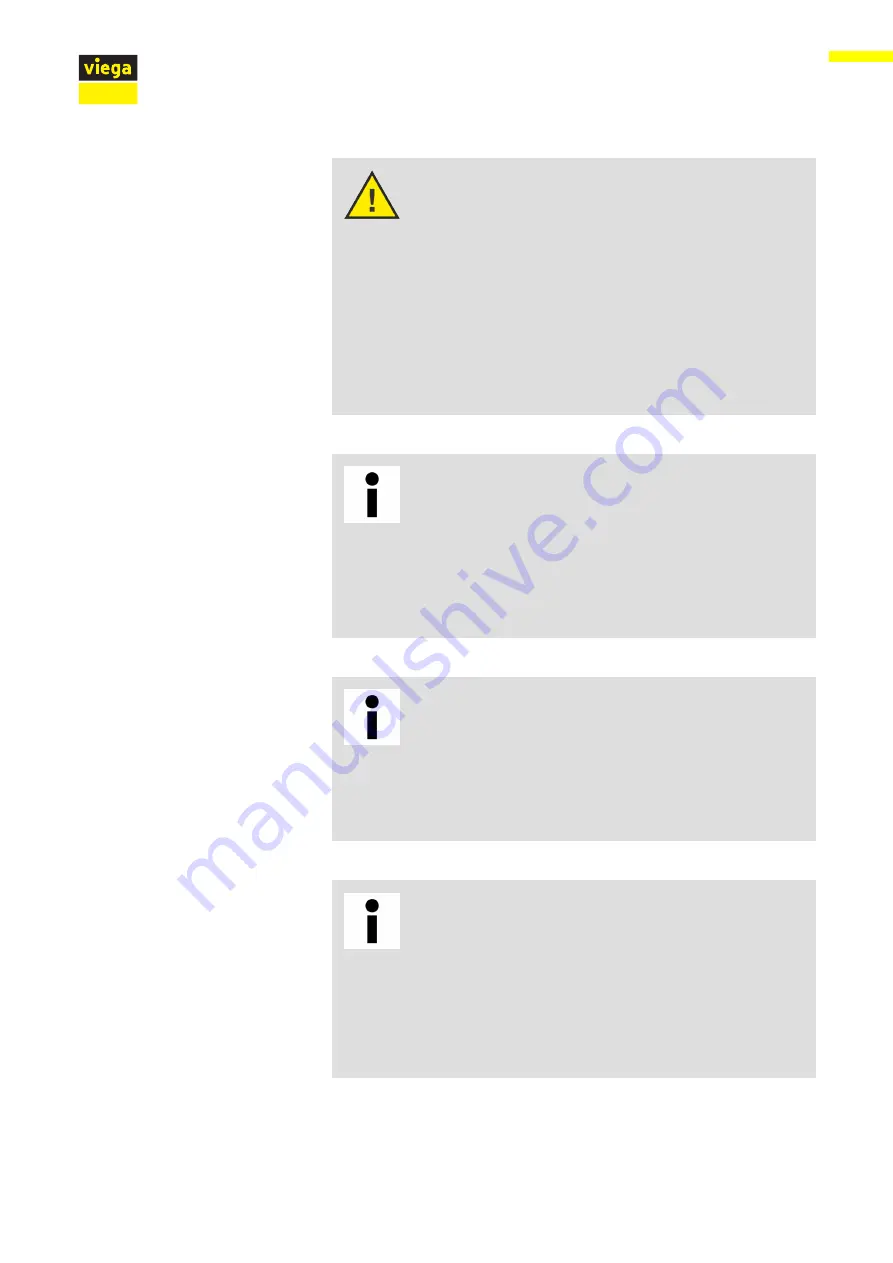
WARNING!
Danger in case of unauthorized third-party
access to the computer network
It cannot be excluded that third parties who can get into
the computer network also gain unauthorized access to
the browser-based software for controlling the flushing
station.
n
Protect your user name and password from third-party
access.
n
A possible break through this access protection
cannot be fully excluded. For this reason, change your
password regularly.
Technical progress
The flushing station has been development pursuant to
state-of-the-art computer and network technology.
It cannot be excluded that the flushing station will not be
compatible with any future computer and network sys‐
tems.
n
Possibly, the flushing station may require technical ret‐
rofitting.
Data protection
The user behaviour of a certain fitting can possibly be
allocated to one individual user. The data collected in this
way is personal data.
n
Inform the user of the flushing station that data is col‐
lected.
n
The user must give his or her consent.
Data protection
It is possible to access the system externally using mobile
end devices. As operator of the flushing station, you are
obliged to check whether the utilization is legally per‐
mitted, in particular if the collected and saved data is sub‐
ject to professional or specific official secrecy.
n
Ensure that personal data is processed and used only
in compliance with the applicable data protection reg‐
ulations.
Product information
Flushing station with Viega technology
9