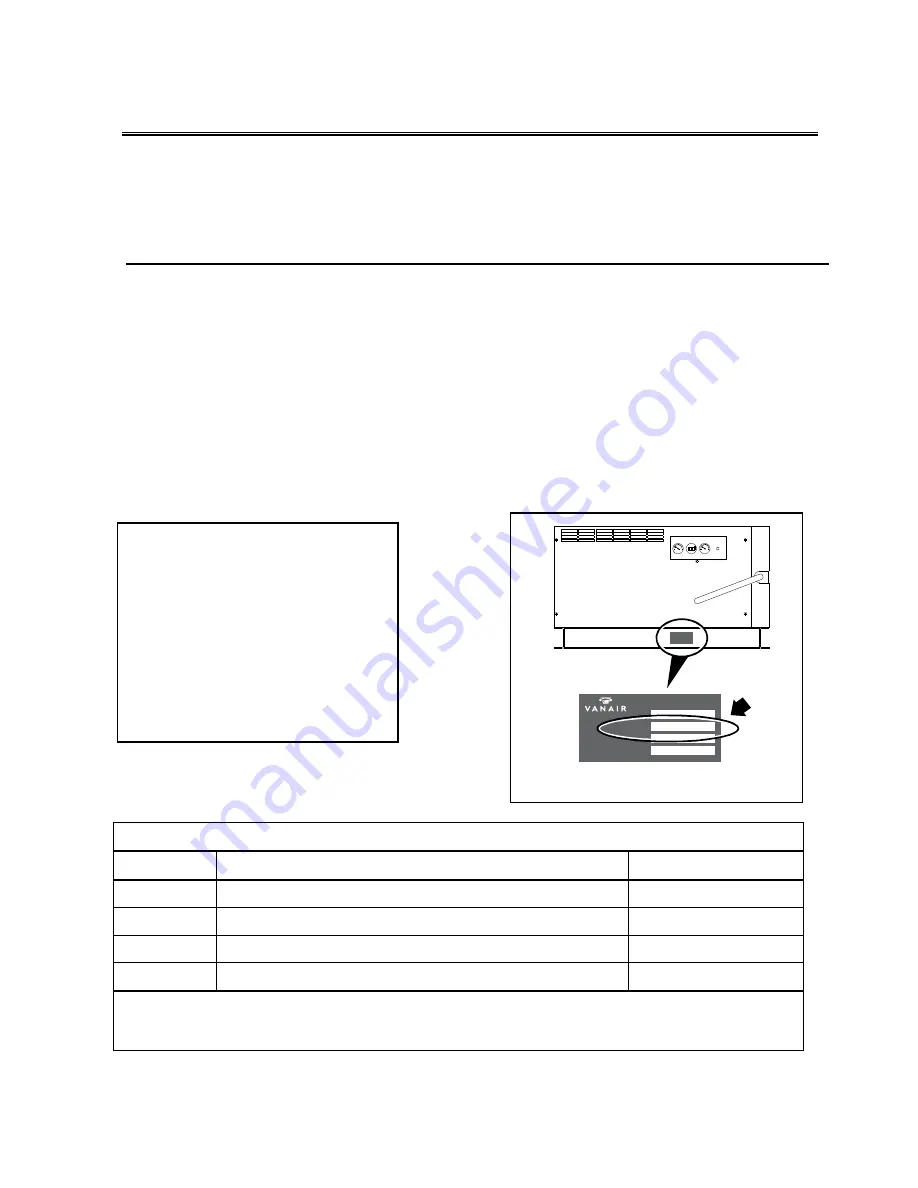
800-526-8817
260940
MODEL NUMBER
SERIAL NUMBER
MAXIMUM PRE SSURE
COMPRE SSOR INPUT RPM
ww w.vanai r.com
ILLUSTRATIONS AND PARTS LIST Section 8 - Pg 01
SECTION 8:
ILLUSTRATIONS AND PARTS LIST
8.1 Procedure for Ordering Parts
Parts should be ordered from the nearest Vanair Representative or the Representative
from whom the compressor was purchased. If, for any reason, parts cannot be obtained
in this manner, contact the factory directly at the address or phone numbers below.
When ordering parts always indicate the
Serial Number
of the compressor package.
This can be obtained from the Bill of Lading for the compressor or from the Serial
Number Plate located on the compressor (
Figure 8-1
).
Figure 8-1 Serial Plate Location
Table 8A: Recommended Spare Parts List
Key No.
Description
Part Order No.
1
Oil Filter Replacement Element
261991
2
Air Filter Replacement Element
264266
3
Air/Oil Separator Replacement Element
260017-001
4
Vanguard™ Premium Oil
I
264626-4PACK
I
Quantity of four (4) x one (1) gallon containers.
Use only Vanair
®
Vanguard™ Premium Synthetic Oil and
Genuine Vanair Parts. Inspect and replace damaged components before operation. Substituting non-
Vanguard™ Oil or non-genuine Vanair filter components WILL VOID THE COMPRESSOR WARRANTY!
VANAIR MANUFACTURING,
INC.
10896 West 300 North
Michigan City, IN 46360
Phone: (219) 879-5100
(800) 526-8817
Service Fax: (219) 879-5335
Parts Fax: (219) 879-5340
Sales Fax: (219) 879-5800
Summary of Contents for ADHD Powertech
Page 8: ...BLANK PAGE...
Page 16: ...BLANK PAGE...
Page 19: ...DESCRIPTION Section 2 Pg 03 Figure 2 1 Compressor Discharge and Cooling and Lubrication System...
Page 31: ...INSTALLATION Section 5 Pg 03 5 3 Wire Diagram 266551_r1_ TP...
Page 32: ...INSTALLATION Section 5 Pg 04 5 4 Dimensions Diagram 263620_r1_ TP...
Page 40: ...BLANK PAGE...
Page 46: ...PARTS LIST ILLUSTRATION Section 8 Pg 04 8 3 Enclosure 263612...
Page 50: ...PARTS LIST ILLUSTRATION Section 8 Pg 08 8 5 Inlet Valve Assembly 265400_r0...
Page 56: ...PARTS LIST ILLUSTRATION Section 8 Pg 14 8 8 Above Deck Hydraulic Drive 6100047ID_r0...
Page 60: ...BLANK PAGE...
Page 62: ...BLANK PAGE...
Page 63: ...BLANK PAGE...