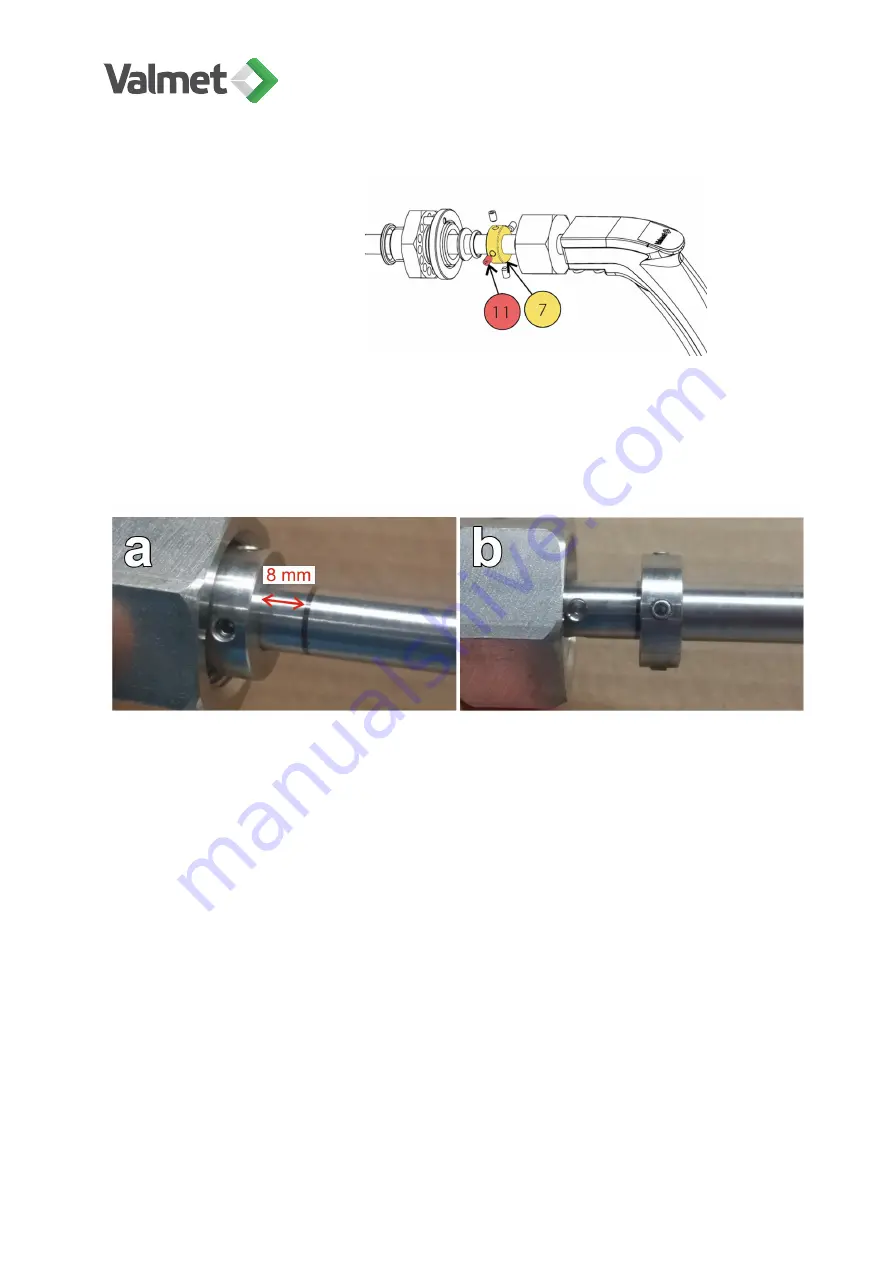
Open the 4 locking screws
(part 11) so that you can
move the locking ring (part
7) on the probe.
Move the locking ring 16 mm (0.6") towards the probe tip from its original position. In
newer sensor probes the position is marked on the probe. If there is no marking on the
sensor probe, draw a mark 8 mm (0.3") from the front surface of the locking ring (step
a
). Push the locking ring towards the probe tip, until the rear edge of the ring is aligned
with the marking (step
b
). Then tighten the 4 locking screws.
Installing the sensor | 18 (48)
K20798 V1.1 EN - 1 - 12/2019