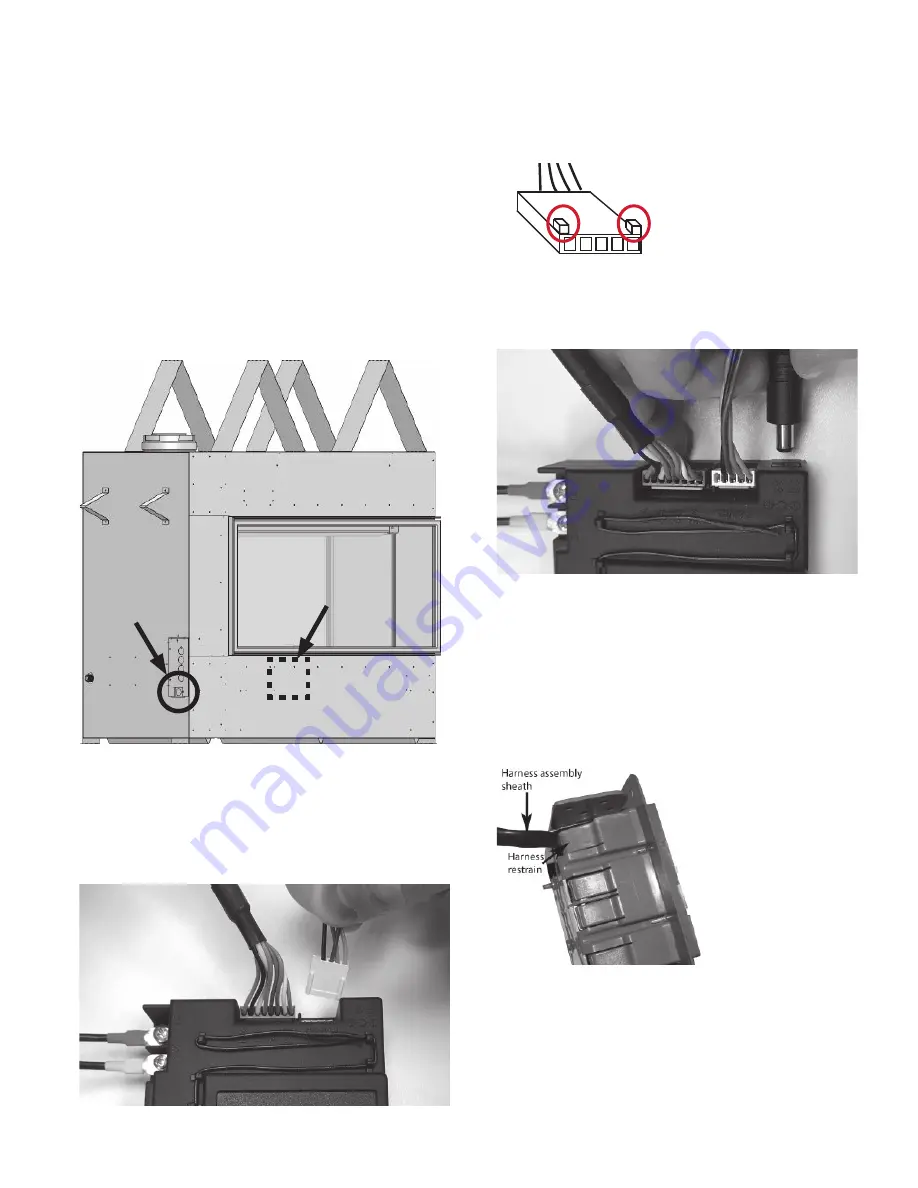
33
Installing Wall Switch Kit
A remote battery wall switch kit is provided with this
appliance. It is connected to the receiver in the
fi
replace.
The receiver is located under the bottom plate.
1. Decide where the switch is to be installed in the wall.
Do not locate the switch within the non-combustible
zone above the
fi
replace.
2. Thread the harness through the access hole in the
appliance, located below the electrical junction box.
DO NOT run the wire over top of the appliance.
3. Pull out the receiver. You can remove the ignition
wire to improve access.
4. Take the signal wire and plug it into the receiver’s
connection slot as indicated (the other slot should
already be
fi
tted with the valve’s wire harness
connector)
!
IMPORTANT: The connection
can only be done one way.
Do not force it or damage
the pins on the receiver box!
5. Connect the 6 volt power wire to the receiver.
6. On the outside of the
fi
replace, run the harness to
the junction box location. Use insulated type staples
to secure the wiring to framing.
7. Feed the harness assembly through a restraint on
the rear of the junction box, feeding through until
the harness sheath is pinched by the retainer. Ensure
there is su
ffi
cient wire length inside the junction box
to make connection to the switch plate and battery
holder.
8. Secure the junction box to the mounting surface
using appropriate fasteners (not supplied).
Entry
Receiver location
Installation
Wall Switch Kit