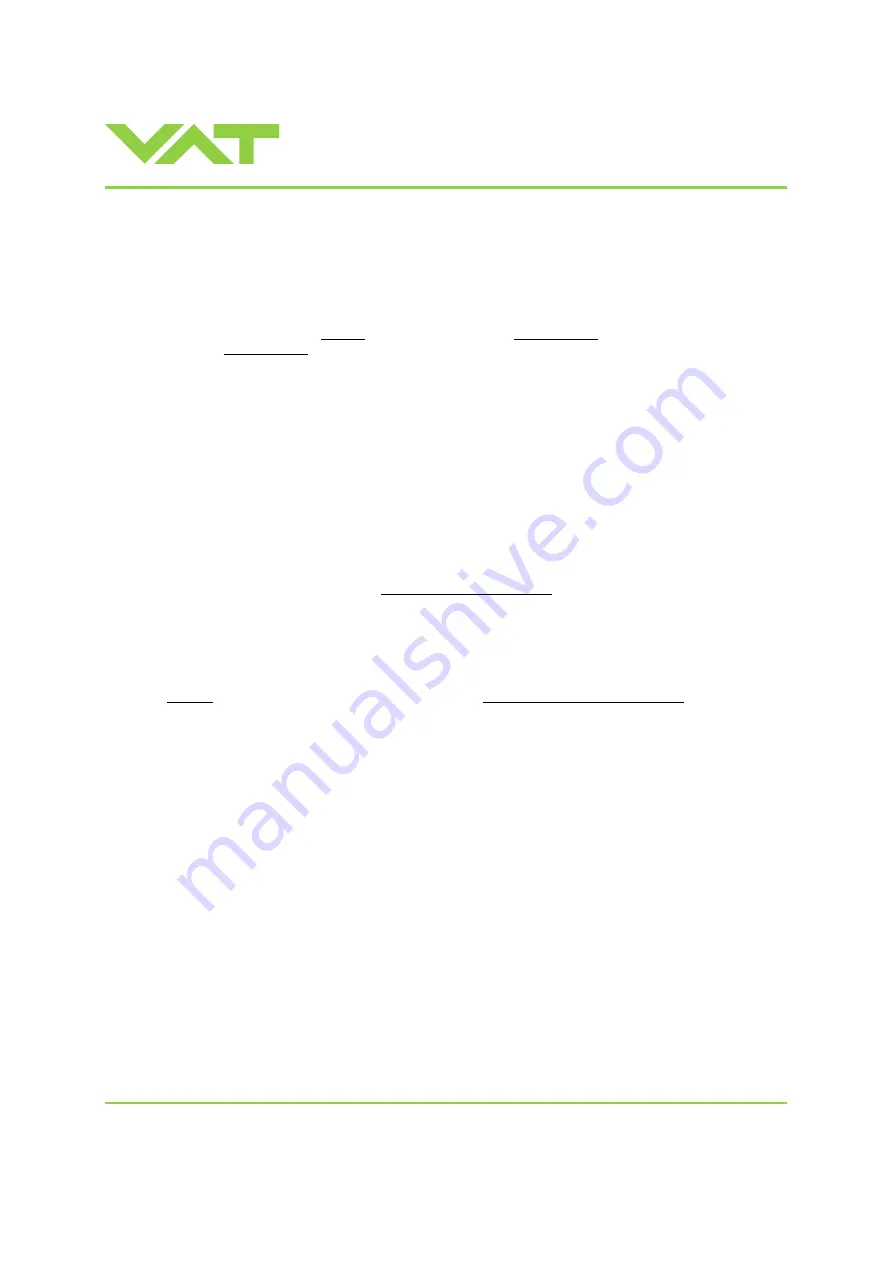
Installation, Operating & Maintenance Instructions
Series 615 DN 63-100 (I.D. 2.5“ - 4”), RS232
VAT Vakuumventile AG, CH-9469 Haag, Switzerland
Tel +41 81 771 61 61 Fax +41 81 771 48 30 [email protected] www.vatvalve.com
290227EA
2011-06-24
10/79
1. Install valve [1] into the vacuum system. Valve seat side must face process chamber. The valve seat side is indicated
by the symbol "
∇
" on the valve flange.
Caution: Do not tighten the flange screws stronger than indicated under «Tightening torque».
Caution: Do not admit higher forces to the valve than indicated under «Admissible forces».
Note: Make sure that enough space is kept free to do preventive maintenance work. The required space is indicated
on the dimensional drawing.
Note: Control unit of valves with ISO-KF flanges (615 . . – K . . . ) needs support when mounted on horizontal piping
and control unit does not hang.
2. Install the ground connection cable at controller. Refer to «Electrical connection»
3. Install sensor(s) [2] according to the recommendations of the sensor manufacturer and directives given under
«Requirements to sensor connection».
4. Connect pressure sensor cable [3] to sensor(s) and then to valve (connector: SENSOR). Refer to chapter «Electrical
connection» for correct wiring.
Note: Input for second sensor is available on 615 . . - . . . H - . . . ., 615 . . - . . . W - . . . . and 615 . . - . . . Z - . . . .
versions only.
5. Connect valve to remote control unit [4] (connector: INTERFACE). Refer to «RS232 connection» for correct wiring.
6. Connect power supply [5] to valve (connector: POWER). Refer to chapter «Electrical connection» for correct wiring.
Note: To provide power to the valve motor pins 4 and 8 must be bridged, otherwise motor interlock is active and the
valve enters the safety mode and is not operative. Refer also to «Safety mode».
7. This valve may optionally be equipped with a heating device. Connect VAT heating device according to manual of
respective heating device.
8. Perform «Setup procedure» to prepare valve for operation.
Note: Without performing the setup procedure the valve will not be able to do pressure control.
2.3 Tightening
torque
Tighten mounting screws of the flanges uniformly in crosswise order. Observe the maximum torque levels in the following
table. Higher tightening torques deforms the valve body and may lead to malfunction of the valve.
2.3.1 Mounting of CF-F flanges
Tightening torques for CF-F flange connections depend on the type of seal which is used. Follow recommendations of
seal manufacturer.