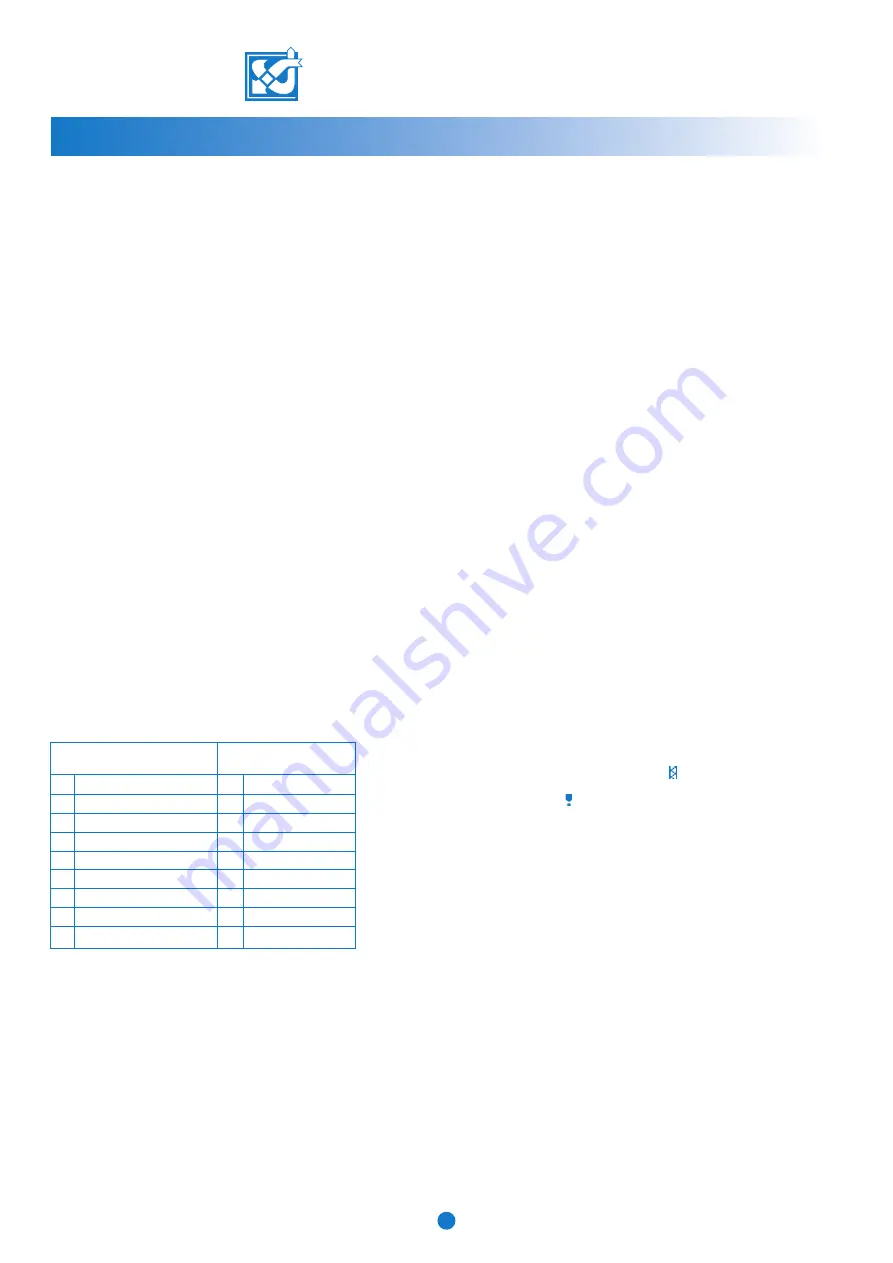
VALLOX DIGIT2 SE/VKL/MLV
© VALLOX • We reserve the right to make changes without prior notification.
DESCRIPTION OF OPERATION/ELECTRIC RADIATOR
12
Control of operation
Power supply to the unit can be controlled with a contactor in the
distribution panel if needed, e.g. with a timer programme. After
starting, the unit first operates at minimum power. After that power is
adjusted based either on the measurement data from air quality sensors
and/or on manual control at the control panel.
Fan speed adjustment
Manual control
Fan speed of the ventilation unit is controlled in 8 steps at control panel
H
.
Week-clock control
Fan speed of the ventilation unit is controlled in 8 steps using the week
clock in control panel
H
. The week clock can be used to programme
the desired fan power option and the setpoint for supply air temperature
for each day of the week and each hour in the day.
Carbon dioxide and humidity control
The fan capacity of the ventilation unit is controlled in multiple steps
depending on loads, and based on the measurement results of the air
quality sensors (CO
2
and %RH sensors) located in the ventilation zone.
The aim is to keep carbon dioxide and/or humidity content below the
threshold set at control panel
H
. It is also possible to select an automatic
search for the humidity content setpoint at control panel
H
. One or
more modes of control may be used simultaneously – the mode
demanding boosting is the dominant one. Fan speed varies depending
on load between the base and maximum fan speeds. The base and
maximum fan speeds can be set at the desired level at control panel
H
.
Control through voltage or current signal
The fan power of the ventilation unit is controlled in 8 steps with a
voltage signal of 0...10 VDC, or with a current signal of 0...20 mA.
However, fan power cannot be raised above the set maximum fan
speed. Voltage or current signal control is used to control base fan
speed. This means that fan speed can be raised when necessary, but
not lowered, by the manual, CO
2
and %RH controls.
Supply air temperature
Supply air temperature can be controlled with either constant temperature
control or cascade control.
Supply air constant temperature control
The control unit directs the operation of post-heating unit
LP2
on the
basis of the measurement data given by temperature sensor
TE2
, aiming
at keeping supply air temperature at the temperature value set on
control panel
H
(+10…+30 ºC).
Supply air cascade control
The control unit directs the operation of post-heating unit
LP2
on the
basis of the measurement data given by extract air sensor
TE4
, aiming
at keeping extract air temperature at the temperature value set on
control panel
H
(+10…+30 ºC).
Heat recovery bypass
Heat recovery is enabled whenever post-heating has been switched
on. Automatic heat recovery bypass is active whenever post-heating
has been switched off and outdoor temperature exceeds the setpoint
(to be set between 0 and +25
°
C). In this case, the control unit directs
the operation of damper motor
FG
on the basis of measurement results
given by outdoor temperature sensor
TE3
and extract air temperature
sensor
TE4
. The aim is to get as cool supply air to the ventilation zone
as possible. Heat recovery is, however, on whenever outdoor temperature
is below the limit set, or whenever outdoor air is warmer than extract
air.
Heat recovery antifreeze
The control centre of the unit controls the operation of preheating unit
LP1
on the basis of the measurement data of temperature sensors
TE1
and
TE3,
preventing freezing alerts and the stopping of supply air fan
TF
. If the capacity of preheating unit
LP1
is not sufficient or it is not on,
the control centre keeps stopping supply air fan
TF
on the basis of the
measurement data on temperature sensor
TE1
and
TE3
, thus preventing
the heat recovery cell from freezing. As soon as the risk passes, the
fan restarts automatically. The threshold temperature (-6...+15
°
C) and
the difference area (1 ...10
°
C) for antifreeze can be set at control
panel
H
. When fan
TF
stops, power supply from radiator
LP1
is stopped
and post-heating radiator
LP2
continues to heat.
For preheating to work, its threshold temperature has to be set at least
one degree higher than the threshold temperature controlling fan
stopping. Temperatures are adjusted at control panel
H
.
Overheat protection for the heating element
Overheat protection thermostats
TS1
and
TS2
monitor the surface
temperature of heating unit
LP2
and overheat protection thermostats
TS3
and
TS4
that of
LP1
. If surface temperature exceeds the threshold,
overheat protection is triggered and power supply to the heating unit
is stopped. Overheat protection for
TS1
and
TS3
is reset automatically,
whereas overheat protection for
TS2
and
TS4
is reset manually.
Alarms
Pressure difference switches
PDE1
and
PDE2
monitor the pressure
difference on the supply and extract air sides. If the pressure difference
rises too high because of dirty filters or clogged ducts, an alarm will
be issued. This is indicated by a symbol ( ) in the main display of the
control panel. If the unit is not equipped with pressure difference
switches, the symbol ( ) appearing in the main display of the control
panel reminds of the need of servicing the unit. The reminder interval
can be set at 1...15 months. The factory setting is 4 months. This
function is always active.
The fault signal relay in the unit gives potential-free alarm indications
on the following fault conditions:
•
Alarm of high carbon dioxide content (> 5000 ppm) switches the
relay at 1-second intervals.
•
In other fault situations, such as sensor faults, the contacts of the
relay close.
Booster or fireplace switch function
The booster or fireplace switch function of the ventilation unit is controlled
either at control panel
H
and/or separate switch
S
, which can be
connected to the connection box of the unit. The mode of operation
of the switch is selected at control panel
H
. The booster switch function
raises fan speed to the set maximum fan speed for 45 minutes. The
fireplace switch stops the extract air fan for 15 minutes and produces
overpressure in the ventilation zone. LON remote monitoring control
can be implemented with a VALLOX LON converter. (See a separate
brochure.)
Voltage values
for each fan speed:
0
0.20...1.25 VDC
1
1.75...2.25 VDC
2 2.75...3.25 VDC
3 3.75...4.25 VDC
4 4.75...5.25 VDC
5 5.75...6.25 VDC
6 6.75...7.25
VDC
7
7.75...8.25 VDC
8 8.75...10.00
VDC
Current signal values
for each fan speed:
0 0.5...2.5 mA
1
3.5...4.5 mA
2
5.5...6.5 mA
3 7.5...8.5 mA
4 9.5...10.5 mA
5 11.5...12.5
mA
6 13.5...14.5
mA
7 15.5...16.5
mA
8 17.5...20.0
mA
Voltage and current signal values (selection in the motherboard)