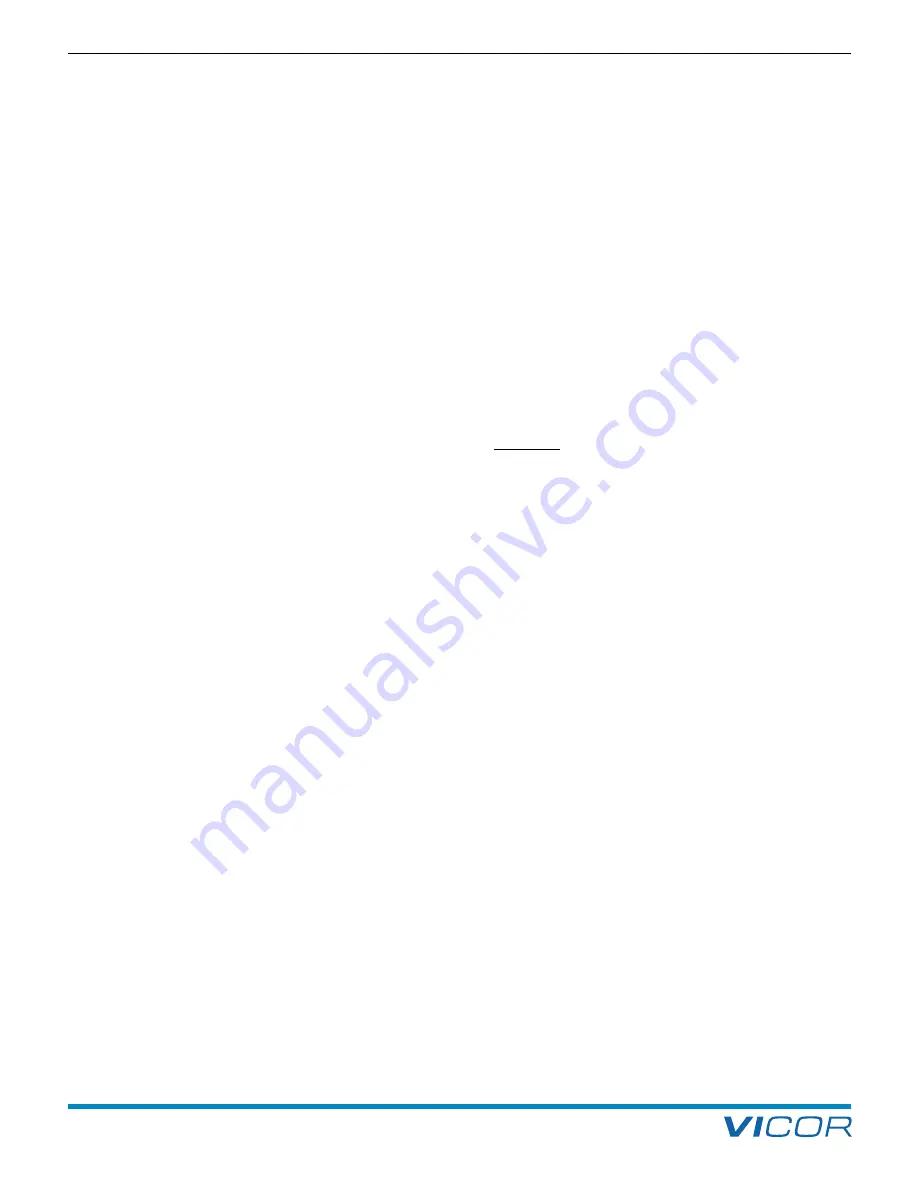
Design Guide & Applications Manual
For VI-200 and VI-J00 Family DC-DC Converters and Configurable Power Supplies
VI-200 and VI-J00 Family Design Guide
Rev 3.4
vicorpower.com
Page 86 of 97
Apps. Eng. 800 927.9474
800 735.6200
23. Recommended Soldering Methods,
Tin Lead Pins, and InMate Sockets
The power module is often much more massive than
other components mounted to the PCB. During wave
solder preheating, the pins will dissipate much of their
absorbed heat within the module. Adjustments to
preheaters alone, therefore, will not improve module
soldering significantly.
A more effective way to improve the soldering of the module
is to lower the conveyor speed and increase the dwell time
in the molten wave. Approximately 5 seconds of exposure
to the molten wave is required to achieve an acceptable
solder joint for a Maxi, Mini, or Micro power module.
Post Solder Cleaning.
Vicor modules are not hermetically
sealed and must not be exposed to liquid, including but
not limited to cleaning solvents, aqueous washing
solutions, or pressurized sprays. Cleaning the backside of
the PCB is acceptable provided no solvent contacts the
body of the module.
When soldering, it is recommended that no-clean flux
solder be used, as this will ensure that potentially
corrosive mobile ions will not remain on, around, or under
the module following the soldering process.
If the application requires the PCB to be subject to an
aqueous wash after soldering, then it is recommended
that Vicor module accessories such as through-hole or
surface-mount sockets be used. These sockets should be
mounted to the PCB and the modules subsequently
inserted following the aqueous washing sequence.
De-soldering Vicor Modules.
Vicor modules should not
be re-used after desoldering for the following reasons:
1. Most de-soldering procedures introduce damaging
mechanical and thermal stresses to the module.
2. Devices or processes that may be capable of
de-soldering a Vicor module from a printed circuit
board without causing damage have not been
qualified for use with Vicor modules. For applications
that require removal of a module with the intent of
reuse, use Vicor socketing systems.
Index of Common Soldering defects.
1.
Solder Bridge.
A short circuit between two electrically
unconnected points caused by a piece of solder
inadvertently forming a “bridge” or connection
between the two points.
Recommended Solution.
Use a smaller soldering tip,
or hold the tip at a different angle when soldering, so
as to only contact one pad at a time.
2.
Cold Solder.
An incomplete or poor connection
caused by either the barrel or the pin not being
heated to the flow temperature of solder. A cold
solder joint will typically exhibit a convex meniscus
with possibly a dark spot around the barrel or pad.
Also a cold solder joint will not be shiny, but will
typically have a “dirty”appearance.
CAUTION: A cold solder joint is not necessarily an
open connection electrically, and cannot be
diagnosed by a simple continuity check. A cold
solder joint is frequently an electrically intermit-
tent connection and is best diagnosed by visual
inspection. A cold solder joint will likely become
electrically open following a period of temp-
erature cycling.
Recommended Solution.
Increase soldering iron
temperature, soldering time, or use a soldering iron
with a higher output wattage if hand soldering. If
wave soldering, lower conveyor speed or increase
preheat temperature.
3.
PC Board Damage.
An intermittent or poor
connection caused by damage to a trace, pad, or
barrel. A damaged pad is best identified by a burn
mark on the PCB, or a trace of pad that moves when
prodded with a mechanical object.
Recommended Solution.
Lower the soldering iron
temperature or the soldering time. If damage persists
use a lower power iron, or consult with the manufacturer
of the PCB for recommended soldering guidelines.
4.
De-wetting.
The solder initially appears to wet but
then pulls back to expose the pad surface, more
common in wave soldering.
Recommended Solution.
Make sure the PCB is clean
prior to soldering.
Summary of Contents for VI-200 Series
Page 100: ......