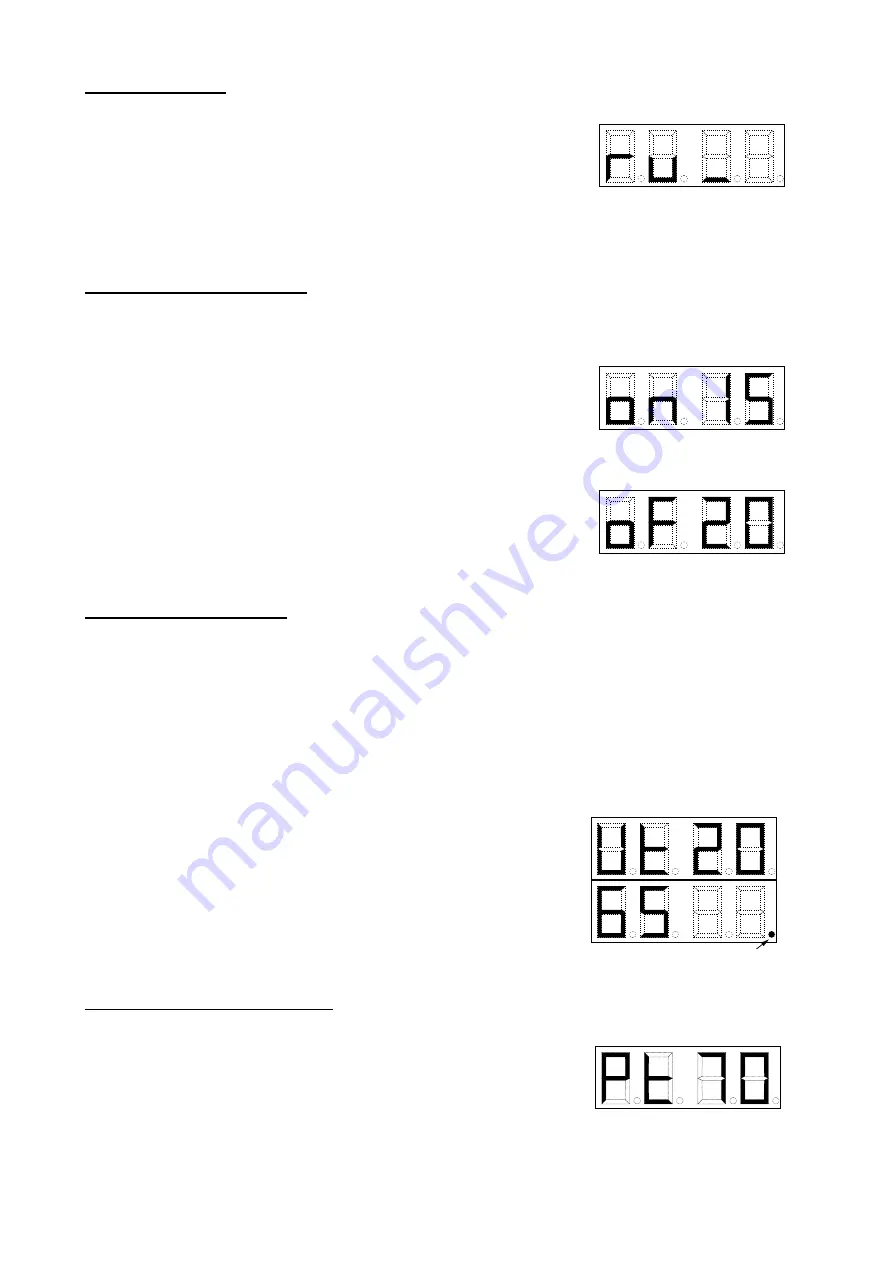
22
1. Manual operation
For the boiler ignition it is necessary to operate manually the fuel
conveyor and ventilator. For this purpose there serve the pushbuttons
1
and
2
. Pushbutton
1
operates the ventilator, pushbutton
2
the fuel
conveyor. By pressing the relevant unit is switched on and by repeated
pressing the relevant unit is switched off. The ventilator operation is
displayed by burning line(stroke) under the ventilator symbol. Once the
ventilator stops the line goes out. The same applies to the fuel conveyor operation indication. It is indicated
by a line(stroke) under the fuel symbol. The fact that the boiler is manually operated is indicated on display
by abbreviation
ru
and burning stroke at the notice
„manual“.
2. Fuel conveyor cycles setting
For a correct boilers function it is necessary to set an optimal proportion between
the time for fuel
feeding
(conveyor works) and the
time for
fuel afterburning
(conveyor in resting stage)
a) By pressing the pushbutton
4
there appears on display the data like
on
15
and it means the operation of fuel reservoir screw conveyor
15
(combustion chamber screw conveyor works parallel, but incl. after-
running). The value can be changed by pressing the pushbutton
*
and
entering a new digit combination like
20
. Then
oF 20
is alight on
display
.
The decision correctness must be confirmed by pushbutton
*
.
Confirmation
o.k.
must appear on display
.
The fuel feeding time can be set within
3 - 90
s, see tab. no.5.
b) By pressing the pushbutton
5
there appears on display the data like
oF
20
and it means that the conveyor is in a resting state for
20
s. The
value can be changed by pressing the pushbutton
*
and entering a
new digit combination like
30
. Then
oF 30
is alight on display
.
The
decision correctness must be confirmed by pushbutton
*
. Confirmation
o.k.
must appear on display
.
The after-combustion time can be set within
3 - 90
s, see tab. no.5.
3. Inhibition duration setting
If the heating water outlet temperature has exceeded the set limit the regulator will shut down the fuel
feeder and ventilator until the temperature drops below the set limit with hysteresis -3 °C. It could happen
that this time is too long and the boiler burns out. That’s why there is set the maximum shut down time so
called.
inhibition duration.
Once it has passed over the ventilator and fuel conveyor start up automatically
within 2 minutes, independently on heating water outlet temperature. Then the regulator comes back into
inhibition status and follows the heating water outlet temperature. The circulating pump is constantly
switched on. The same can be induced by indoor thermostat once the room temperature has been
exceeded. Then besides the induction into the inhibition status there is switched off the circulating pump
while keeping the 4 minutes after-running.
By pressing the pushbutton
6
there appears on display the data like
Ut 20
and it means the
20
minutes
inhibition duration. The value can be changed by pressing the
pushbutton
*
and entering a new digit combination like
30
. Then
oF 30
is
alight on display
.
The decision correctness must be confirmed by
pushbutton
*
. Confirmation
o.k.
must appear on display
.
The inhibition
duration can be set between
5 and 90
minutes. Recommended value is
30
min. If in this regime the heating water temperature significantly rises
(first of all in summer season, when there is a minimum heat take-off
from the system), it is recommended to increase this value.
Inhibition on display is indicated by a burning point in its right lower
corner.
4. Outlet water temperature setting
The required outlet water temperature
is set by means of pushbutton
3
. On display there appears the
data like
Pt 70
and it means the required outlet water temperature of
70
°C. The value can be changed by pressing the pushbutton
*
and entering
a new digit combination like
75
. Then
Pt 75
is alight on display. The
decision correctness must be confirmed by pushbutton
*
. Confirmation
o.k.
must appear on display
.
The required outlet water temperature can
be set between
60 and 90
°C. It is recommended to operate boiler at temperatures higher than
65
°C.
Indikace útlumu
Inhibition