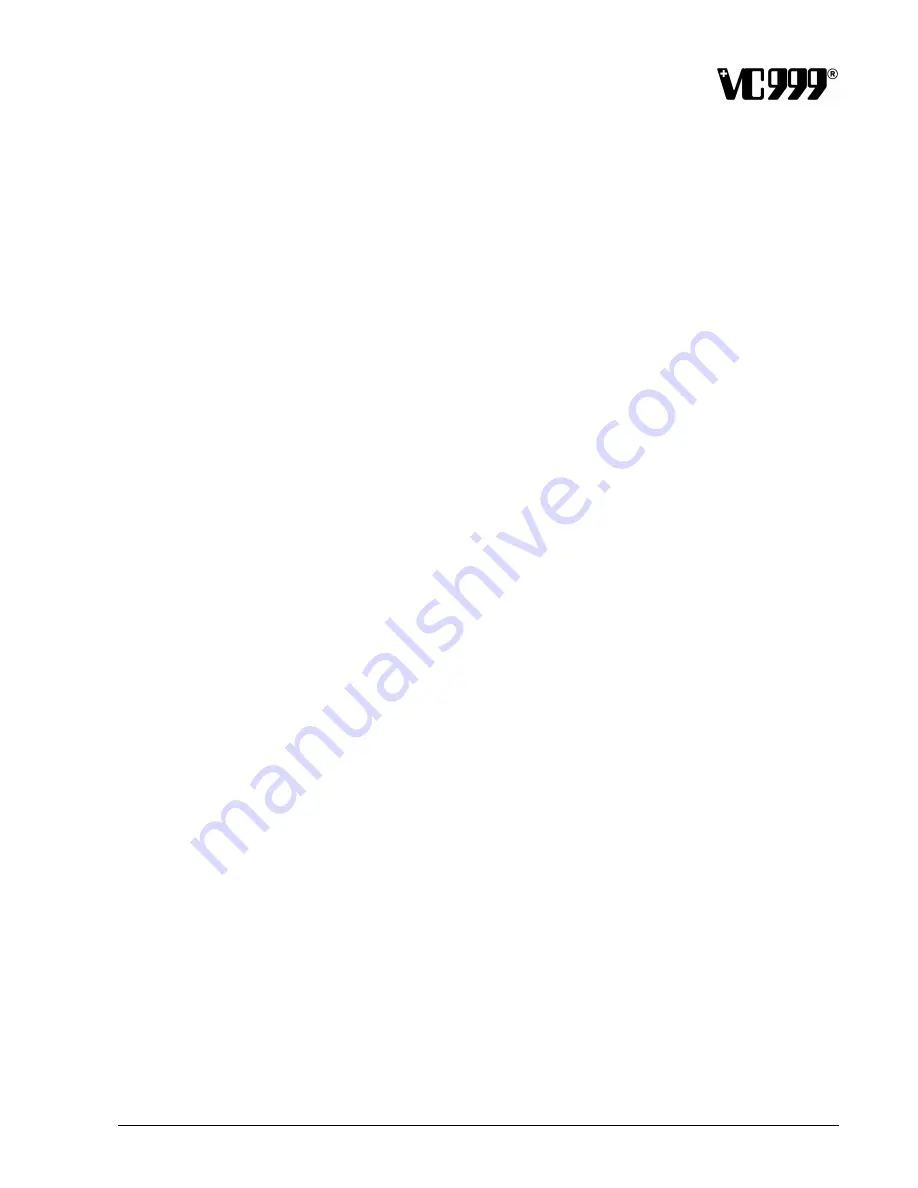
K5/K5N Vacuum Packaging Machine
Contents
2002-04-25
Art. no. 519.339 DE
Page 2 /1
Contents
1
Introduction .......................................................................................................... 5
1.1
General information ............................................................................................. 5
1.2
Definitions ............................................................................................................... 6
1.3
Protection of copyright........................................................................................ 6
2
Safety, warranty.................................................................................................. 7
2.1
General safety instructions ............................................................................... 7
2.1.1
Use as prescribed ................................................................................................ 8
2.1.1.1
Machine without an inert gas system (K5 type)......................................... 8
2.1.1.2
Machine with an inert gas system (K5N type) ........................................... 8
2.1.2
Processing materials ........................................................................................... 9
2.1.2.1
Vacuum bags ......................................................................................................... 9
2.1.2.2
Suitable products .................................................................................................. 9
2.1.2.3
Inert gas................................................................................................................... 9
2.1.3
Requirements for operators ............................................................................ 10
2.2
Explanation of the safety instructions.......................................................... 10
2.3
Warranty, liability................................................................................................ 10
3
Description of the machine ......................................................................... 11
3.1
Principle of how it works .................................................................................. 11
3.1.1
Structure of the machine .................................................................................. 11
3.1.2
Packaging cycle ..................................................................................................11
3.2
Technical data ..................................................................................................... 12
3.2.1
Dimensions........................................................................................................... 12
3.2.2
Weight .................................................................................................................... 12
3.2.3
Vacuum technology........................................................................................... 13
3.2.3.1
Vacuum pump ..................................................................................................... 13
3.2.3.2
Vacuum generation ........................................................................................... 13
3.2.4
Welding technology........................................................................................... 13
3.2.5
Inert gas connection.......................................................................................... 13
3.2.6
Power supply ....................................................................................................... 13
3.2.7
Controller............................................................................................................... 14
3.2.8
Noise emission ....................................................................................................14
4
Packaging and transport .............................................................................. 15
4.1
Packaging the machine.................................................................................... 15
4.2
Transportation of the machine ....................................................................... 15
4.3
Unpacking the machine .................................................................................... 15
5
Setting up the machine ................................................................................. 16
5.1
Criteria for the installation site ....................................................................... 16
5.2
Foundations.......................................................................................................... 16
5.3
Ambient temperature ........................................................................................ 16
5.4
Safe ty space ........................................................................................................ 16