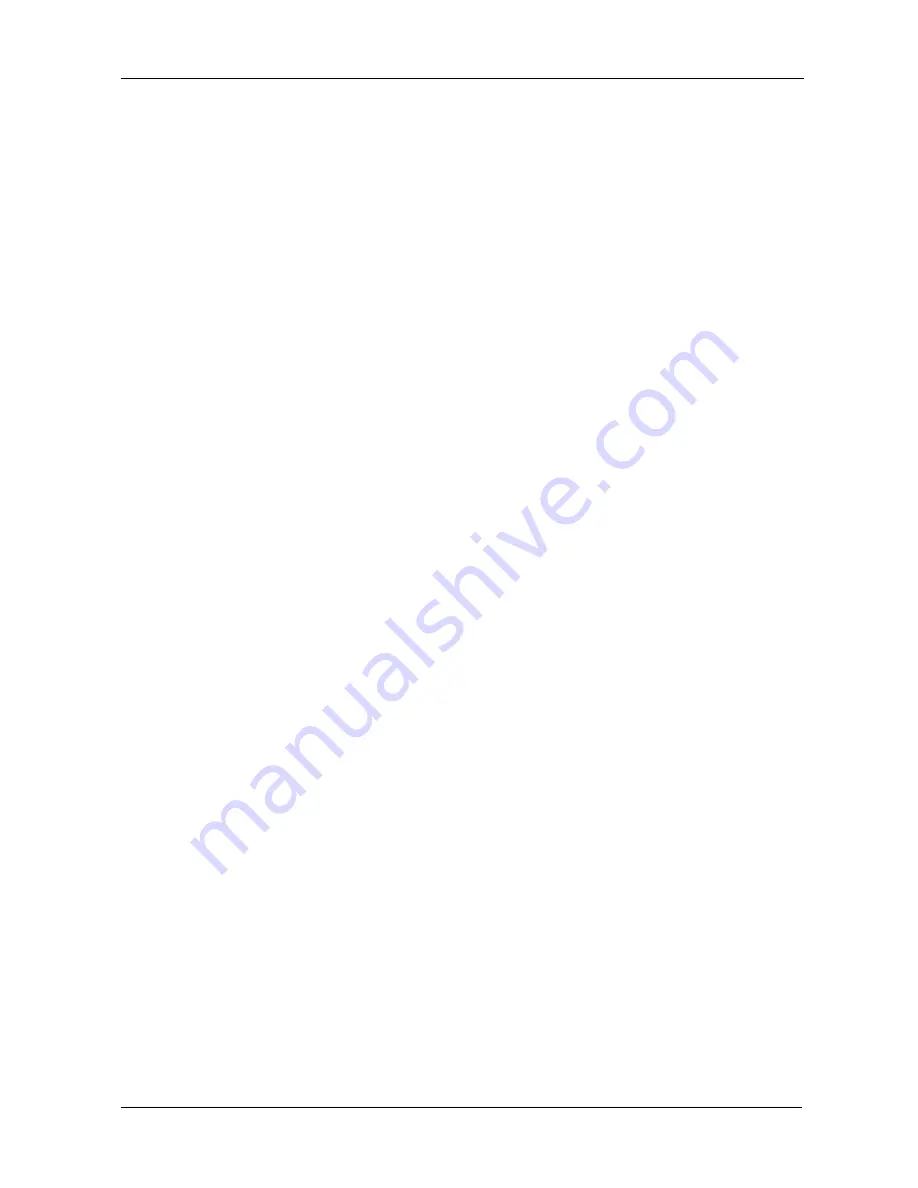
BCs160VA
Nov. 15, 1997
SMART-PULP
Smart Consistency Transmitter
29
3 SMART-PULP’S OPERATION AND CONSTRUCTION
SMART-PULP uses a piezoresistive force transducer to measure the shear force acting
on its sensor blade. The shear force is proportional to pulp consistency. Oil damping
prevents the effects of pipework vibration on the measurement.
The pulp, force transducer and electronics temperatures are measured, and the effects of
temperature variation are compensated for arithmetically in the electronics.
3.1 Construction
Mechanical (refer to Fig. 3.1a).
The sensor blade is mounted on a taper pin with
taper joint. The taper pin has a narrowing, or
”mechanical fuse”, at which the pin will flex in case
the sensor blade is overloaded. This will prevent
damage to the transmitter’s interior.
The taper pin is threaded to a counter pin. An inlet
diaphragm is pressed between the taper pin and
counter pin to prevent the admission of the process
medium to the transmitter’s interior. The diaphragm
is sealed on the inlet cone with a double O-ring
around its rim. The hole in the rotatable inlet cone is
eccentric and therefore enables compensation for
static pressure. The counter pin connects with a
damping cylinder pivoted on the transitter’s body.
Shear force F1 generates force F2 to the
piezoresistive transducer through the sensor blade,
taper pin, counter pin, damping cylinder, column and
connecting wire.
The piezoresistive transducer is fastened to the
inner body, which is attached to the transmitter’s
body. Motion limit clearance prevents overloading of
the force transducer. The free space inside the body
is filled with damping silicone oil. An expansion
diaphragm permits thermal expansion of the oil.
Gaskets are O-rings, except the process gasket
which is a PTFE ring with rectangular cross section.
The transducer that measures the process
temperature is located inside the transmitter’s body
as close as possible to the surface in touch with the
process medium. The wiring from the electronics to
the process temperature transducer and force
transducer passes through inlet plugs in the inner
cover.
The electronics housing is fastened with screws to
the inner cover. The electronics units are attached
with screws to the electronics housing at the bottom,
and supported through an O-ring on cover 1 at the
top. The wiring from the electronics to the terminal
board passes through oil-resistant radio interference
filters.
The operator unit is locked in position in the junction
box and connected with a flat cable and
disconnectible connector to the terminal board.
The transmitter will operate in the normal manner
even if the operator unit is disconnected.
The connecting cable is provided with two optional
inlets, one of which is covered with a plug while the
other is equipped with a cable gland with gasket.
The junction box’s cover (cover 2) is equipped with a
window when the operator unit is installed in the
transmitter as shown in Figure 3.1a. When the
operator unit with terminal board is mounted in an
optional remote wall box, cover 2 is replaced by
cover 1 and the terminal board with screw terminals
is of a different type (a version suitable for
connecting remote operator unit). The 9.75 m cable
between the remote wall box and transmitter is
connected permanently to the remote operator unit,
and its other end is connected to the transmitter’s
screw terminals. The connecting cable to the system
or consistency controller is connected to the remote
operator unit.
Electronics (refer to Fig. 3.1b).
The piezoresistive force transducer and electronics
have been matched to each other at the
manufacturer’s factory.
The sensor board, processor board, power supply
board and motherboard have been cast into a single
assembly which cannot be disassembled.
The four resistors that measure mechanical strain
and temperature are connected into a Wheatstone
bridge in the force transducer, and the four wires
from the resistors’ connection points are passed to
the sensor board in the electronics housing. The
wires from two other temperature measurements
(process and electronics) are also connected to the
sensor board.
The operator unit has an 8-character letter/number
liquid crystal display and four pushbutton keys, as
well as test point connections.
The terminal board has screw terminals for the
connecting cable’s signal wires.