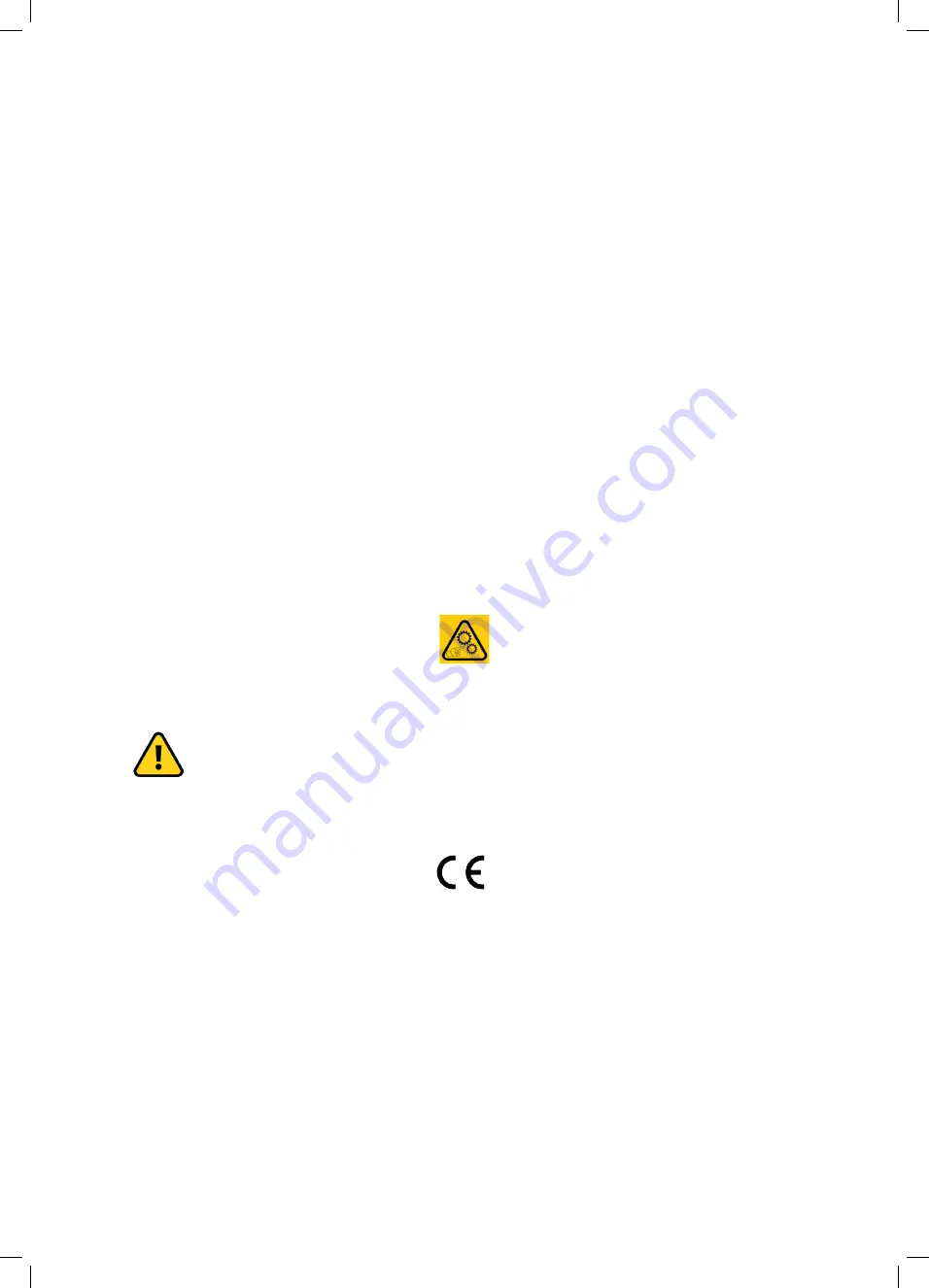
6
Operation and maintenance, Discfilter HSF2600 - 2,3 series with PFLC
2. SAFETY INSTRUCTIONS
Hydrotech Discfilters in the HSF2600 series are designed for safe operation provided that they are
installed correctly and used in accordance with the enclosed instructions. The equipment must
be installed correctly and adapted in accordance with local regulations. The machine equipment
is intended for use by multiple operators. You must read the applicable chapters in this manual
prior to using the equipment or performing maintenance.
⊲
Pay attention to all warning symbols that appear in this manual. If this information is ignored
it may result in serious personal injury and/or damage to equipment.
⊲
Assume all electrical equipment to be live.
⊲
Assume all hoses and pipes to be pressurized.
⊲
Before carrying out maintenance work, the main power switch (see Figure 2.3) must be turned
to the OFF (0) position and locked with a padlock.
⊲
Maintenance and service may only be performed by authorised personnel.
⊲
Adequate lighting should be used while operating the filter and when working in close prox-
imity to the filter.
2.1 Warning symbols
Warning symbols are used in this manual to draw attention to potentially dangerous situations:
Information that warns you of a potential risk of personal injury and/or damage to equip-
ment.
Warning stickers (see Figure 2.1) are attached to the filter to warn personnel and act as a remin-
der to keep hands and fingers away from the filter’s moving parts.
2.2 CE marking
This equipment is CE marked (see Figure 2.2), which guarantees that the equipment is designed,
manufactured and described in accordance with the requirements set out in the EU Machinery
directive.
2.3 Conversion
The CE marking does not include any components that are not approved by Hydrotech AB and
which are used in conversion/reconstruction of the equipment.
The warning symbols and CE marking must be attached where they are fully visible. If any part of
Figure 2.1
Figure 2.2