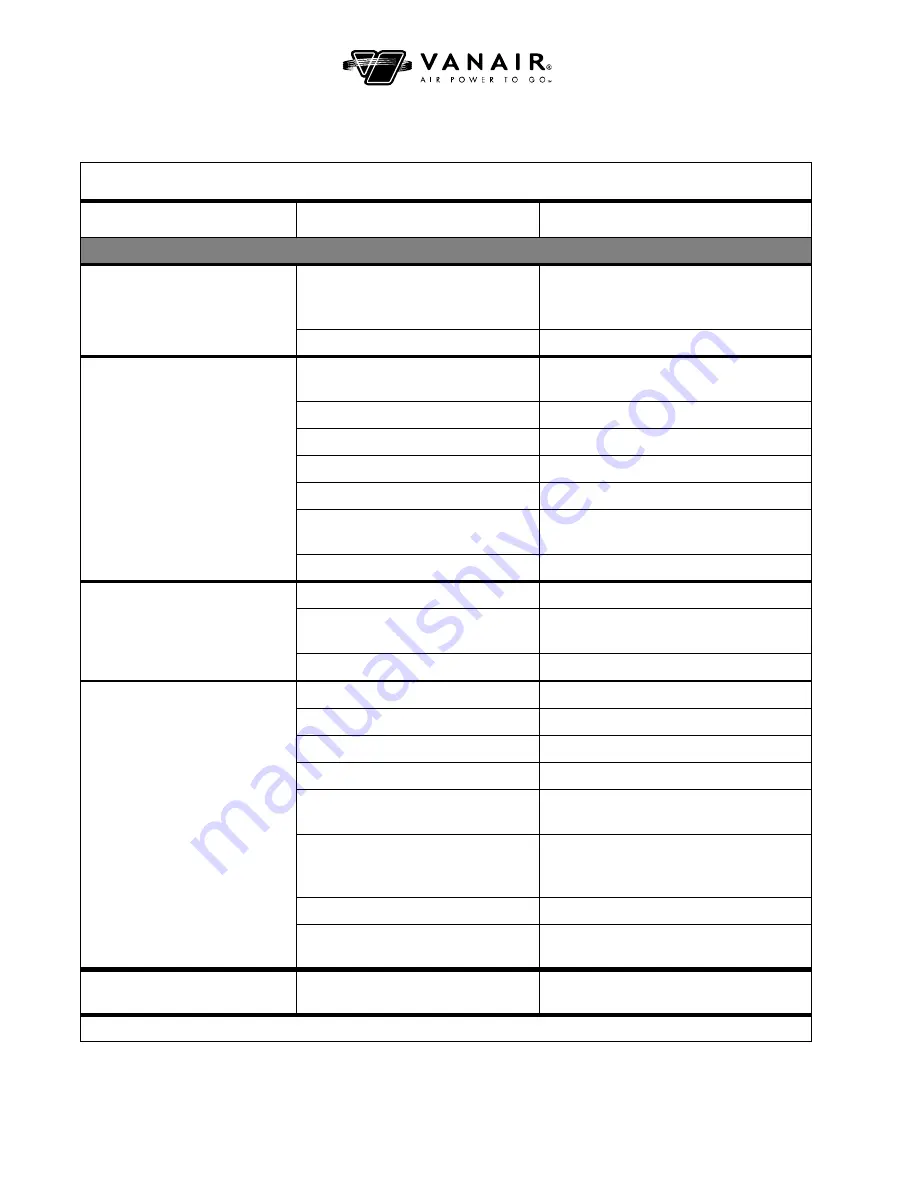
SECTION 6: TROUBLESHOOTING
AIR N ARC
®
150 SERIES
PAGE - 48
090051-OP_r0 (FEB-2014)
Vanair Manufacturing, Inc.
vanair.com • 800-526-8817
COMPRESSOR (CONTINUED)
Water in crankcase
Oil breaking up
Oil gets dirty; rusty valve or
cylinder (continued)
System pressure leaking back through
check valve when compressor is
stopped
Check and replace/check valve, if
necessary.
Wrong oil being used.
Drain and replace with proper oil.
Excessive vibration
Loose compressor, motor, engine or
guard
Tighten components.
Excessive discharge pressure
Reduce operating pressure.
Compressor not level
Level compressor.
Leg bolts tightened too tightly to floor
Loosen leg bolts.
Wrong oil being used
Drain and replace with proper oil.
Loose flywheel, drive pulley or drive
belts
Tighten loose components and check belts.
Worn rods, wrist pin or main bearings
Check and replace worn parts.
Compressor knocks
Compressor valves loose or broken
Check and replace worn or broken valves.
Inspect check valve; it may knock at
low pressures
Remove and clean check valve.
Bearing failure
Replace compressor.
Compressor uses too much oil
Clogged inlet filter
Clean inlet filter or replace, if necessary.
Wrong oil being used; wrong viscosity
Drain and replace oil.
Oil level too high
Fill compressor with oil to proper level.
Crankcase breather valve malfunction
Replace crankcase breather.
Compressor runs unloaded too long
Increase load or stop compressor when not
needed. Check for air leaks.
Compressor operating outside in cold
conditions or inlet filter not protected
against weather
Provide adequate protection against
extreme weather conditions.
Worn piston rings
Replace piston rings.
Piston rings not seated
See
Piston rings not seated
instructions,
below.
Piston rings not seated
Ample time not allowed for new rings to
seat
Allow 100 hours of normal operation for new
rings to seat.
Continued on next page
6.2 TROUBLESHOOTING GUIDE
Fault/Malfunction
Possible Cause
Corrective Action