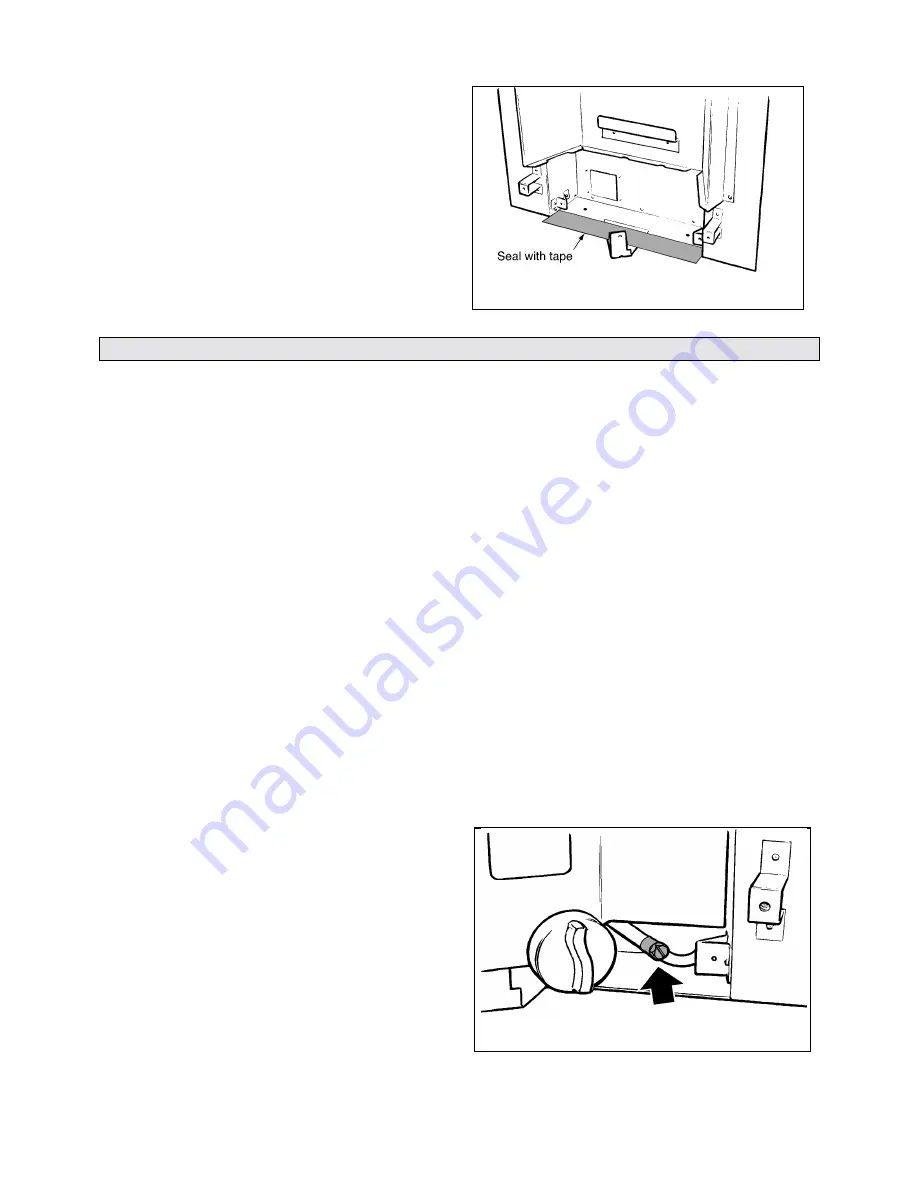
10
7.3
SEAL THE FLOOR FRONT
(ALL INSTALLATIONS)
Using the floor sealing tape supplied, seal the bottom
of the convection box to the fireplace and hearth
floor. Run the tape over the burner fixing bracket.
(see figure 15).
8.
BURNER, FRONT SURROUND & SUPPLY PIPE INSTALLATION
8.1
Refit the burner unit to the convection box with
three screws.
8.2
Locate the two lugs at the top of the front surround
in the slots in the convection box hood. Swing the
bottom of the surround sides back against the
convection box and lower the surround so that the
lugs are fully seated in the slots in the convection box
hood.
8.3
Refit the two screws to secure the surround sides to
the convection box brackets.
8.4
Connect the supply line to the appliance.
For right hand side connection.
The supply pipe
will have to be formed to go behind the control knob
and burner support bracket. The installation
template contains a diagram for bending this supply
pipe.
8.5
Pressure check the installation pipework for gas
soundness in accordance with the current edition of
BS6891.
A long brush may be required to reach
some joints
.
8.6
PRELIMINARY BURNER CHECKS
Some burner operations can be checked at this stage.
Checking now will mean that less disassembly will
be required if any problems are found.
A full check
should still be made, however, after final installation.
8.6.1
If closed
,
open the isolating valve at the inlet elbow.
8.6.2
Depress the control knob and turn anticlockwise
partially towards the “PILOT/IGN” position until
some resistance is felt. Keep depressed at this
position to purge air from the system then, while
keeping it depressed, turn fully to the “PILOT/IGN”
position. A spark should be generated at the pilot
while turning. The spark should ignite the pilot
.
8.6.3
When pilot ignition has been achieved, keep the
control knob depressed for approximately ten
seconds to allow the thermocouple probe to warm
up and then release it. If the pilot does not remain
alight, ensure that the air has been purged, that the
pilot orifice is clear and that the thermocouple
connections are sound. Replace the pilot unit if
necessary (see servicing section of this manual).
8.6.4
When the pilot is alight and stable, partially depress
the knob and turn to “LOW”. The pilot should then
light the main burner at its low setting. There may
be a delay of up to four seconds between the pilot
lighting and ignition of the gas at the main burner.
This is normal and is due to the time required to fill
the main burner compartment with sufficient gas for
ignition.
8.6.5
When the burner is operating properly, partially
depress the control knob and gradually turn it anti-
clockwise. The burner flames should gradually
increase until the knob reaches the “HIGH”
position.
When the above checks have been completed
partially depress the control knob and turn to “OFF”.
8.6.6
If the above checks are satisfactory, continue with the
installation. If not, check the control and ignition
circuitry and components as described in the
servicing section of this manual.
8.7
CHECK REFERENCE PRESSURE
The appliance is pre-set to give the correct heat input
at the inlet pressure shown in section 1 of this
manual. No adjustment is necessary. Check the
burner pressure by fitting a pressure gauge at the test
point. The test point is on the pipe situated below
the bottom right corner of the burner unit (See
figure 16). Check the pressure with the appliance
alight and set at maximum output.
After checking, turn off the appliance. Remove the
pressure gauge and replace the test point sealing
screw. Relight the appliance. Turn to the maximum
output position and test around the sealing screw for
gas soundness with a suitable leak detection fluid.
Fig. 15 Floor sealing
Fig. 16 Pressure test point