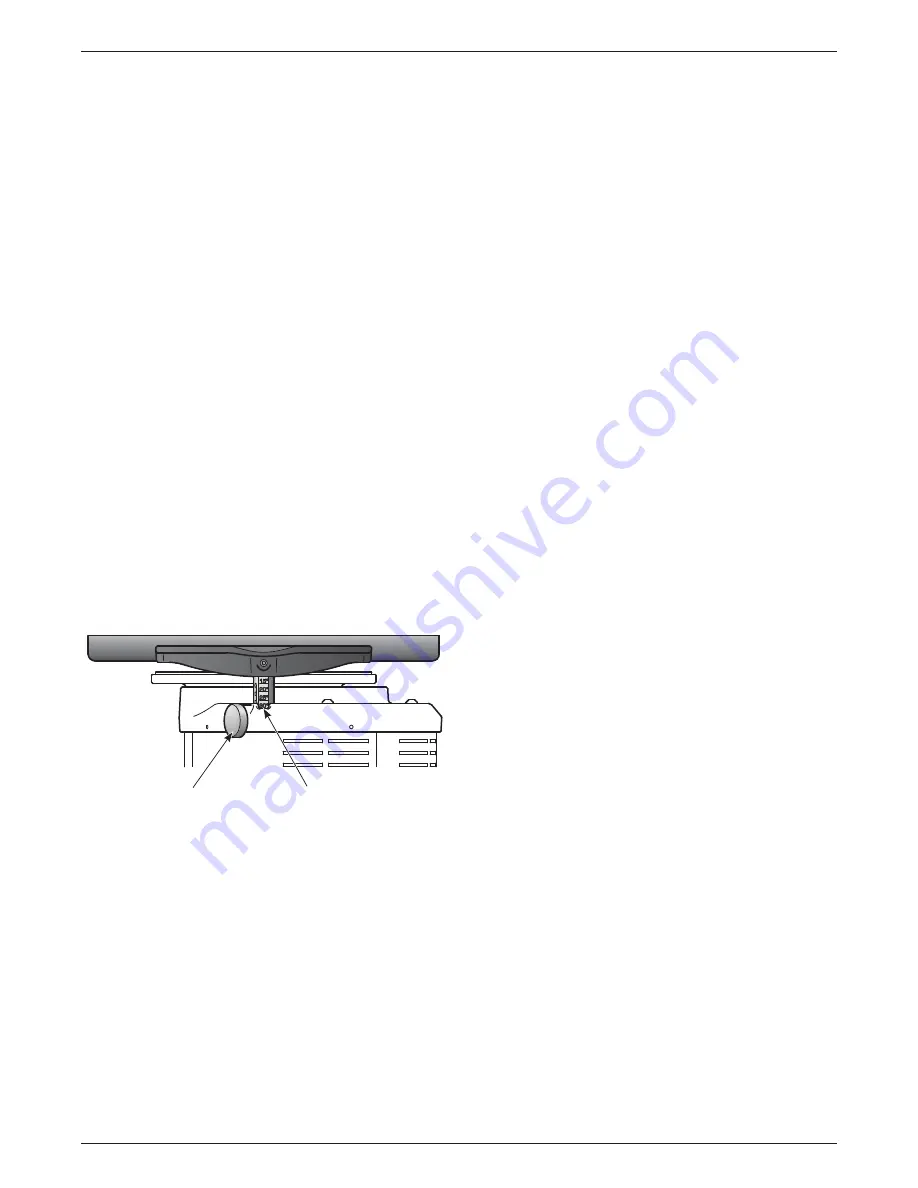
12
Veritas
®
Mk.II Power Sharpening System
Tool Registration
The system relies on the tool holder to be used
with the tool registration jig and the tool guide to
grind and hone accurate, repeatable bevel angles.
As illustrated in
Figure 8
, the blade should always
project the same distance from the holder, with
the exception of especially short tools (see
Short
Projection
). Different bevel angles are achieved
solely by varying the height of the tool guide. The
tool guide post has a series of indents that engage a
ball plunger installed in the base. This creates seven
pre-determined settings for the tool guide height as
shown on the tool guide scale (from 15° to 45° in
5° increments). As the post is moved up and down,
it will register at each 5° setting with a small click.
The corresponding bevel angle is read according to
the lowest number that can be read from the scale
as shown in
Figure 11
. The guide may be set to
any height between the two extremes; however, if
the angle required is not one of the presets, you will
need to mark the position with a fine-tip marker on
the label, or with a scratch or other mark on the post
itself, for the setting to be repeatable. If unusual
bevel angles are required more often than the seven
presets, you can back off the ball plunger to eliminate
the standard presets by first removing the locking
screw (to access the ball plunger).
Abrasives
The types and grades of abrasives used with the system
have been carefully selected for fast material removal
and cool grinding temperatures. As with all sharpening
methods, the sharpening system uses a range of
abrasives from very coarse to very fi ne. Each grade is
suitable for a specifi c stage of the sharpening process.
Four different grades are included with each system for
use on the turntable. They are as follows:
•
80x (180µ) zirconia
– applied to one side of the
thick (4mm) platter, and used for basic shaping of
the bevel and grinding out edge damage.
•
100µ (150x) aluminum oxide
(1µ = 1 micron
=
1
/
1,000,000
metre) – applied to other side of the
thick (4mm) platter. The micron grade refers to
the average particle size. This abrasive is the
first to be used if the blade was last sharpened on
the system at the same angle and no large nicks
or chips are to be removed from the edge. This
abrasive must also be used if a blade was started
with the 80x platter because, as with all abrasive
action, when progressing from coarse to fine, one
should not make too large a jump from one grade
to the next.
•
40µ (320x) aluminum oxide
– applied to one side
of the thin (3mm) platter. This grade is used
only
for lapping the face of a chisel or plane blade.
In normal sharpening (i.e., when working on the
bevel), this abrasive is not used.
•
9µ (1200x) aluminum oxide
– applied to the
other side of the thin (3mm) platter. This abrasive
is used to create the micro-bevel with the final
cutting edge.
Micro-Bevels
As explained in
Appendix C: General Sharpening
Procedures
, concentrating one’s honing efforts on a
micro-bevel will save a great deal of time and abrasive.
When using this system, a very slight change of angle is
automatically created when the user switches from the
coarse abrasive discs mounted on the thick platter to the
fi ne abrasive discs mounted on the thin platter. The user
needs to do nothing more than switch to the platter with
the fi ne abrasive to achieve a micro-bevel of about 1°.
Figure 11: Setting the bevel angle.
Locking Screw
Read angle here.
Summary of Contents for Mk.II
Page 6: ...vi Veritas Mk II Power Sharpening System ...
Page 14: ...8 Veritas Mk II Power Sharpening System ...
Page 20: ...14 Veritas Mk II Power Sharpening System ...
Page 33: ...27 Exploded Assemblies Master Parts List 5 3 13 9 7 2 14 24 21 1 6 22 20 19 18 17 16 15 23 4 ...