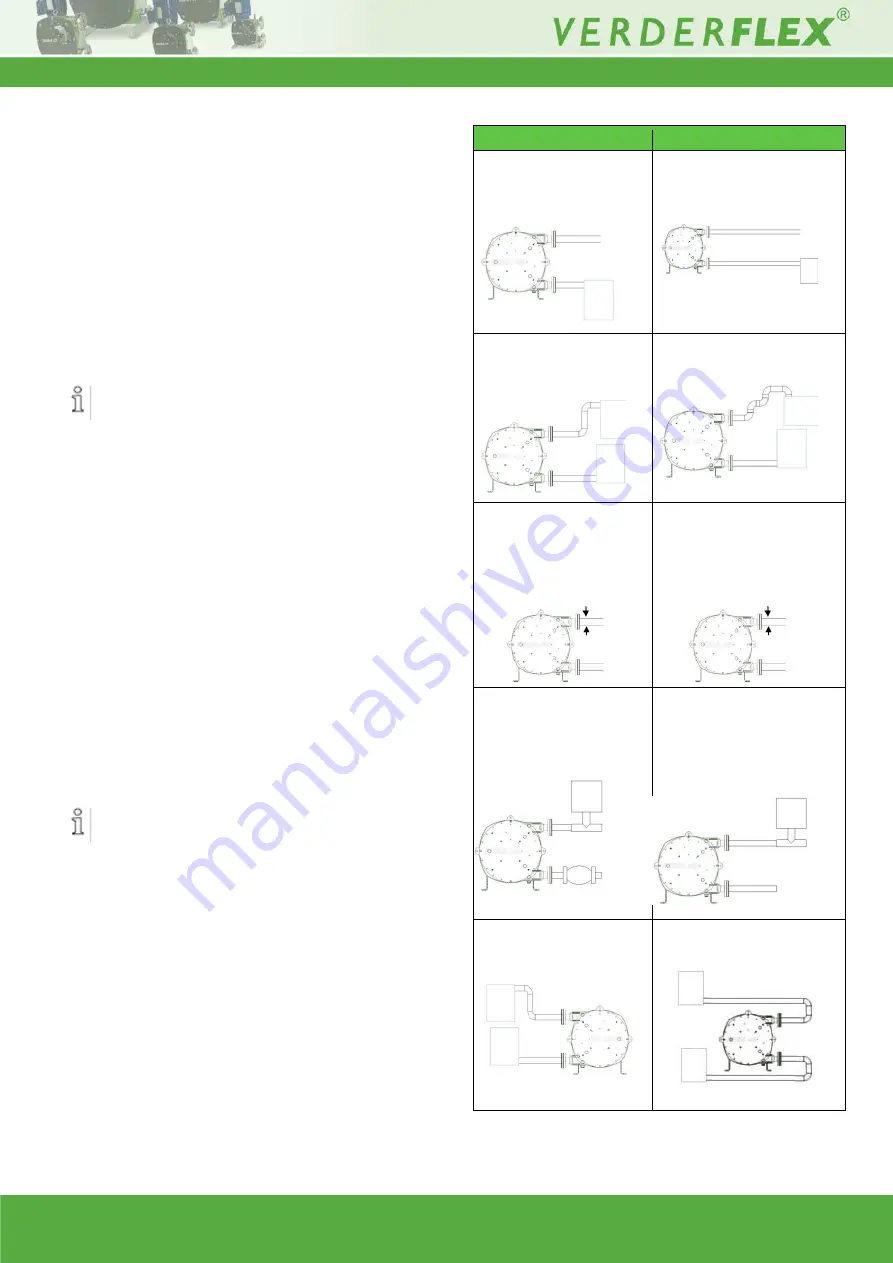
Dura 5 - 35
4.0v-06.2013
10 | Page
5.3
Planning the pipes
5.3.1
Specifying supports and flange connections
1.
When planning pipe runs take every possible
operating condition into account:
–
Cold/warm medium
–
Empty/full
–
Unpressurized/pressurized
–
Positional change of the flanges
2.
Ensure that the pipe supports are designed to
accommodate any movement from environmental or
pressure imposed forces.
5.3.2
Specifying nominal diameters
Keep the flow resistance in the pipes as low as
possible. Pipe work immediately connected to both
inlet and outlet port of the pump should be straight
runs for at least 1 meter.
Ensure that nominal pipe diameter is at least 1.5 times
nominal pump-hose diameter to reduce pulsation.
5.3.3
Specifying pipe lengths
1.
Keep pipe work as short and direct as possible.
2.
To allow easy access when changing hoses, include a
short, removable section adjacent to the port flanges.
5.3.4
Optimizing cross-section of pipe work
1.
Avoid bending radii of less than 1.5 times the nominal
pipe diameter.
2.
Avoid abrupt changes of cross-section along the
piping.
5.3.5
Providing safety and control devices
(recommended)
Making provisions for isolating and shutting off pipes
For maintenance and repair work.
Provide shut-off valves in the suction and discharge
lines.
Allowing safe removal of product
Include drainage taps in suction and discharge lines at
the lowest point.
Do’s
Don’t
1. Short pipe run to
suction side
Long pipe run to suction
side
2. Reduced
Joints/Bends
Multiple Joints/Bends
3. Connecting pipe with
diameter 1.5 times
pump hose diameter
Connecting pipe with
smaller than pump hose
diameter
4. Pulsation damper
connected close to the
pump
Pulsation damper
connected away from
pump
5. Pump installed in the
right direction.
Piping bend away from
pump.
Table 4
Do’s and Don’ts
10% loss in damper efficiency for
every meter
Pulsation Damper
Bellows
Pipe ID < Pump hose ID
Pipe ID 1.5 times hose ID
Summary of Contents for Dura 10
Page 28: ...Dura 5 35 4 0v 06 2013 28 Page...