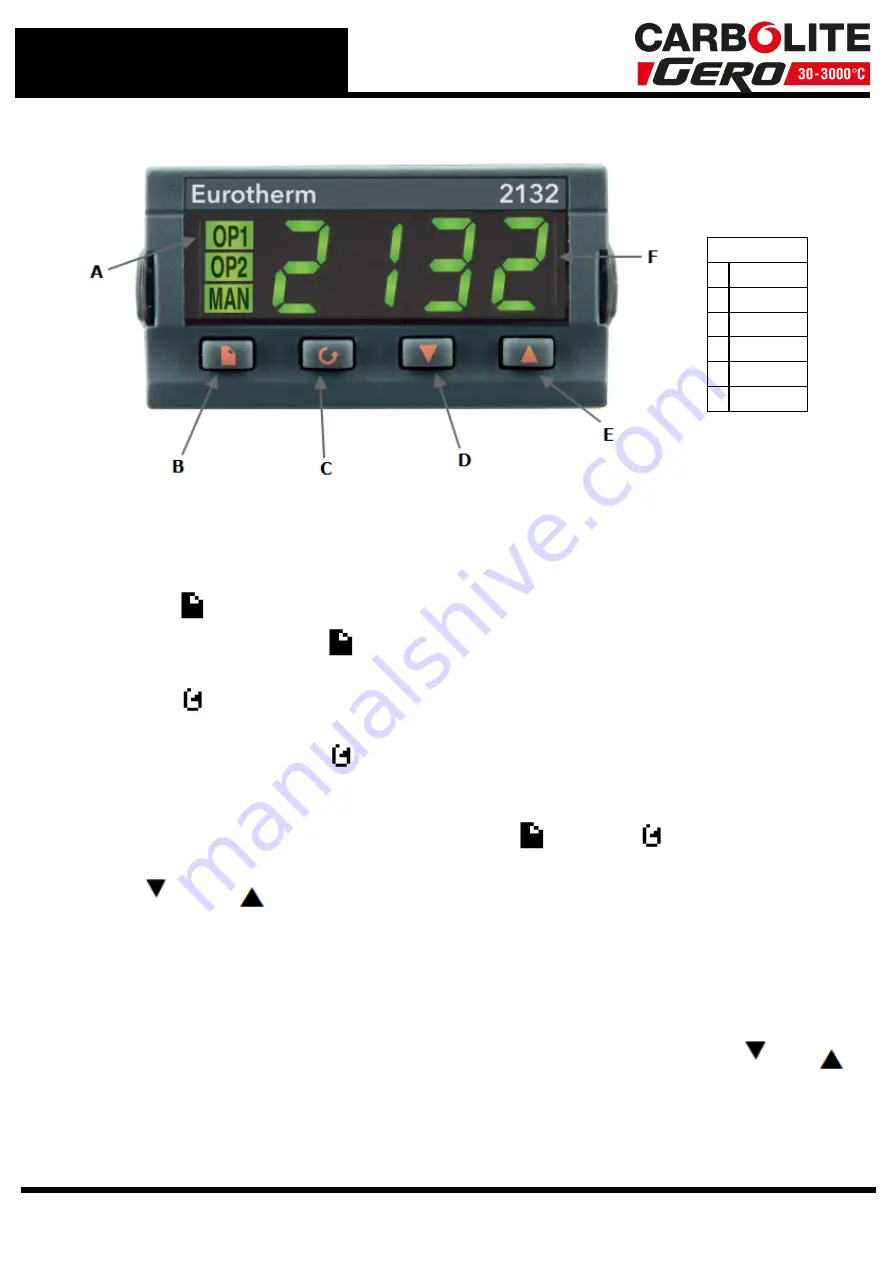
3.0 2132 Controller
3.2.2
2132 Controller Operation
Key
A
Alarm Light
B
Page
C
Scroll
D
Down
E
Up
F
Display
When switched on, the controller lights up, goes through a short test routine and then
displays the measured temperature or the over-temperature setpoint.
The page key
allows access to parameter lists within the controller.
A single press of the page key
displays the temperature units, normally set to °C;
further presses reveal the lists indicated in the navigation diagram. See section 4.4.
The scroll key
allows access to the parameters within a list. Some parameters are
display-only; others may be altered by the operator.
A single press of the scroll key
in the 'Home' list displays the temperature units;
further presses reveal the parameters in the current list indicated in the navigation
diagram.
To return to the 'Home' list at any time, press page
and scroll
together, or wait
for 45 seconds.
The down
and up
keys are used to alter the setpoint or other parameter values.
3.2.3
Basic Operation
Normally no operator action is required other than entering the setpoint, as the
controller starts to control on being switched on, as described above.
3.2.4
Altering the Setpoint
With the display at 'Home', showing the measured temperature, press down
or up
once to display the setpoint; press again or hold down to adjust it. The display returns to
the measured temperature when no key is pressed for 30 seconds.
10
Summary of Contents for CARBOLITE GERO VMF-ASTM
Page 4: ...10 2 Power Settings 38 11 0 Specifications 39 11 1 Environment 39 4 ...
Page 20: ...3 0 2132 Controller 3 7 Navigation Diagram 20 ...
Page 28: ...6 0 Maintenance Power Consumption Measure the current drawn on each phase cir cuit 28 ...
Page 40: ......
Page 41: ...Notes Service Record Engineer Name Date Record of Work ...