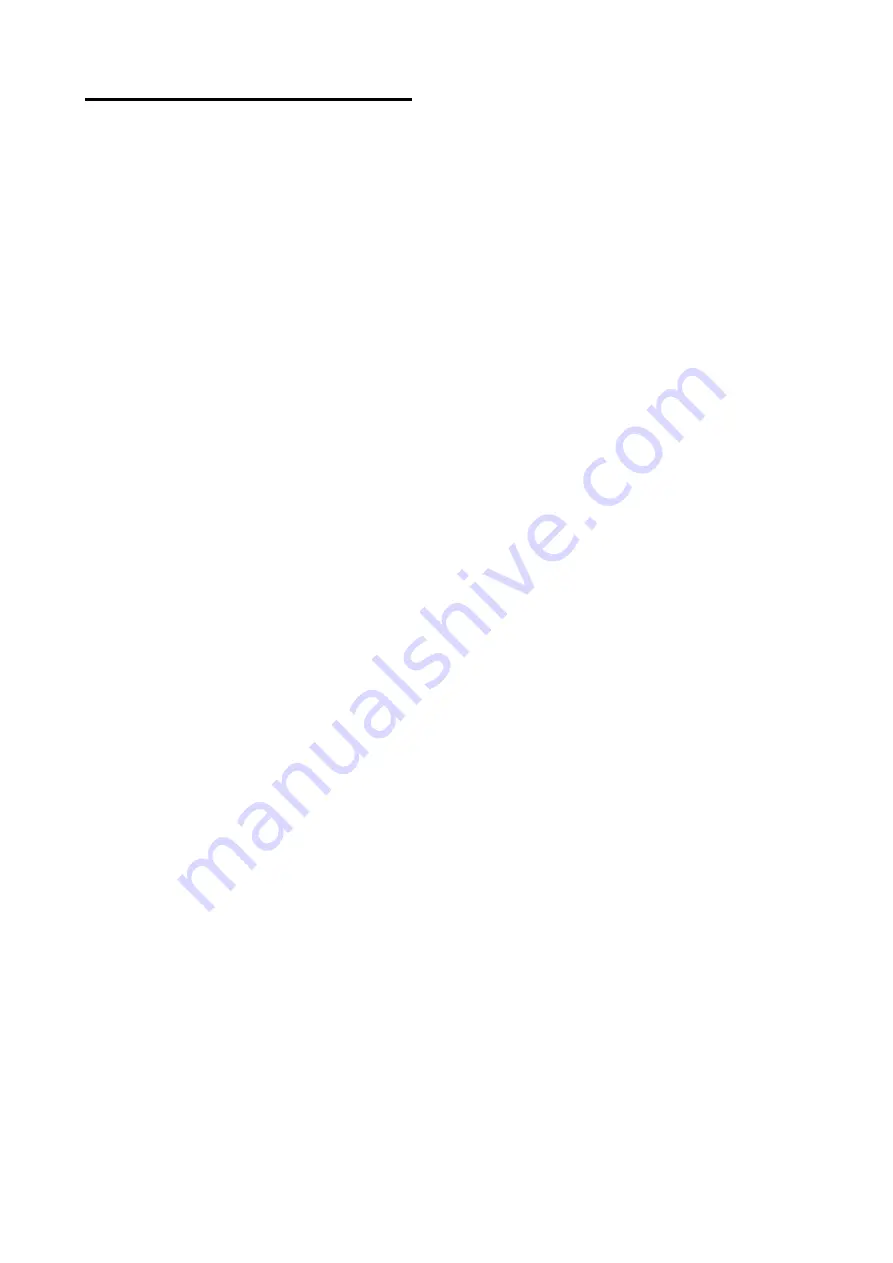
24
11. Warranty and defect liability
ŽDB GROUP, a. s., VIADRUS division grants a warranty:
–
For boilers 24 months after the boiler putting into operation, but maximum 30 months after the date it
was dispatched from the manufacturing factory.
–
For boiler drum 5 years after the date its dispatch from the manufacturing factory.
The user is obliged to leave the furnace installation to an assembly company, putting into operation and
defect removing only to a professional contractual service accredited by the furnace producer ŽDB GROUP
a.s., VIADRUS division otherwise the warranty for proper furnace operation is not valid.
If the furnace is operated according to the instructions mentioned in the “Instructions for the furnace
operation and installation”, the furnace does not require any special professional service interventions.
“Certification of the quality and completeness of the VIADRUS U 22 furnace” serves for filling in by a
contractual service organization as the ”Warranty card”.
For an eventual jacket reclamation is the customer obliged to submit a packing label of the boiler jacket.
It is placed on the cardboard in which the jacket is expedited.
The user is obliged to perform a regular control of the furnace – see Chapter 9.
Failing to keep the mentioned instructions the warrants provided by the producer are not granted.
Each notice of defect must be made immediately after its finding always in written form and by a
phone agreement.
The grant does not apply for:
-
Faults caused by improper assembly and improper attendance of the product and faults caused
by improper maintenance see chap. 9
-
Faults and damage caused by failure to observe water quality in heating system see chap. no. 4.1
and 5.3 or by using the anti-freeze mixture
-
Faults caused by failure to observe instructions stated in this manual
-
Defects caused by a wrong assembly or incorrect operation of the product
-
Damage of the product during transfer or other mechanical damage
-
Defects caused by improper storage
The producer grants the right for changes performed within the frame of product innovation that may
not be included in this instruction
.