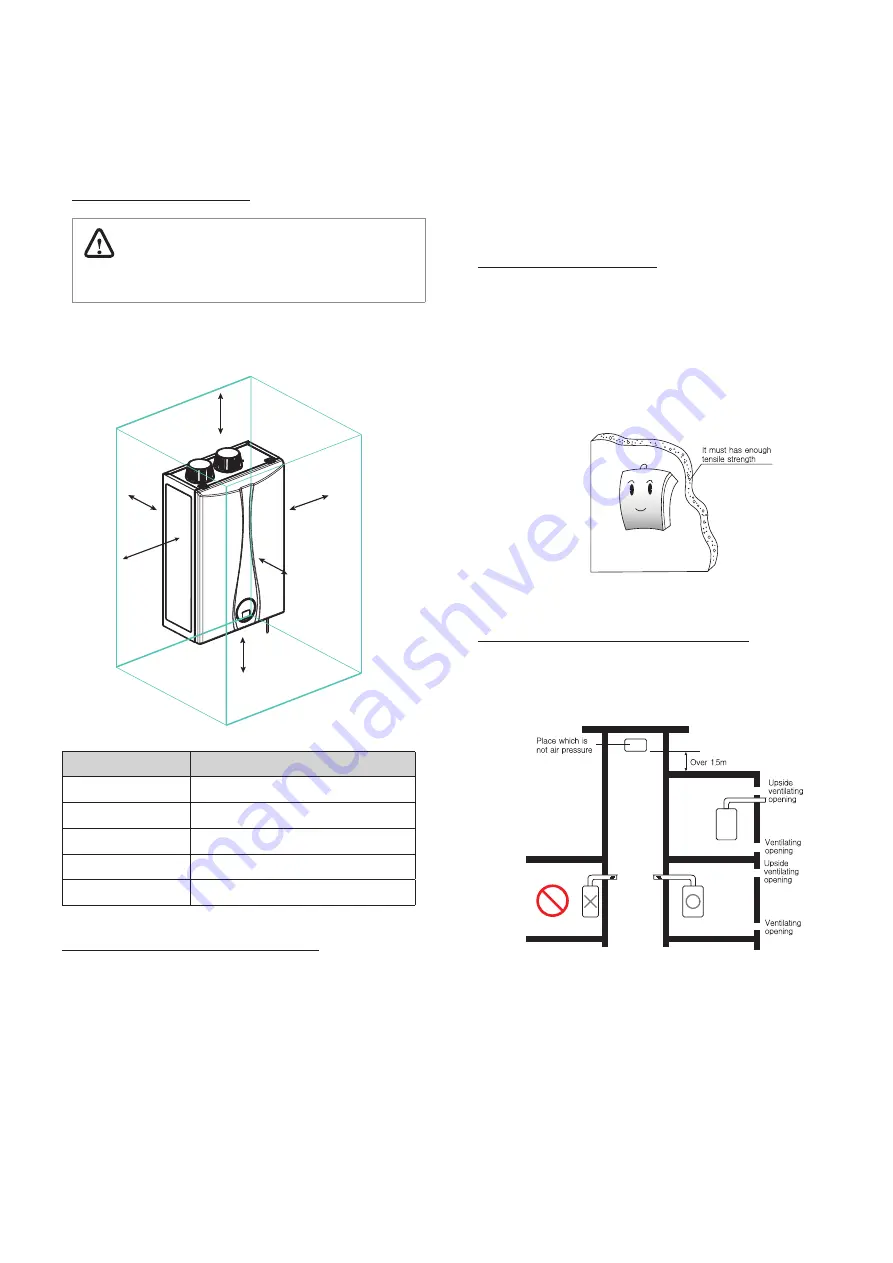
Installing the Boiler 15
Clearance from
:
Indoor Installation
Top
9 in 229 mm minimum
(
)
Back
0 5 in 13 mm minimum
.
(
)
Front
4 in 100 mm minimum
(
)
Sides
3 in 76 mm minimum
(
)
Bottom
12 in 300 mm minimum
(
)
Clean debris and chemical free combustion air
,
-
●
Do not install the boiler in areas where dust and debris may
accumulate or where hair sprays spray detergents chlorine or
,
,
,
similar chemicals are used
.
●
Do not install the boiler in areas where gasoline or other
flammables are used or stored
.
●
Ensure that combustible materials are stored away from the
boiler and that hanging laundry or similar items do not obstruct
access to the boiler or its venting
.
Adequate installation clearances
CAUTION
Do not install the boiler on carpeting
.
Install the boiler in an area that allows for service and maintenance
access to utility connections piping filters and traps Based on
,
,
,
.
the installation location ensure that the following clearances are
,
maintained
:
Top
Back
Side
Bottom
Front
Side
2 2
.
How to install
Please install on a durable wall.
●
When install the product, about 66 lb(31kg) is added in a wall.
So if it is not installed on solid wall, it may cause damages,
●
If there is not enough strength to preserve the product, please do
●
The weight of the product is marked on 8page of this manual.
●
Make sure the unit is mounted on a non-combustible material.
submersion, gas leak and a fire by falling the product
reinforcement work.
Please don
’
t install on a froup exhaust port wall.
●
It may cause mounting screw corrosion and result in failure.
●
It may cause damages, submersion, gas leak and a fire from
unit falling.