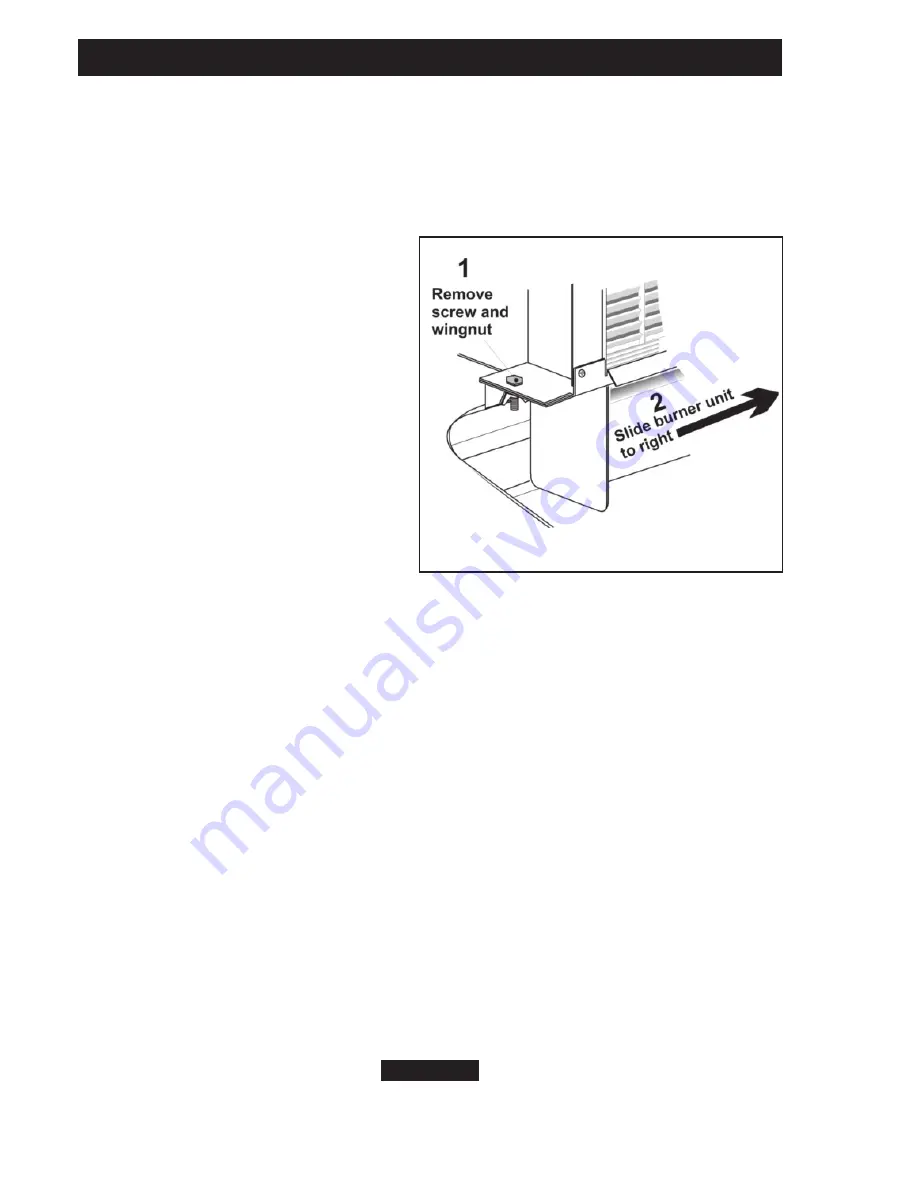
It is important to note the orientation of the ‘D’ flat at the top of the spindle as it
will need to be replaced in the same way.
4.
Detach the left end of the burner module from the radiant box by removing one
screw and a wingnut (See figure 19).
5.
Carefully slide the burner module to the right to free it from the right side of the
radiant box (See figure 19).
6.
Remove the pipes, gas tap or injectors as required.
7.
Replace in the reverse order.
Take care when replacing the injectors.
The injectors have ceramic tips at each
end. It is important not to allow jointing
compound to get on either end of the
injectors.
Make sure that the control knob with
spindle is correctly turned to agree with
the gas tap position before refitting the
split pin.
11.6 To grease the gas tap.
1.
Remove the burner module as section
11.6.
2.
Remove the circlip holding the piezo
generator to the tap and remove the
piezo generator.
3.
Remove the two screws from the head of the gas tap and remove the gas tap
head.
4.
Remove the spindle and spring from the tap.
5.
Note the position of the slot in the plug. Mark this position on the tap body.
6.
Rotate the plug and pull it out of the tap.
7.
Clean and grease the plug lightly with suitable grease. Do not apply excessive
grease. Particularly, make sure that the gas ports are not restricted by grease.
8.
Push the plug back into the tap body. Line up the slot in the plug with the mark
previously made on the tap body.
9.
Reassemble in the reverse order making sure that the components are correctly
engaged. Check the operation of the tap and ignition. Make sure that the control knob
with spindle is correctly turned to agree with the gas tap position before refitting the
split pin / ‘R’ clip.
Page 31
©
GDC Group Ltd. OCT 2016
INSTALLER GUIDE
Figure 19. Burner module removal