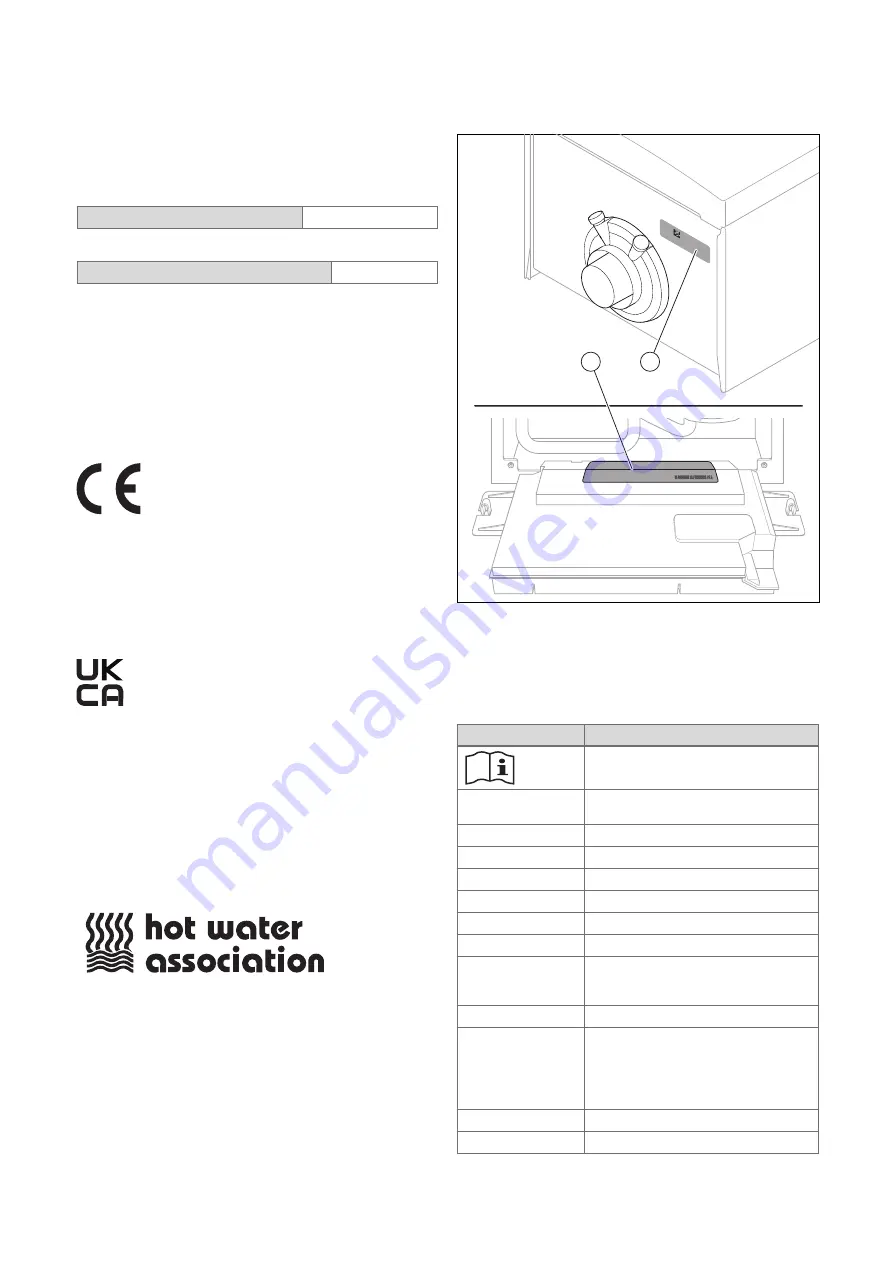
10
Installation and maintenance instructions 0020308121_04
4
Notes on the documentation
▶
Always observe all the operating and installation instruc-
tions included with the system components.
▶
Pass these instructions and all other applicable docu-
ments on to the end user.
These instructions apply for the following products only:
Product article number
VUI 30/40
0010036114
Gas Council Numbers
VUI 30/40CS/1-5 (N-GB) ecoTEC plus 940
47-044-96
These instructions apply only to:
–
Great Britain
–
Ireland
5
Product description
5.1
CE marking
The CE marking shows that the products comply with the
basic requirements of the applicable directives as stated on
the declaration of conformity.
The declaration of conformity can be viewed at the manufac-
turer's site.
5.2
UKCA mark
The UKCA marking shows that the products comply with the
basic requirements of the applicable directives as stated on
the declaration of conformity.
The declaration of conformity can be viewed at the manufac-
turer's site.
5.3
Hot Water Association
Vaillant is a full member of the Hot Water Association and
promotes the scheme in association with its cylinder range.
Details are available on the web site www.vaillant.co.uk
5.4
Water Regulations Advisory Scheme
The product meets the requirements of this quality standard.
5.5
Data plate
2
1
Two data plates are attached to the product at the factory.
The data plate on the top of the unit
(2)
is always accessible
and contains the basic information for the chimney sweep.
The main data plate
(1)
with all of the information is attached
to the rear of the electronics box. Any information that is not
listed here can be found in separate sections.
Information
Meaning
Read the instructions.
VCI, VUI, VMI, VHR
I
Product with integrated domestic hot
water generation
10 - 36
Nominal heat output
C
Condensing boiler
S
Stainless steel heat exchanger
/1
Product generation
-5
Product equipment
N, E
Gas group
E.g. AT, BE, CH,
DE, DK, ES, FR, IT,
NL, NO, PL, SE
Target market
ecoTEC plus
Marketing name
E.g. I2N, 2N, I2ELw,
I2H, G20
–
20 mbar
(2.0 kPa)
E.g. I3P, G31
–
50 mbar (5.0 kPa)
Gas group and gas connection pressure
as set at the factory
Cat.
Gas boiler category
Type
Unit types
Summary of Contents for ecoTEC plus VUI Series
Page 1: ...en Installation and maintenance instructions ecoTEC plus VUI 0020308121_04 31 05 2023...
Page 98: ......
Page 99: ......