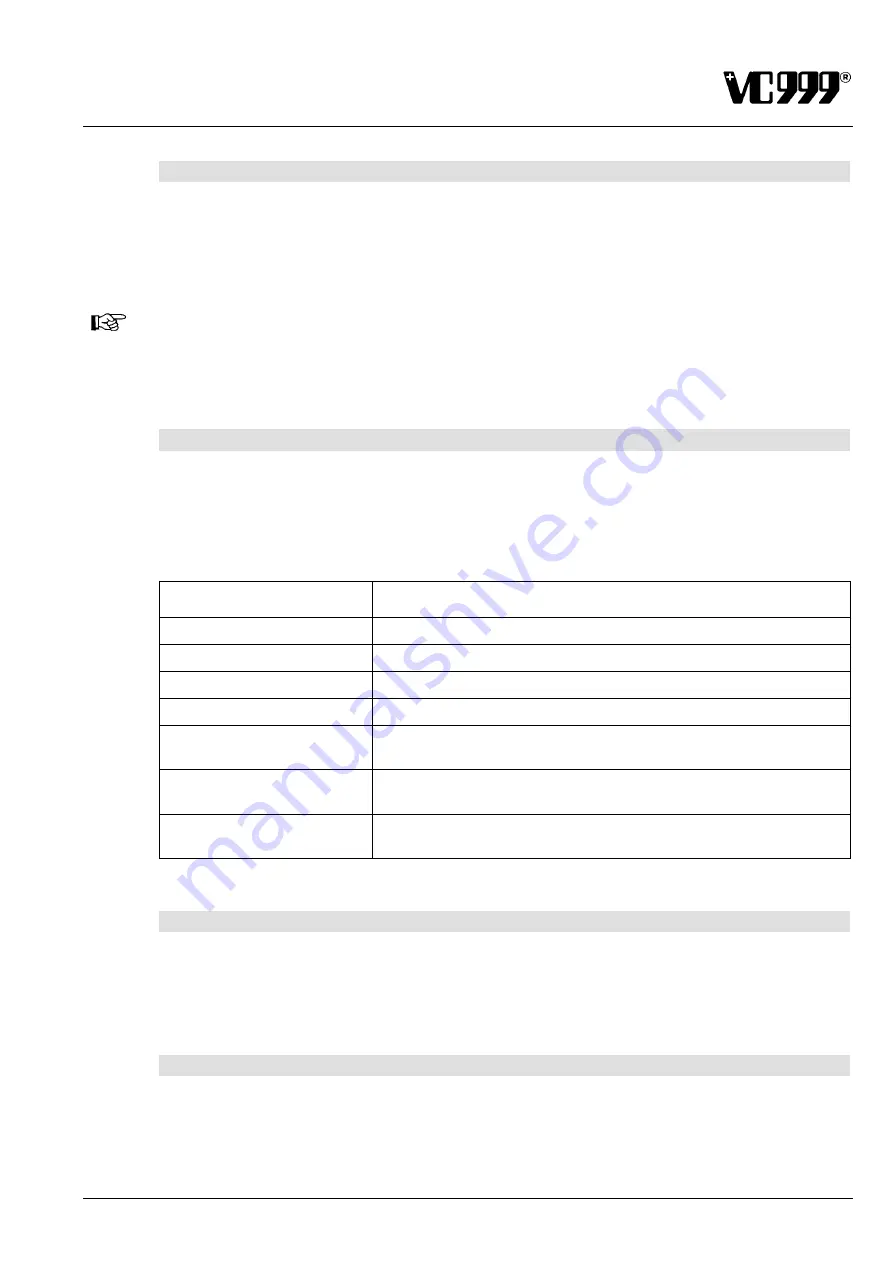
Vacuum Packaging Machines 07P ...
Operation
10.6.6 Sealing and cutting
The programmed sealing and cutting times refer to the operating heat of the sealing bars. In order to
obtain an optimum sealing quality independently of the operating temperature, a sensor measures the
heating bar temperature. The sealing and cutting times are automatically corrected.
A cutting time is only set when no counterseal has been pre-set. The cutting time can be different from
the sealing time.
IMPORTANT
With the HELP button it is possible to select a particular product from different types of bags
with already assigned sealing times.
10.6.7 Sealing type
The machine possesses sealing bars in the vacuum chamber lid and for counterseal (07P+G) also in
the vacuum chamber lower part left, right and at the front. The type of seal will determine which sealing
bars are in use and which are not.
With countersealing the, sealing is always carried out from the top and the bottom (biactive).
Setting
Active sealing bar
OFF
No sealing bar is active, Sealing is switched off
ALL 3 SEALING BARS
All 3 sealing bars in the vacuum chamber lid
SIDE BARS ONLY
Both side sealing bars in the vacuum chamber lid
FRONT BAR ONLY
Only the front sealing bar in the vacuum chamber lid
COUNTERSEAL ALL BARS
(07P+3G)
All 6 sealing bars in the vacuum chamber lid and in the vacuum
chamber lower part
COUNTERSEAL SIDEBARS
(07P+2G)
Each both side sealing bars in the vacuum chamber lid and the
vacuum chamber lower part
COUNTERSEAL FRONTBAR
(07P+G)
Only the front sealing bar in the vacuum chamber lid and the vacuum
chamber lower part
10.6.8 Product
height
In order to obtain an optimum sealing seam, it is important that the setting of the platform is adapted to
the product height. By entering the corresponding product height, the platform automatically travels after
the program selection to the correct height and thus ensures an optimum seal.
10.6.9 Preventilation
Preventilation has the effect of a fold-free clinging of the bag against the product and is suitable for
products which can be damaged by the sudden ventilation and/or which could damage the bag.
2003-11-05
Art. no. 527.763
Page 33/74
Summary of Contents for 07P Series
Page 2: ......
Page 4: ......
Page 69: ...Vacuum Packaging Machines 07P Circuit diagrams 2003 11 05 Art no 527 763 Page 69 74...
Page 70: ...Vacuum Packaging Machines 07P Circuit diagrams Page 70 74 Art no 527 763 2003 11 05...
Page 71: ...Vacuum Packaging Machines 07P Circuit diagrams 2003 11 05 Art no 527 763 Page 71 74...