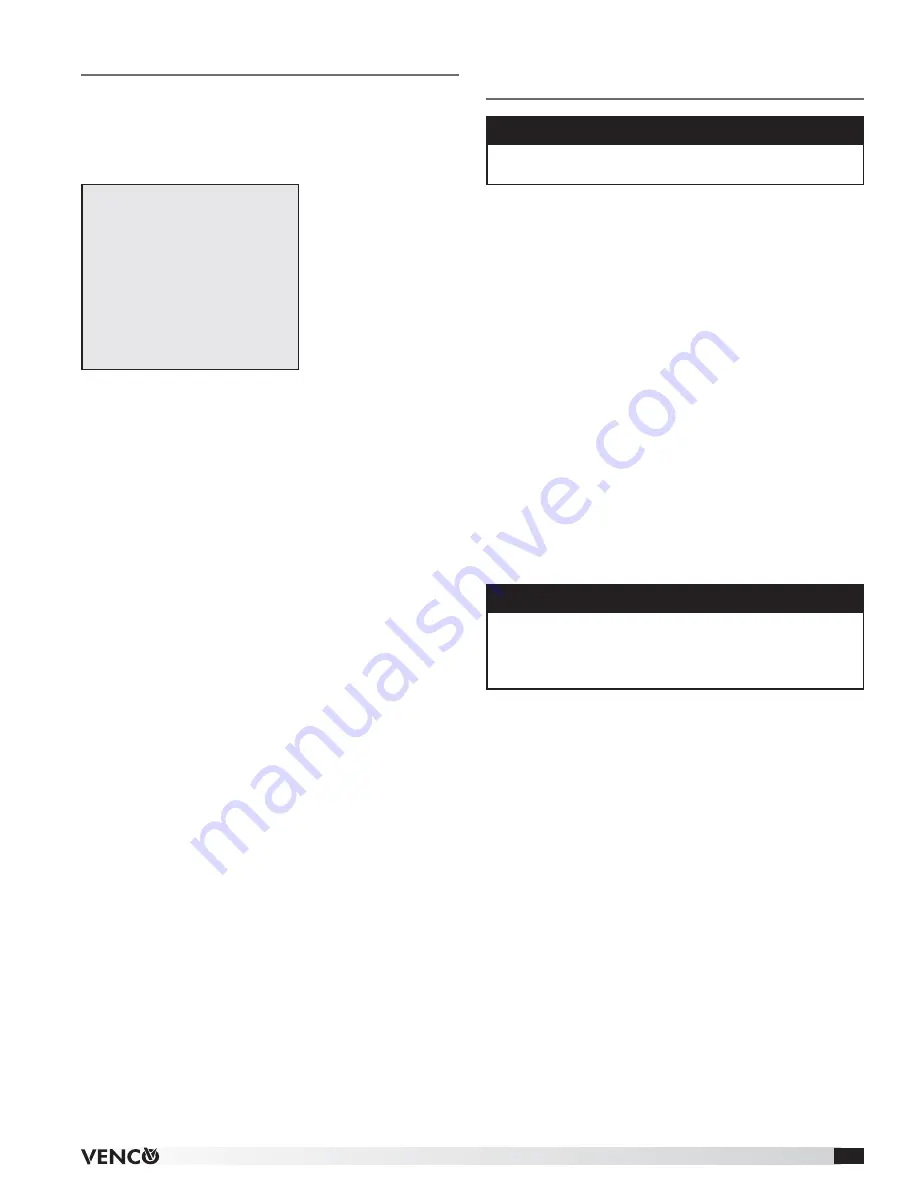
Fume Exhaust Fans
13
Vibration
On start-up and during operation, the unit should
operate smoothly with minimal vibration. It is possible
that a higher degree of vibration may be experienced.
Excessive vibration if left unchecked, can cause a
multitude of problems, including structural and/or
component failure.
The most common
sources of vibration
are listed.
Many of these
conditions can be
discovered by careful
observation. Refer to
the troubleshooting
section of this
manual for corrective
actions. If observation cannot locate the source of
vibration, a qualified technician using vibration analysis
equipment should be consulted. If the problem is wheel
unbalance, in-place balancing can be done through the
access panel located on the side of each fan’s tubular
housing. Any correction weights added to the wheel
should be welded to either the wheel back (single-plane
balance) or to the wheel back and wheel cone (two-
plane balance).
Common Sources of Vibration
1. Wheel Unbalance
2. Drive Pulley Misalignment
3. Incorrect Belt Tension
4. Bearing Misalignment
5. Mechanical Looseness
6. Faulty Belts
7. Drive Component Unbalance
8. Poor Inlet/Outlet Conditions
9. Foundation Stiffness
Routine Maintenance and
Operation
Once the unit has been put into operation, a routine
maintenance schedule should be set up to accomplish
the following:
1. Lubrication of bearings and motor.
2. Wheel, housing, bolts and set screws on the entire
fan should be checked for tightness.
3. Any dirt accumulation on the wheel or in the housing
should be removed to prevent unbalance and
possible damage.
4. Inspect fan impeller and housing looking for fatigue,
corrosion, or wear.
Fan Operation
All fans should be run every thirty (30) days, or at least
“bumped” every thirty days. It is preferred that each
fan is run as this causes all electrical and mechanical
components to get up to temperature, displacing any
formed condensation, redistributes load on bearings,
and redistributes grease in the bearings (motor and
shaft bearings).
CAUTION
When operating conditions of the fan are to be
changed (speed, pressure, temperature, etc.), consult
manufacturer to determine if the unit can operate
safely at the new condition.
CAUTION
When performing any service to the fan, disconnect
the electrical supply and secure fan impeller.
Motors
Motor maintenance is generally limited to cleaning
and lubrication. Cleaning should be limited to exterior
surfaces only. Removing dust and grease buildup on
the motor housing assists proper motor cooling. Never
wash-down motor with high pressure spray.
Greasing of motors is only intended when fittings are
provided. Many fractional motors are permanently
lubricated for life and require no further lubrication.
Motors supplied with grease fittings should be
greased in accordance with the manufacturer’s
recommendations. When motor temperature does not
exceed 104ºF
(40ºC)
, the grease should be replaced
after 2000 hours of running time.
Direct drive systems have extended grease lines to
lubricate the motor without removal of any guarding.