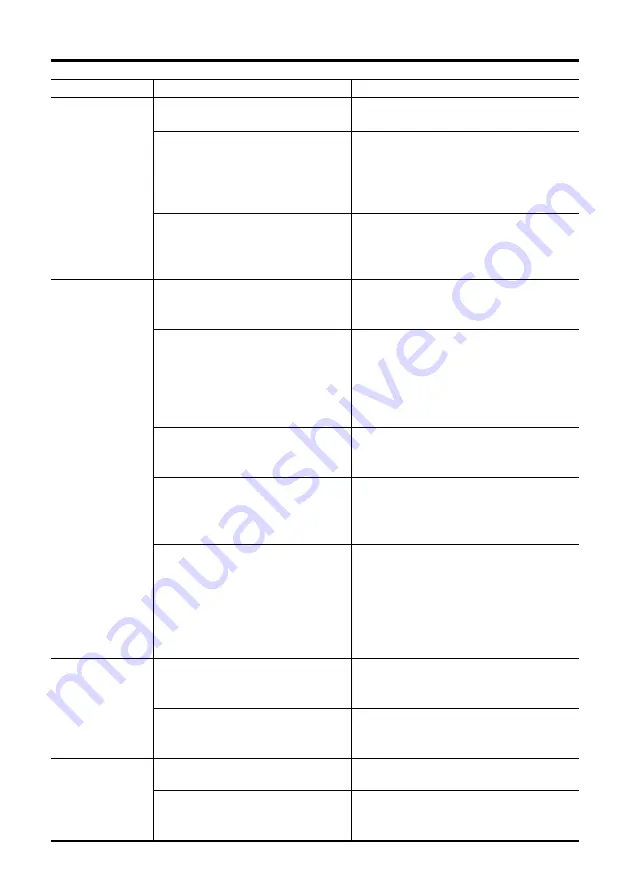
32
Phenomenon
Motor operation
is unstable.
Loss of
synchronization
during
acceleration or
running
Motor does not
move the set
amount.
Current does
not drop when
the motor
stops.
Remedial action
Double-check that the driver and
motor connections are correct.
Return the current-adjustment controls
to its factory setting and check.
• Check the controller and driver
connections.
• Check the pulse-input specifications
(voltage and width).
Check the linkage state for the motor’s
output shaft and load shaft.
Check for large load fluctuations
during motor operation. If adjusting
the motor’s operating speed to low and
high torque eliminates the problem, it
is necessary to review the load
conditions.
Lower the speed of the starting pulse
and set it again to a speed at which
stable starting is possible.
Lengthen the acceleration
(deceleration) time in order to reset it
to a time at which stable starting is
possible.
Check running with only the motor,
driver and required controller. If the
impact of noise is recognized, take
countermeasures, such as rewiring for
greater distance from the noise source,
changing the signal cables to shielded
wire, or mounting a ferrite core.
Check the step-angle setting switch
(DATA1, DATA2) settings and the
C/S input switching state.
Check whether or not the number of
pulses required for operation at the set
step angle are being output.
Switch the current check switch to
“OFF.”
After the pulses stop, always switch
to “OFF.”
Possible cause
Error in the motor’s cable
connection
Current-adjustment control
incorrectly set
If the setting is too low, the
motor torque will also be too low
and operation will be unstable.
Pulse-input line connection
defect
The centers of the motor’s
output shaft and load shaft are
not aligned.
The load or load fluctuation is too
high.
The speed of the starting pulse
is too high.
The acceleration (deceleration)
time is too short.
Electrical noise
Mistake in switching C/S (step-
angle switching) input
Pulse-output count is too low or
too high.
Current-check switch to “ON”
CW input, CCW input or pulse
input set to “ON” after pulses
have stopped