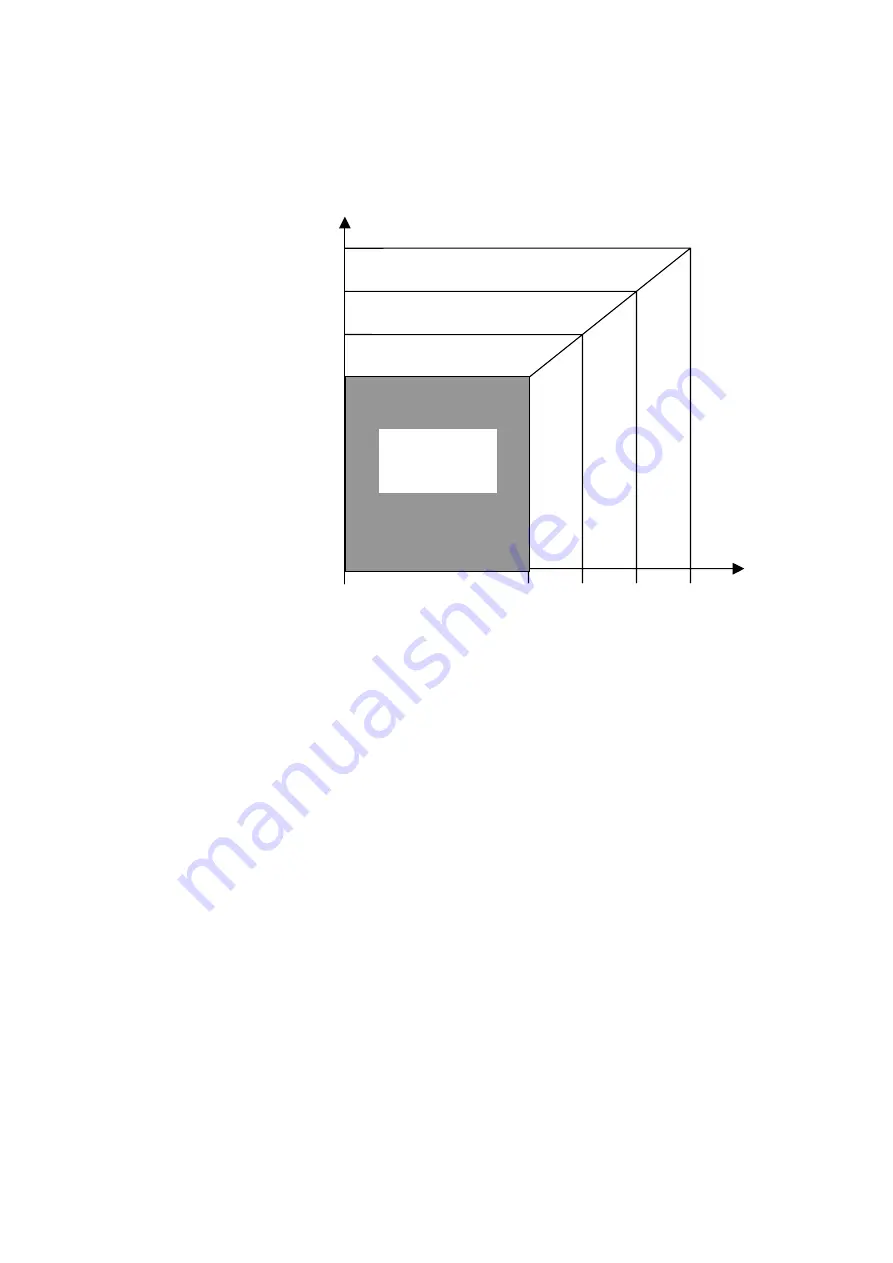
6
The stove may be fitted below a combustible shelf providing there is a minimum distance of
250mm above the top of the stove and the shelf does not project more than 150mm. If the
shelf overhangs more than 150mm the distance between the fire and the shelf must be
increased by 15mm for every 25mm of additional overhang over 150mm. See Graph below
1.4 CLEARANCES TO COMBUSTIBLE BEAMS WITHIN INGLENOOKS – TOP FLUE
FITTING
The stove may be below a combustible beam providing there is a minimum distance of
610mm above the top of the stove and that it does not extend in front of the stove. There
must be a minimum distance of 300mm to any combustible side or rear surface, and 100mm
to any non-combustible side or rear surface.
1.5 FLUE / CHIMNEY INSPECTION
Forward Shelf Projection Allowed (mm)
Shelf Height
Above Top of
Stove (mm)
0
150
175
200
225
295
280
265
250
0
Stove Must Not be
fitted below a Shelf
Height of 250mm