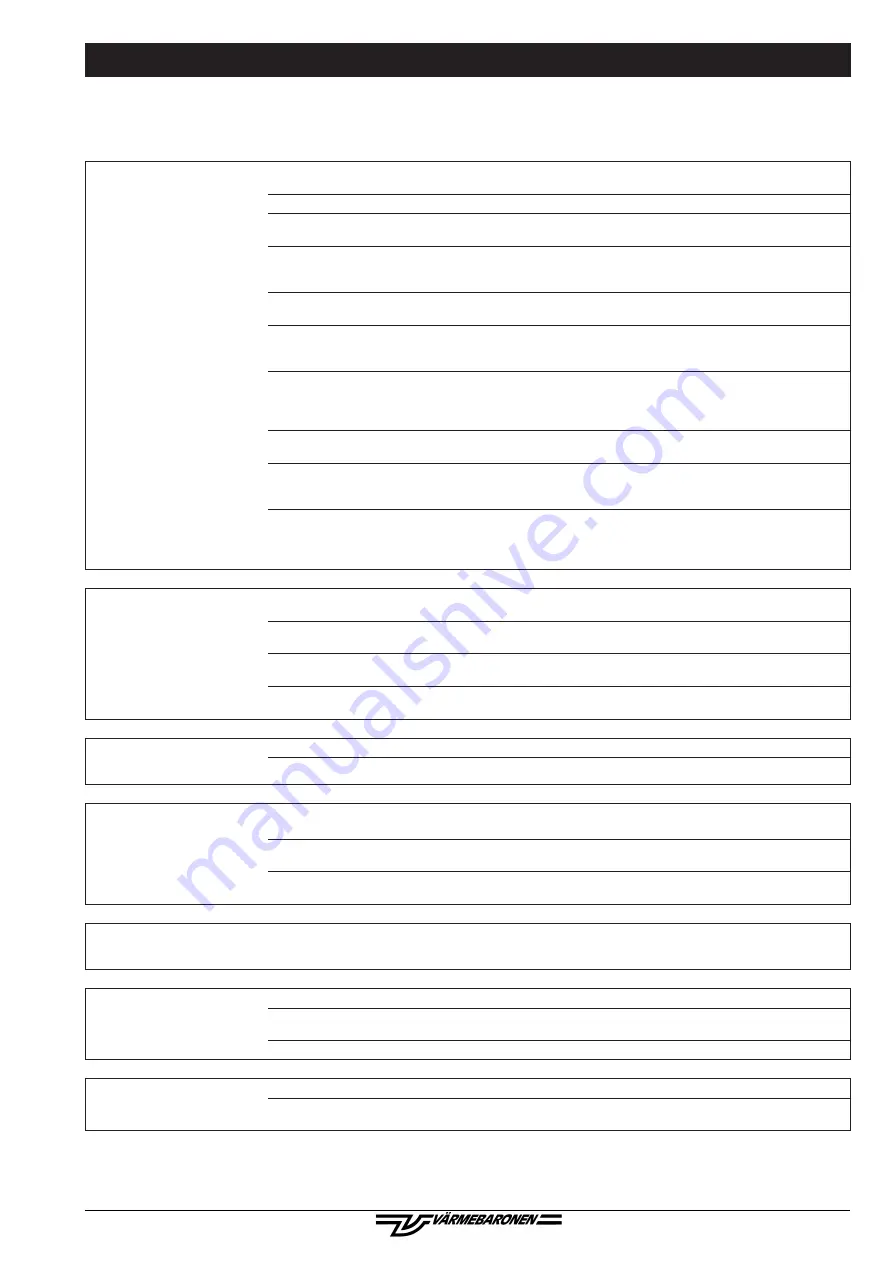
11
2008-03
Vedolux 37
Problems burning firewood
The most common problems that occur when burning firewood are usually the result of the boiler failing to reach a high enough temperature so
that the boiler never really gets going. Another common problem is that the heat is not transferred to the accumulator tanks even though the
wood is burning well in the boiler.
Poor combustion in the boiler Damp wood.
A ceramic boiler requires a high combustion temperature. To
achieve this, the wood must be dry, moisture content 12- 30%.
Incorrect handling.
Read the instructions.
The wood is not suitable for the
boiler.
The firewood should be 50 cm long. The thickness should allow
three blocks to fit the width of the grate.
Shaped wood, rectangular wood. If uniform blocks of wood are stacked on each other, a sold mass
of wood is created with limited surface area for the fire to act on.
Arrange the wood so there are gaps between the blocks.
Fails to burn.
This happens when the wood is bent and is not suitable for the
boiler. Use wood that is suitable for the boiler.
Inadequate air supply.
The fresh air intake of the boiler room must have at least the same
cross sectional area as the flue duct. Check that the air valve is
open.
Secondary/tertiary damper too
open.
If the damper is too open, the primary and secondary air will be
incorrectly distributed. Start with the secondary damper fully
closed. It will never normally be necessary to open it by more than
a few millimetres (glass).
The chimney runs downwards
from the boiler connection.
The turbulence created takes away some of the draught. Fill the
lower part with sand or similar material.
No accumulator control.
A ceramic boiler is at its most efficient when the ceramic is hot.
The temperature in the boiler therefore needs to be increased
quickly before charging begins. Add a control system.
Ceramic not correctly positioned. If the boiler is new, check that the ceramic has not moved during
transport. There is no need to remove the ceramic, even for clean-
ing. However, if it is removed anyway, make sure it is replaced cor-
rectly. Check the seal with the combustion chamber walls.
High flue gas temperature.
Tar, soot in the pipes.
Due to incorrect combustion. Check the firewood, the draught,
the air intake and the handling. Clean the boiler.
Bypass damper open.
Close the damper. The bypass damper must only be opened for
adding wood.
Combustion tunnel in wrong posi-
tion.
The combustion tunnel must be inserted as illustrated on page 9.
Faulty flue gas thermometer.
The thermometer may have been damaged by cleaning or by
long periods of updraught burning.
Tar and large quantities of soot
in the pipes.
Incorrect combustion.
See the section about high flue gas temperature.
Wrong connections.
Check.
Heat is not transferred from the
boiler to the accumulator.
Circulation pump too small.
The pump must have sufficient capacity to transfer the heat.
Change to a larger pump.
Air.
If you make the connections as suggested, the system will not be
sensitive to air problems. Vent.
Wrong connection of accumula
-
tor.
See the points above.
Boiling noises in the boiler.
Low pressure head.
Check the pressure, which should be about 1 bar. The expansion
vessel must be dimensioned for the volume and for the tempera-
ture variations that occur.
Fan fails to start
Main switch in position O.
Set the main switches to position I.
Forgotten to connect the instant
connector.
Connect the instant connector.
Overheating protection triggered. Reset the overheating protection.
The safety valve opens when
the system heats up.
Expansion vessel too small.
See the section about the “Expansion system” on page 5.
Initial pressure in the expansion
vessel too high/low.
Check the pressure in the vessel, see the section about the “Ex-
pansion system” on page 5.