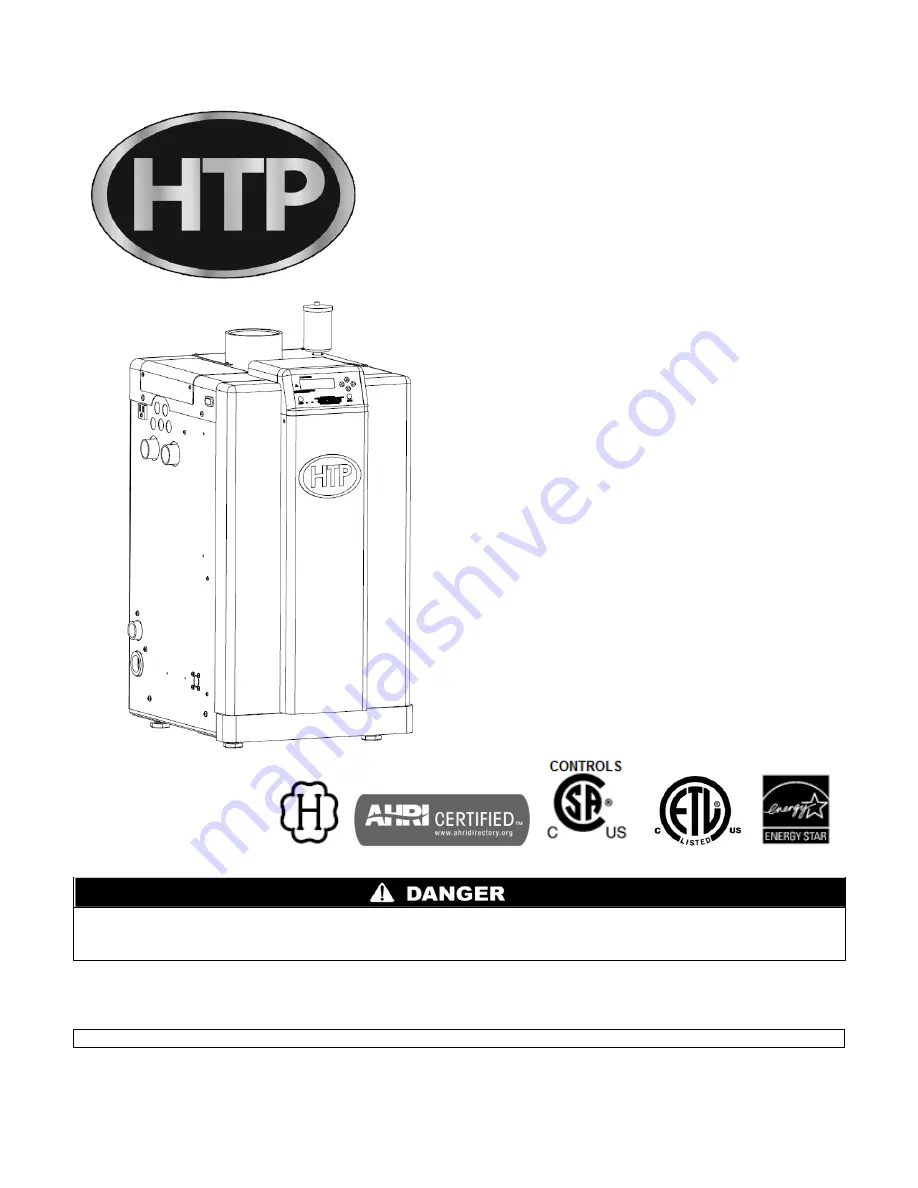
120 Braley Rd. P.O. Box 429
East Freetown, MA 02717-0429 www.htproducts.com
LP- 293 REV. 3.29.12
Elite
INSTALLATION
START-UP
MAINTENANCE
PARTS
Elite Models*
EL-80 / 110 / 150 / 220 / 299 / 399
*A suffix of “LP” denotes propane gas
*A suffix of “N” denotes natural gas
NOTICE:
HTP reserves the right to make product changes or updates without notice and will not be held liable for
typographical errors in literature.
NOTE TO CONSUMER: PLEASE KEEP ALL INSTRUCTIONS FOR FUTURE REFERENCE.
This manual must only be used by a qualified heating installer/service technician. Read all instructions in this
manual before installing. Perform steps in the order given. Failure to comply could result in substantial property
damage, severe personal injury, or death.
Summary of Contents for EL-110
Page 15: ...15 Figure 3 ...
Page 61: ...61 Figure 29 ...
Page 62: ...62 Figure 30 ...
Page 87: ...87 Figure 33 ...
Page 88: ...88 Figure 34 ...
Page 89: ...89 Figure 35 LP 293 A NOTE Parts listed on the following page ...
Page 94: ...94 ...
Page 95: ...95 ...
Page 96: ...96 MAINTENANCE NOTES ...