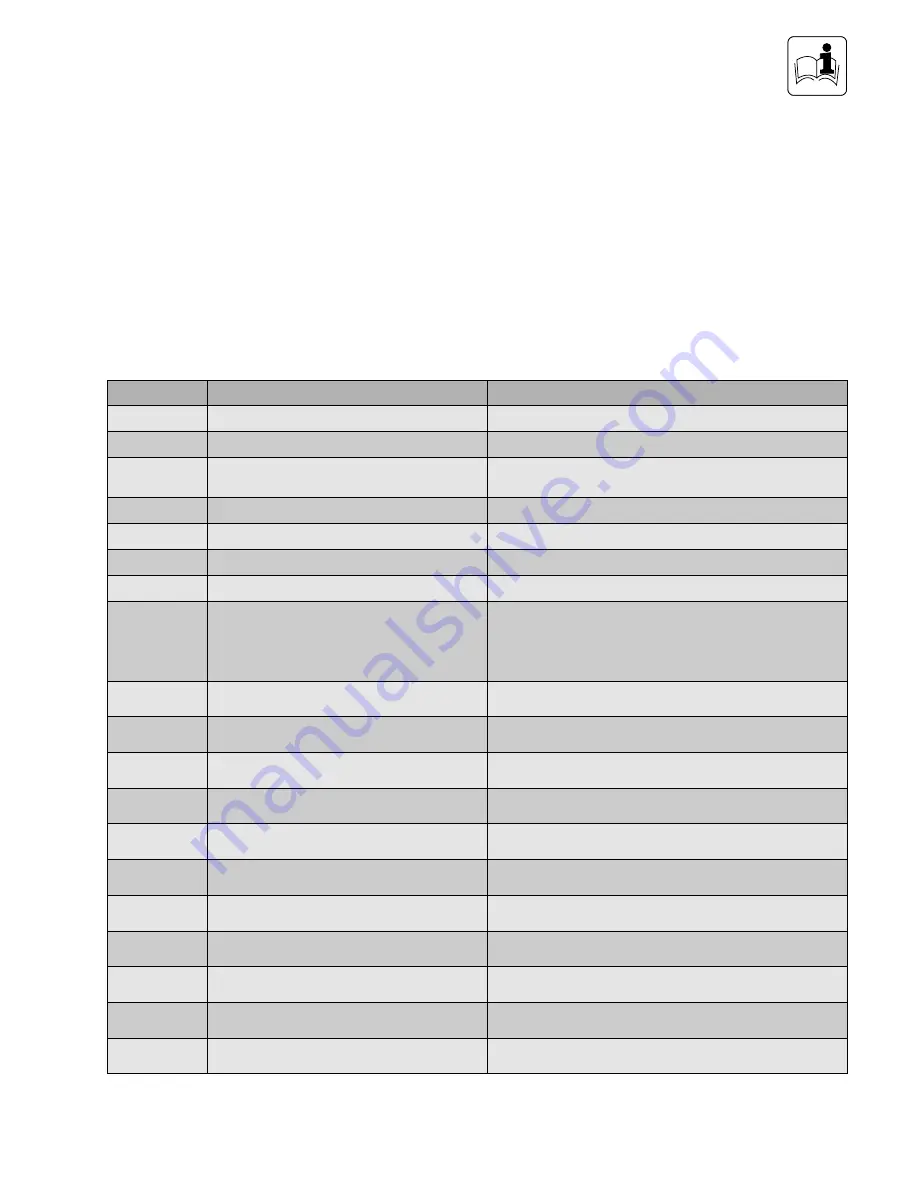
75
FAULT FINDING
Diagnostic Modes
In order to assist with the pinpointing
of a particular fault it is possible to
use the boiler display in a diagnostic
mode to interrogate the boiler about
the status of certain components.
●
Press the
„i“
and
„+“
buttons
below the display simultaneously.
The display will now show
„d.00“
.
●
Use
„+“
or
„-“
buttons to scroll up
or down to the desired diagnosic
number.
●
Press
„i“
button to display the
corresponding diagnosic
information.
●
If necessary, you can now alter the
value by pressing
„+“
or
„-“
buttons. (When altering values
display will flash). Press and hold
the "i” button to save the value to
memory, when the value is saved
the display will stop flashing.
Diagnosic mode is cancelled as
follows:
●
Press the
„i“
and
„+“
buttons
simultaneously
or
●
Do not press any key for
approximately four minutes. The
display will now revert back to
showing the current flow
temperature.
Display
Indication
Displayed values/adjustment values
d.00
Part load setting
0, 1, 2 …15 (factory-adjusted to 15 = max. rating)
d.01
Water pump over run
1, 2, 3, …60 min (factory adjusted setting: 5 min)
d.02
Maximum burner anti cycling period at 20 °C
flow temperature
8 - 60 min (predelivery setting: 15 min)
d.04
Not applicable
d.05
Flow temperature setting
°C
d.06
Not applicable
d.07*
1. Vantage hot water temperature
(not applicable)
2. Warmstart temperature setting
(applies to TURBOmax Plus only)
1. 15 - 75 °C
2. 40 - 65 °C
d.08
External controls heat demand
0 = open, no demand
1 = closed, demand
d.09
Not applicable
d.10
Pump status
1 = ON
0 = OFF
d.11
External pump status
1 = ON
0 = OFF
d.21
Flame rectification
1 = ON
0 = OFF
d.22*
Domestic hot water demand
1 = ON
0 = OFF
d.23
Summer/winter function (control knob)
1 = winter
0 = summer
d.24
Air pressure switch
1 = Closed
0 = Open
d.25*
Warmstart status (TURBOmax Plus)
1 = ON
0 = OFF
d.30
Gas valve status
1 = ON
0 = OFF
d.35*
Diverter valve position (THERMOcompact)
1 = hot water
0 = heating system
Table St.2: Diagnostic Modes 1 of 2
* TURBOmax Plus only
d.03
Not applicable