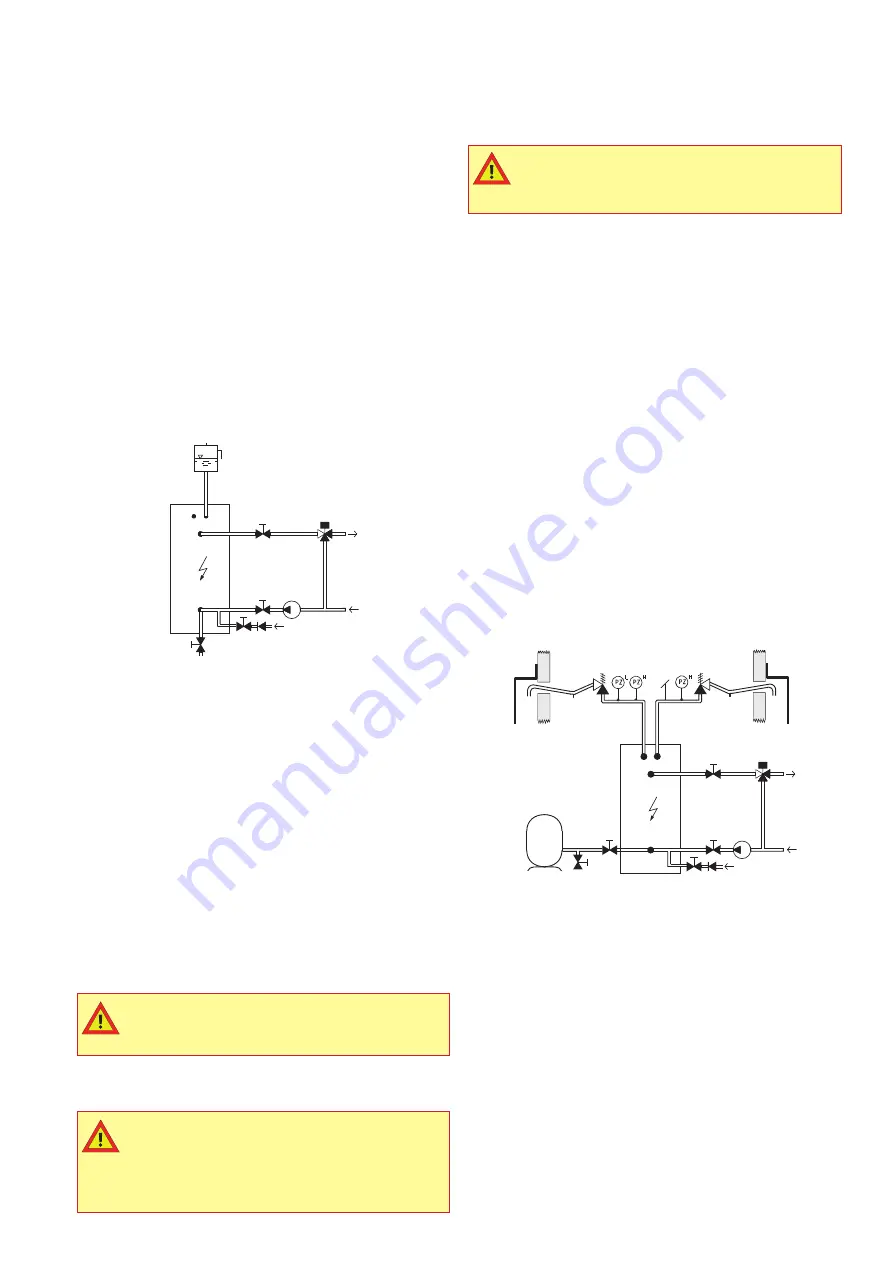
ins
ta
lla
tio
n
23
Värmebaronen EP- 900, -1080, -1200, -1400
Pipe installation
Excessive water flow can result in the following:
- Vibrations in the immersion heaters with noise and reduced
service life as a result.
- Unnecessary wear on the system's components.
System principles
The figures shown are system principles. The actual system
must be installed according to existing standards.
Any additional equipment must be installed according to the
manufacturer's instructions.
Open system
The boiler's safety line must be connected in an uninterrupt-
ed, un-closeable pitch to an expansion vessel, installed at the
highest point of the heating system.
Expansion vessels are dimensioned to accommodate chang-
es in water volume due to heating and cooling.
Expansion vessels, safety pipes, aeration and overflow
pipes must be installed such that they are protected against
freezing.
To avoid oxygenation of the water, the distance between
the heating system’s highest point and the expansion vessel
must not be less than 2.5 metres.
Pressure height must exceed the pump's lowest static pres-
sure on the low side.
To avoid damage in the event of any blockage in
the expansion system, the boiler should be fitted
with a safety valve.
The air vent on the boiler's safety pipe must
always be open. Otherwise, air collects in the
top of the boiler, which leads to disruption as the
float switch is triggered on account of insufficient
water level.
Closed system without a expansion trap, >300 kW, ≤105ºC
The opening pressure of the safety valve is
determined by the component in the system that
tolerates the lowest pressure.
Under SS EN 12828, the installation must include:
- At least one safety valve min DN 15, with sufficient blow-off
capacity at the system's operating pressure.
- Two pressure guards, one with zero voltage release.
- Low pressure guard if there is a risk of boiling dry, alterna-
tive to level switch.
- Two temperature guards, STB.
- Flow guard if the boiler cannot cope with zero flow.
- Valve for expansion vessel, must be locked in open position.
- For boiler placed at a higher level than consumers, a level
guard is required
The boiler: - can cope with zero flow, from a safety viewpoint
- has two built-in temperature guards.
- has a built-in level sensor.
- can be supplied with factory installed safety
equipment.
Safety valves are fitted with pressure guards and an auto-
matic vent valve on the boiler's safety pipe.
The discharge pipe of the safety valve shall lead to a safe
place in accordance with the requirements of SS EN 12828.
Normally, this means on the outside of the building or in a
expansion trap.
The discharge pipe from the safety valve shall be dimen-
sioned so that the blow-off capacity is not impeded.
The discharge pipe must be laid so it cannot freeze, must be
cleaned well and must be laid so that water pockets cannot
form. DN 10 drainage must be provided if there is a risk of
standing water in the safety valve outlet line.