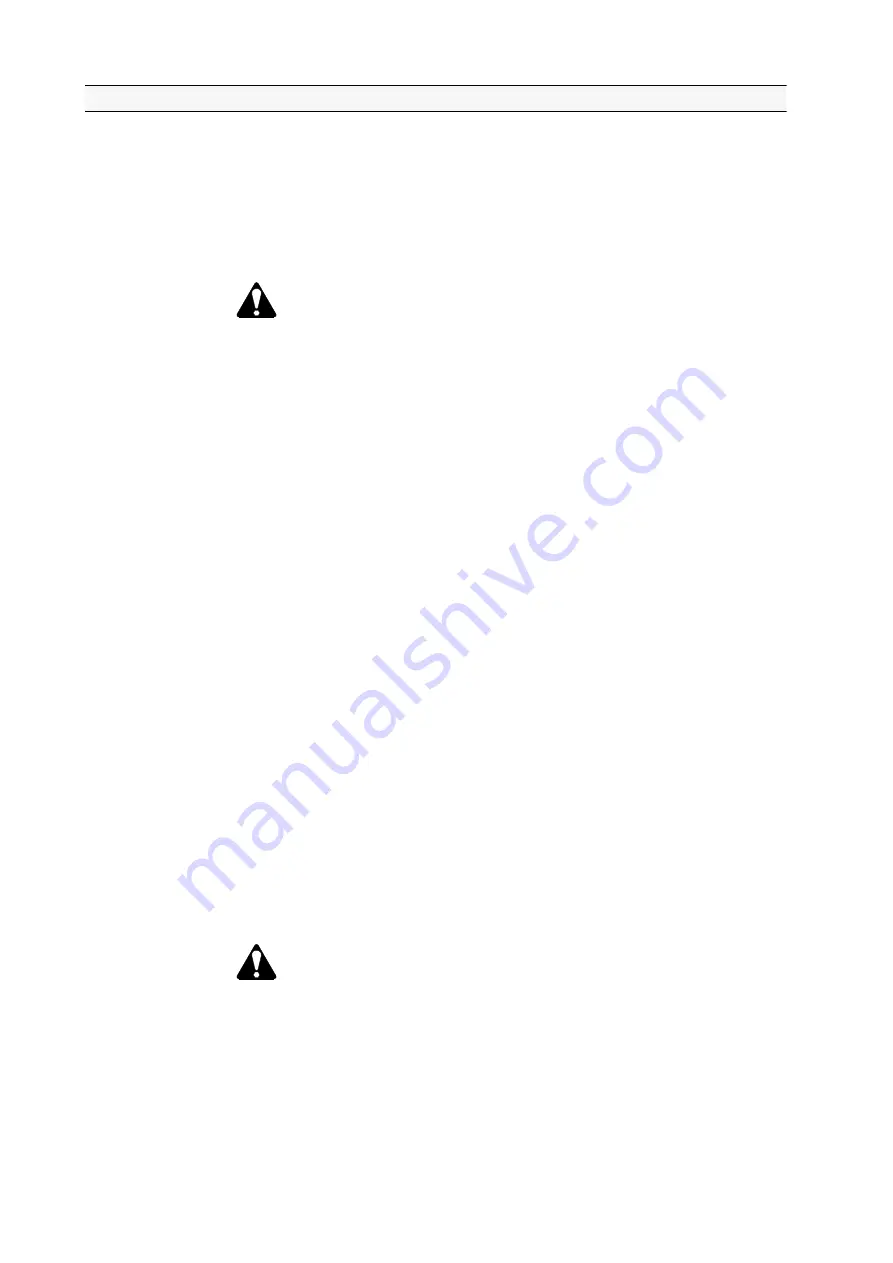
1.2.2
Maintaining hardware safety
To ensure maximum safety for the operator, maintain tractor hardware safety.
The owner is responsible for repairing any damage or wear which might
endanger the safety of the tractor.
•
Cab
Damages on the cab must be repaired without delay to ensure the cab's
protective capability.
WARNING: If damage occurs to the cab, replace all parts affected
with new ones. Do not attempt any repair work (welding, drilling,
cutting, or grinding) without first consulting the manufacturer.
•
Tractor construction
Do not change the tractor construction, such as maximum driving speed or
maximum power.
The tractor is type approved to comply with construction and use regulations.
Any changes to the tractor construction may reduce safety and durability and
affect the warranty terms.
•
Brakes
•
Always check that the brakes are working before driving.
•
Lock the brake pedals together whenever individual wheel brakes are not
required and always when driving on the road.
•
Extensive repairs to the braking system should be undertaken only by an
authorised Valtra workshop.
•
When implements or ballast weights are front-end mounted, the rear axle
loading is decreased:
•
Check that the rear brakes are still effective.
•
Use appropriate ballast weights at rear as required.
•
Cleaning
Keep the tractor clean to minimise risk of fire.
•
Lights
•
Make sure that lights and reflectors are clean and in working order.
•
Make sure that the headlights are correctly adjusted.
•
Steps
Keep the steps clean. Dirty steps can lead to falls and personal injury.
•
Quick couplings
DANGER: Clean the quick couplings and ball joints before
attaching an implement. There is risk that the implement is not
attached properly.
1. Safety precautions
- 14 -