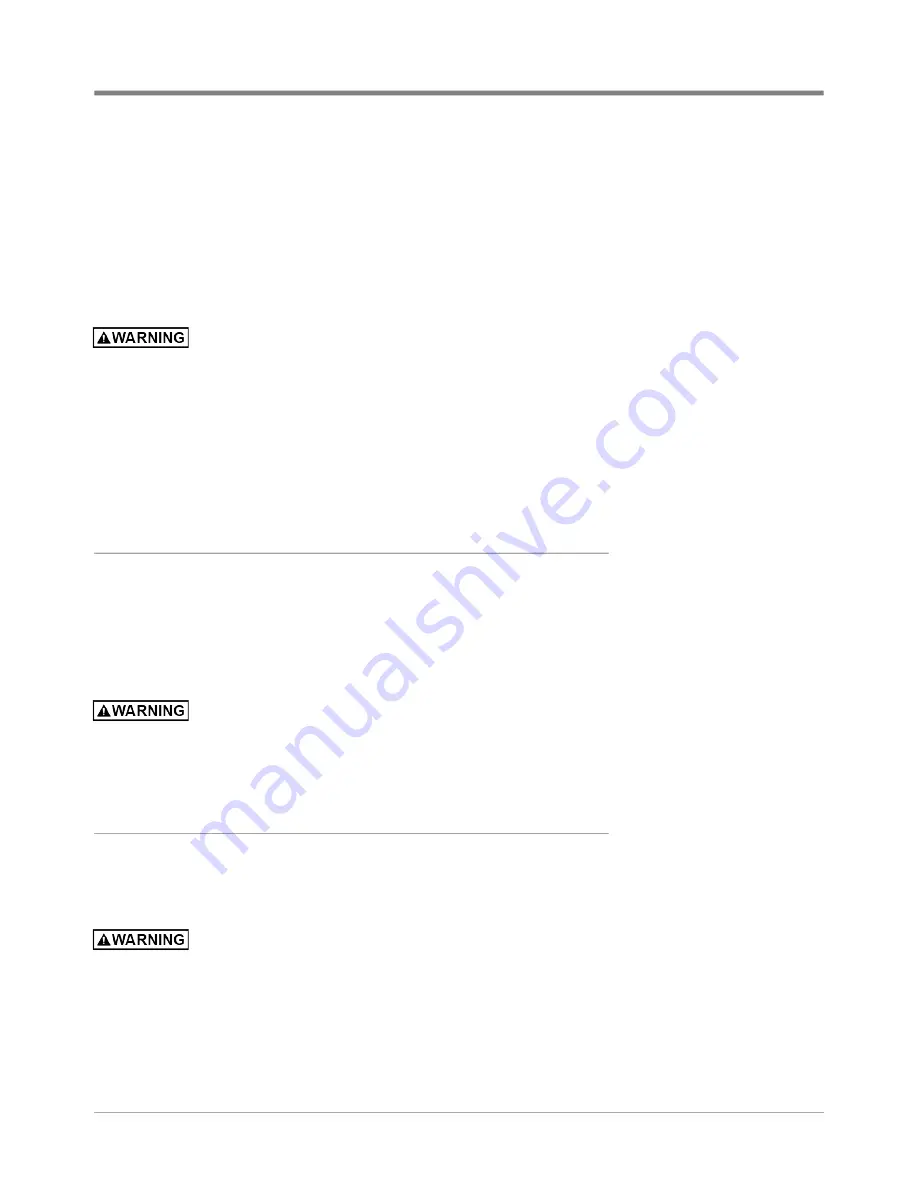
Installation
Follow These Directions Carefully
7
3. Maxxum® submersibles are not designed to handle abrasives or foreign particles in the product being
pumped.
4. Product temperature must never exceed 105°F (41°C) as the submersible motors are equipped with an
auxiliary thermal overload. Product temperature higher than 105°F (41°C) may result in tripping of the thermal
overload under low flow rate conditions.
5. Pumping water will overload the motor and damage the motor bearings.
6. These units are designed for use in Class I, Group D atmospheres.
7. Install pumping system in accordance to applicable codes.
Proper motor overload protection must be provided by an external control device. To
maintain overload protection and warranty, the magnetic starters used must be sup
-
plied by Red Jacket, or have equivalent protection features defined as follows:
- 3-leg protection
- Properly sized quick trip heaters, and
- Ambient temperature compensated overloads.
8. The UMP (Unitized-Motor-Pump) contains no serviceable parts (other than the foot valve) and should not be
modified or adjusted.
Follow These Directions Carefully
Check these points before installing.
1. The power supply against the equipment voltage rating. For 3 phase units, request the power company identify
and tag the service wires for L-1, L-2, L-3 phase sequence.
2. Be certain that the pump with the siphon valve is installed into the correct tank.
3. Check the equipment which was received against Table 2 and Figure 6 for the tank diameter and bury depth.
Before installing pipe threads apply an adequate amount of fresh, UL classified for
petroleum, non-setting thread sealant.
4. Apply thread sealant to the six-inch riser/flange male threads. Thread it into the tank port. Tighten the riser/
flange until the joint is water tight.
Installing The Pumping Unit
1. Apply a gasket compound to the bottom surface of the manifold and press the gasket onto the manifold’s
mating surface so the holes in the gasket and manifold align (reference Figure 1).
2. Coat the exposed surface of the gasket with gasket compound.
Confirm that the lifting eyebolts are properly torqued to 10 ft-lbs (13.6 N•m) with a
minimum of 6 full threads installed.
Occasionally, eyebolts are removed after pump
installation and corrosion may occur in the threaded areas of the extractable and the
eyebolt. If corrosion has occurred, the extractable and eyebolt should be replaced.
Utilize BOTH lifting eyebolts to suspend the pump vertically and lower the pumping
unit into position. Do not allow the gasket to contact the riser flange until the bolt
holes in the flange are aligned with those in the manifold and the discharge port is
aimed in the desired direction.