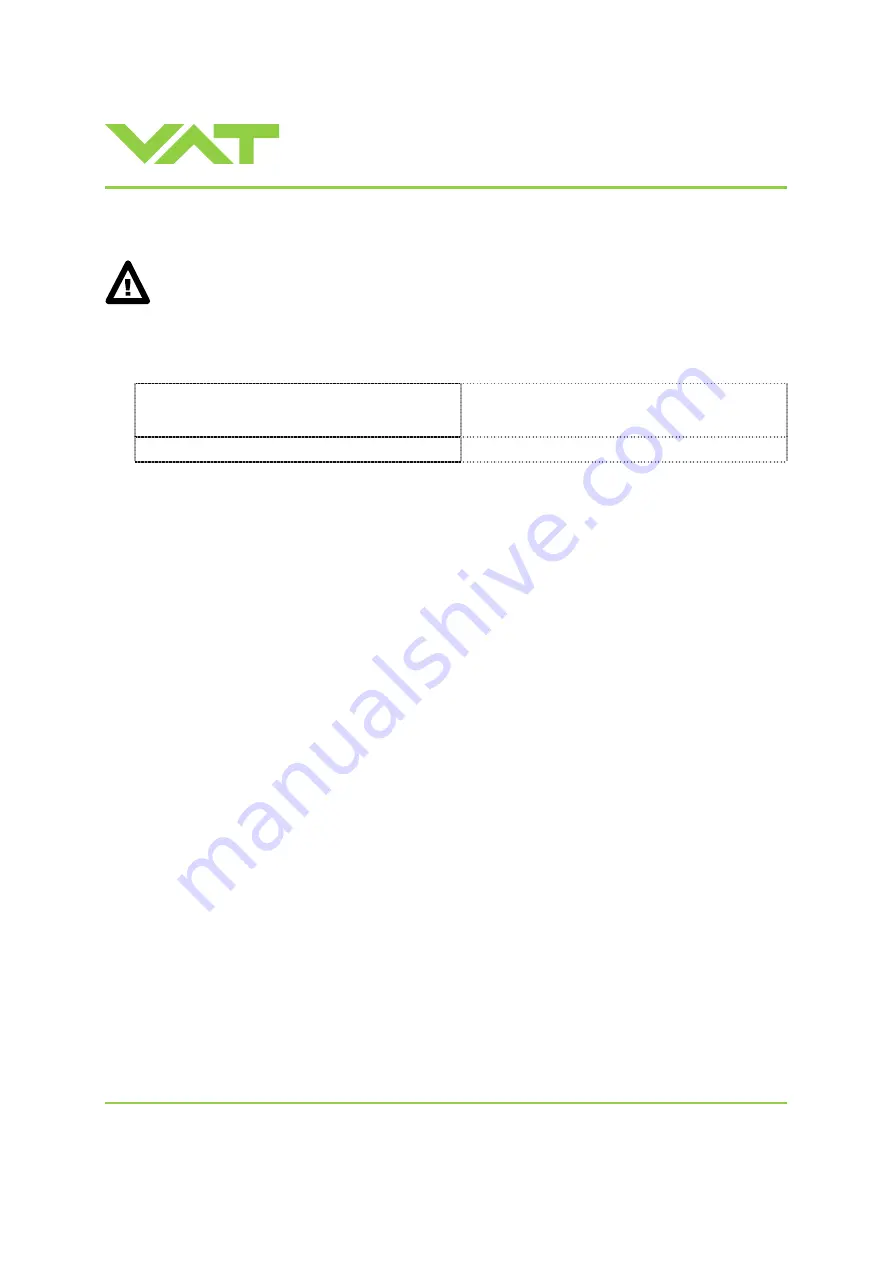
Installation, Operating & Maintenance Instructions
Series 650 DN 100-250 (I.D. 4“ - 10”), RS485
VAT Vakuumventile AG, CH-9469 Haag, Switzerland
Tel ++41 81 771 61 61 Fax ++41 81 771 48 30 Email
www.vatvalve.com
271149EA
2007-06-12
34/77
3.10 Pressure control
To prepare valve for PRESSURE CONTROL perform complete «Setup procedure».
The valve has parameters that may be modified to tune pressure control performance.
Refer to «Tuning of control performance».
The included PID controller controls the chamber pressure according to the pressure setpoint by means of the valve
position. The PID controller works with an adaptive algorithm to achieve best results under altering conditions (gasflow,
gas type).
Local operation
:
(‘Control View’, ‘Control Performance Analyzer’ or
‘Service Box 2‘)
Remote operation
:
(Refer to chapter «RS485 control commands» for
details)
Select or enter pressure setpoint
Send PRESSURE CONTROL
3.10.1 Operation with 2 sensors
[applicable for 650 . . - . . . K - . . . . version only]
If 2 sensor operation is enabled, changeover between the sensors is done automatically during pressure control. For
configuration refer to chapter «Setup procedure». We recommend a ratio of 10:1 between the pressure gauges. Max. ratio
is 100:1. It is required that the high range pressure gauge is connected to sensor 1 input and the low range pressure
gauge to the sensor 2 input.
Between 90 and 100% of the low range sensor full scale, the low range sensor is phased out while high range sensor is
phased in. This maintains a functional response behavior in case of small calibration errors between the two sensors. The
pressure output in this range is a blend between both sensors.
For monitoring purpose each sensor signal may be read out individually.
Note: Make sure that both sensors are calibrated.
Note: Do not close optional gauge isolation valves during the transition phase between the sensors.