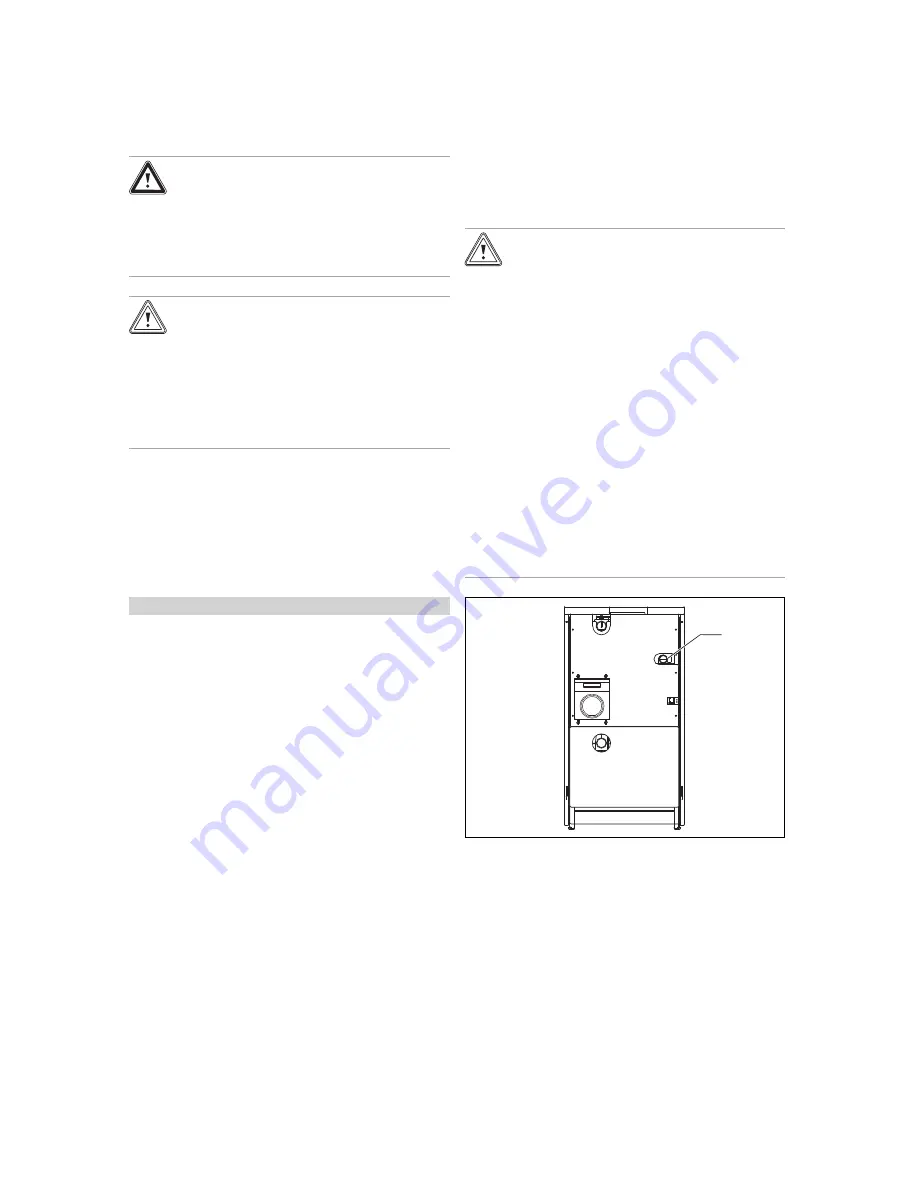
Installation 5
0020149561_01 ecoCRAFT exclusive Installation and maintenance instructions
11
5
Installation
5.1
Preparing for installation
Danger!
Risk of scalding and/or risk of material
damage due to incorrect installation lead-
ing to escaping water.
Stresses in supply lines can cause leaks.
▶
Install the supply lines without tension.
Caution.
Risk of material damage due to contamin-
ated lines.
Foreign bodies, such as welding remnants,
sealing residues or dirt in the supply lines,
may cause damage to the product.
▶
Blow or flush the supply lines thoroughly
prior to installation.
▶
Install an expansion relief valve on-site.
▶
A discharge pipe with inlet funnel and siphon must be
routed on-site from the discharge line of the expansion
relief valve to a suitable drain in the installation room.
The drain must be visible.
▶
Install a purging device at the highest point in the heating
installation.
▶
Install a filling/draining device in the heating installation.
Conditions
: Plastic pipes present in the heating installation
▶
Install a suitable thermostat at the heating flow on-site in
order to protect the heating installation against temperat-
ure-related damage.
▶
Connect the thermostat to the terminals for the surface-
mounted thermostat (blue ProE plug).
▶
Use seals that are made of a paste-like fibre material
because seals that are made of rubber-like materials
may be subject to plastic deformation, which can lead
to pressure losses.
5.2
Required accessories (on-site)
The following required accessories (to be provided on-site)
are necessary for the installation:
–
Gas isolator cock with fire protection device
–
Expansion relief valve, heating side
–
Service valves (heating flow and return)
–
Low loss header (optional)
–
Heat generator pump
–
Expansion vessel
–
Controller
–
Flue pipe
–
Condensate pump (optional)
–
Neutralising unit
–
Automatic air vent
5.3
Performing the gas installation
Using the incorrect type of gas may cause fault shutdowns in
the product. Ignition and combustion noise may occur in the
product.
▶
Only use the gas type listed on the identification plate.
▶
Make sure that the existing gas meter is capable of
passing the rate of gas supply required.
Caution.
Risk of material damage due to the gas
leak-tightness test.
At a test pressure of >11 kPa (110 mbar), gas
leak-tightness tests may cause damage to
the gas valve.
▶
If, during gas leak-tightness tests, you
also place the gas lines and the gas valve
in the product under pressure, use a max.
test pressure of 1.1 kPa (110 mbar).
▶
If you cannot limit the test pressure to
11 kPa (110 mbar), close any gas isolator
cocks that are installed upstream from the
product before you carry out the gas leak-
tightness test.
▶
If, during gas leak-tightness tests, you
have closed the gas isolator cock that is
installed upstream of the product, relieve
the gas line pressure before you open this
gas isolator cock.
1
▶
The cross-sections of the gas pipe must be designed to
suit the nominal floor-standing boiler heat loading.
▶
Install the gas line without tension on the connection in
the product
(1)
in accordance with the recognised rules of
engineering practice.
▶
Remove the residues from the gas pipe by blowing
through the gas pipe.
▶
Install a gas isolator cock with fire protection device in the
gas line, upstream from the product, at an easily access-
ible location. The gas stopcock must be at least the same
nominal size as the gas connection (R 1.5").
▶
Purge the gas line before start-up.