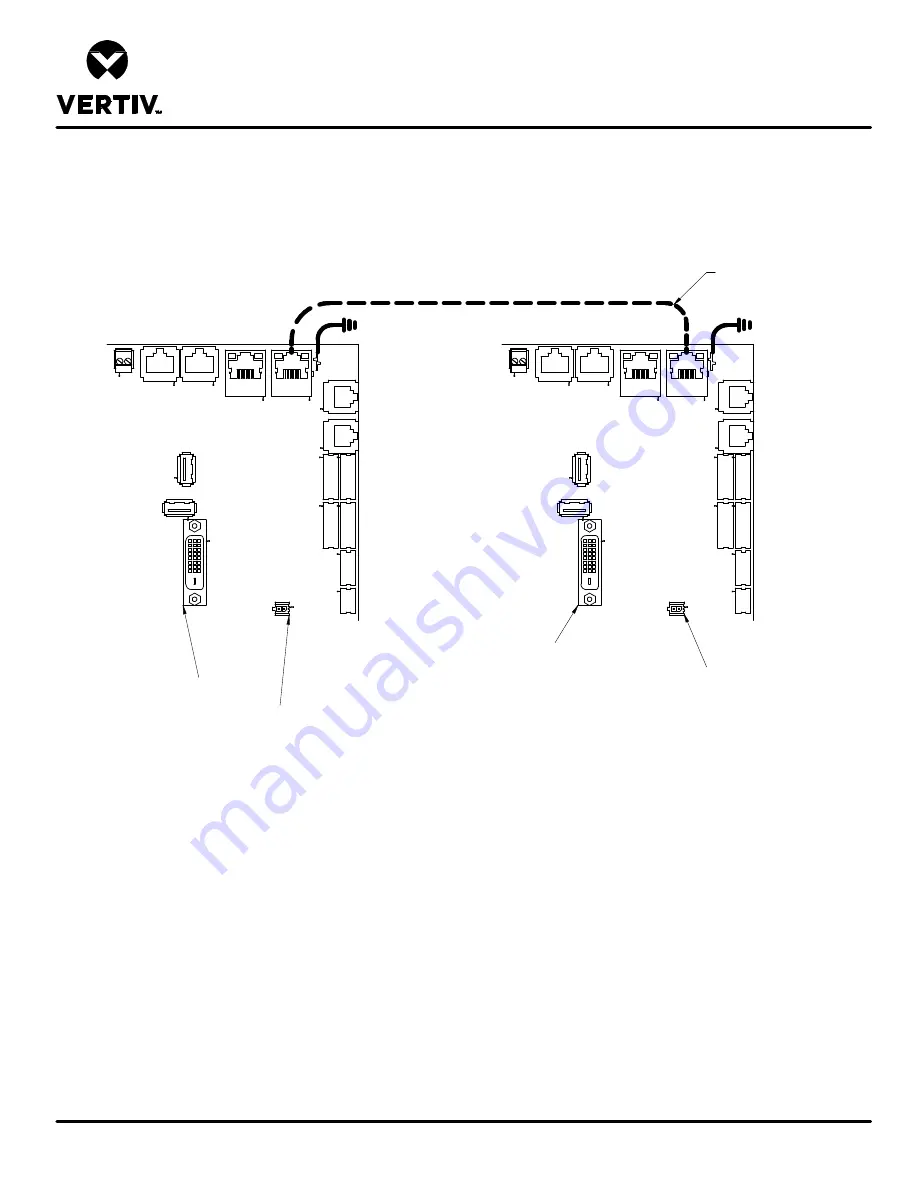
REV : 2
REV DATE : 6/18
DPN004351
Page :2 /2
F
or
m
N
o.
: D
P
N
00
10
40
_R
E
V
4
UNIT TO UNIT NETWORK CONNECTIONS
LIEBERT DS, DSE, CW, PDX & PCW
ETHERNET CABLE
(FIELD SUPPLIED)
TB3
P71
P72
P74
P64
E5
P
67
P
66
P
11
P
12
P
21
P
20
P
13
P
7
P76
P95
P100
P75
2
iCOM
MICROPROCESSOR
AND I/O BOARD
TB3
P71
P72
P74
P64
E5
P
67
P
66
P
11
P
12
P
21
P
20
P
13
P
7
P76
P95
P100
P75
2
iCOM
MICROPROCESSOR
AND I/O BOARD
NOTE* For dual-unit network configurations only
P95 DVI-D CABLE CONNECTION
TO 7-INCH ICOM DISPLAY
P100 POWER SUPPLY TO
7-INCH ICOM DISPLAY
P95 DVI-D CABLE CONNECTION
TO 7-INCH ICOM DISPLAY
P100 POWER SUPPLY TO
7-INCH ICOM DISPLAY
Summary of Contents for Liebert CW
Page 10: ...Vertiv Liebert CW Installer User Guide 6 This page intentionally left blank...
Page 24: ...Vertiv Liebert CW Installer User Guide 20 This page intentionally left blank...
Page 32: ...Vertiv Liebert CW Installer User Guide 28 This page intentionally left blank...
Page 34: ...Vertiv Liebert CW Installer User Guide 30 This page intentionally left blank...
Page 36: ...Vertiv Liebert CW Installer User Guide 32 This page intentionally left blank...
Page 46: ...Vertiv Liebert CW Installer User Guide 42 This page intentionally left blank...
Page 48: ...Vertiv Liebert CW Installer User Guide 44 This page intentionally left blank...