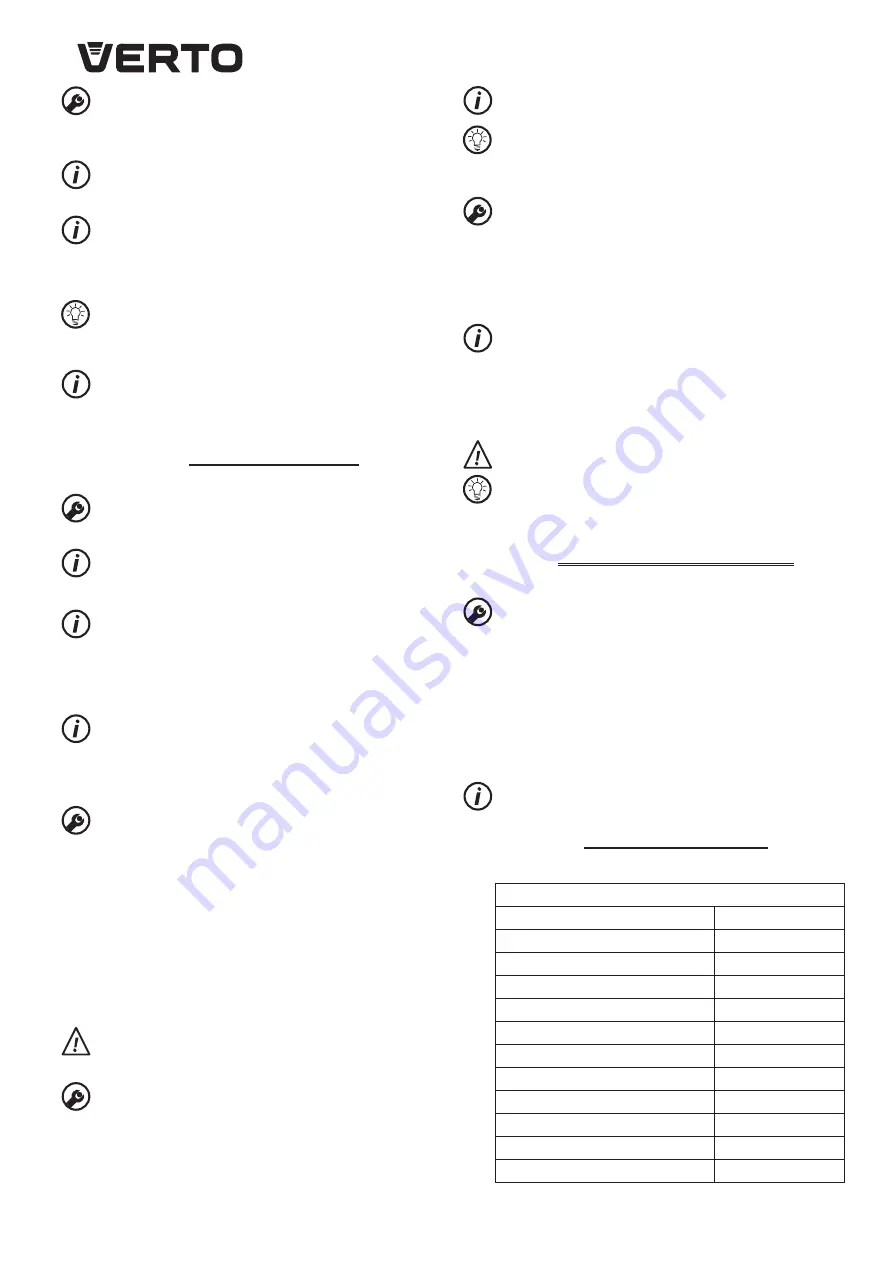
10
•
Put the charger cable plug into charger socket (
4
) in the drill body
(
fig. A
).
•
C
onnect the charger (
7
) to mains socket
23
0 V
AC
.
•
Red L
E
D will light up (
8
) on the charger (
7
) (
fig. B
).
• Red diode light (8)
– voltage is on and the battery charging is
in progress.
• Green diode light (8)
– the battery is fully charged.
L
E
D (
8
) will keep on green until the charger is disconnected from
the mains socket.
A
fter discharge a minimum
3
–
5
hour of recharge
is required to reach full battery level. In normal use the drill battery
allows for multiple chargings. To maintain the drill in good condition
recharge its battery at least once per six months.
Batteries heat up strongly when charging. Do not operate just
after charging – wait for the battery to cool down to room
temperature. It will prevent battery damage.
SPINDLE BRAKE
Drill is equipped with electronic brake, which stops the spindle
immediately after the switch button (
5
) is released. The brake
ensures precision when screwing or drilling and prevents free
spindle rotation after switching off.
OPERATION / SETTINGS
SWITCHING ON / SWITCHING OFF
Switching on –
press the switch button (
5
).
Switching off –
release the switch button (
5
).
E
ach time the switch button (
5
) is pressed, the L
E
D diode (
6
) ligths
up to illuminate the workplace.
ROTATIONAL SPEED CONTROL
Increase or reduce pressure on the switch button (
5
) to adjust
drilling or driving speed while operating. Speed adjustment allows
for a soft start, which prevents dill slipping when drilling holes in
gypsum or glaze, and allows for operation control when screwing
in and out.
OVERLOAD CLUTCH
Set the torque adjustment ring (
2
) in appropriate position to
permanently set overload clutch to defined torque value. When the
set torque is reached, overload clutch disconnects automatically. It
prevents screwing screws too deep or damaging the drill driver.
TORQUE ADJUSTMENT
•
Different screws and materials require different torque to be
applied.
•
The bigger the number corresponding to given position, the
bigger is the torque (
fig. C
).
•
Set the torque adjustment ring (
2
) to appropriate torque value.
•
A
lways start operation with low torque.
•
Increase the torque gradually until obtaining desired results.
•
Use higher settings to unscrew screws.
•
When drilling, choose setting marked with the drill symbol. The
torque is the greatest with this setting.
•
Knowledge how to choose appropriate torque setting comes with
practice.
Setting the torque adjustment ring in the drilling position
deactivates the overload clutch.
WORKING TOOL INSTALLATION
•
Set the direction selector switch (
3
) in the middle position.
•
Hold the rear ring of the quick release chuck (
1
) and turn front ring
counter-clockwise to open jaws appropriately and insert drill or
driver bit (
fig. D
).
•
Hold the rear ring of the quick release chuck (
1
), turn front ring
clockwise and tighten firmly to install working tool.
Deinstallation of the tool is similar to installation, only the sequence
of actions is reversed.
Make sure the tool position is correct when installing drill or
driver bit in the quick release chuck. Use additional magnetic
adapter as an extension when using short driver bits.
LEFT – RIGHT DIRECTION OF ROTATION
C
hoose direction of spindle rotation with the direction selector
switch (
3
) (
fig. E
).
Right rotation – set the switch (
3
) to the extreme left position.
Left rotation – set the switch (
3
) to the extreme right position.
* In certain cases position of the switch in relation to rotation may be different
than specified. Please refer to graphic signs placed on the switch or tool body
Safe position of the direction selector switch (
3
) is in the middle, it
prevents accidental starting of the power tool.
•
Drill cannot be started, when the switch is in this position.
•
Use this position of the switch to change drills or bits.
•
Before starting the tool make sure the position of the direction
selector switch (
3
) is correct.
Do not change direction of rotation when the drill spindle is
rotating.
Long lasting drilling at low rotational speed of the spindle
may cause motor overheating. Provide regular breaks during
operation or let the tool operate at maximum speed with no load
for approximately 3 minutes.
OPERATION AND MAINTENANCE
QUICK RELEASE CHUCK REPLACEMENT
Quick-release chuck is screwed onto spindle of the drill and
additionally secured with a screw.
•
Set the direction selector switch (
3
) in the middle position.
•
Open jaws of the quick release chuck (
1
) and unscrew the fixing
screw (left-hand thread) (
fig. F
).
•
Install hexagonal key in the quick release chuck and tap the other
end of the key.
•
Unscrew the quick release chuck.
•
Installation of the quick release chuck is similar to deinstallation,
only the sequence of actions is reversed.
A
ll defects should be repaired by service workshop authorized by
the manufacturer.
TECHNICAL PARAMETERS
RATED PARAMETERS
Cordless drill
Parameter
Value
Battery voltage
10,8 V D
C
Battery type
Li-Ion
Battery capacity
1
3
00 m
A
h
Range of idle rotational speed
0-
55
0 rpm
Range of quick release chuck
0,8-10mm
Torque control range
1 –
2
0 plus drilling
Max. torque (soft drive)
11 Nm
Max. torque (hard drive)
25
Nm
Protection class
III
Weight
0,9
5
kg
Year of production
2
017
Summary of Contents for 50G271
Page 2: ...2 ...
Page 3: ...3 1 D B 4 8 7 E 5 6 3 2 2 C F A 4 1 2 3 4 5 6 ...
Page 63: ...63 ...
Page 64: ......