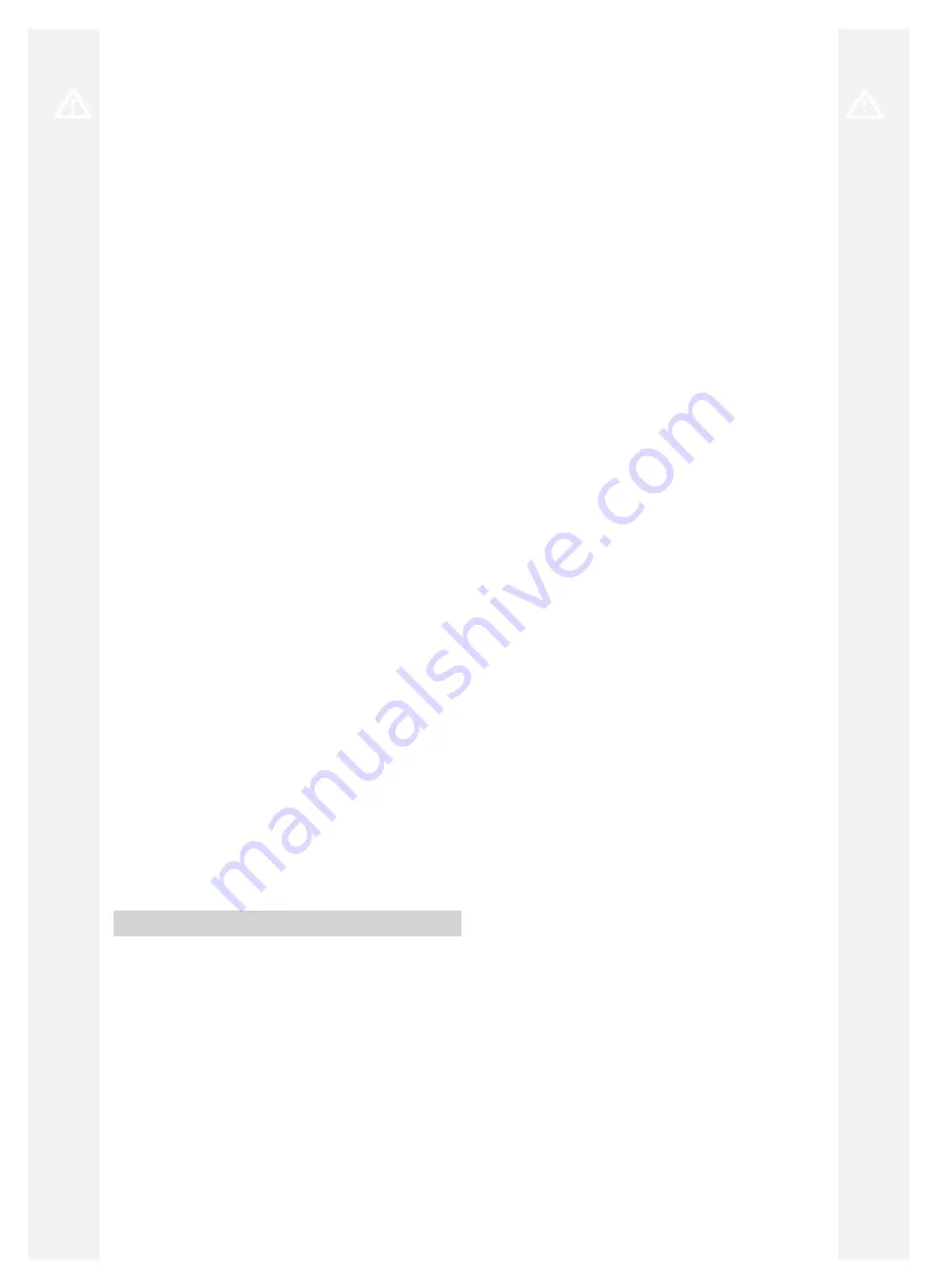
1 Safety
4
Installation and maintenance instructions atmoMAG 0020271929_00
▶
Use a telephone outside the building to
inform the emergency service department
of the gas supply company.
1.3.3 Risk of death from leaks if the
product is installed below ground
level
Liquid gas accumulates at floor level. If the
product is installed below ground level, liquid
gas may accumulate at floor level if there
are any leaks. In this case, there is a risk of
explosion.
▶
Make sure that liquid gas cannot escape
from the product or the gas line under any
circumstance.
1.3.4 Risk of death due to blocked or
leaking flue gas routes
Installation errors, damage, tampering, unau-
thorised installation sites or similar can cause
flue gas to escape and result in a risk of pois-
oning.
What to do if you smell flue gas in the prop-
erty:
▶
Open all accessible doors and windows
fully to provide ventilation.
▶
Switch off the product.
▶
Check the flue gas routes in the product
and the flue gas diversions.
1.3.5 Risk of death due to explosive and
flammable materials
▶
Do not use the product in storage rooms
that contain explosive or flammable sub-
stances (such as petrol, paper or paint).
1.3.6 Risk of poisoning caused by
insufficient supply of combustion air
Conditions
: Open-flued operation
▶
Ensure that the air supply to the product's
installation room is permanently unobstruc-
ted and sufficient in accordance with the
relevant ventilation requirements.
1.3.7 Risk of corrosion damage due to
unsuitable combustion and room air
Sprays, solvents, chlorinated cleaning
agents, paint, adhesives, ammonia com-
pounds, dust or similar substances may lead
to corrosion on the product and in the flue
system.
▶
Ensure that the supply of combustion air is
always free of fluorine, chlorine, sulphur,
dust, etc.
▶
Ensure that no chemical substances are
stored at the installation site.
▶
If you are installing the product in
hairdressing salons, painter's or joiner's
workshops, cleaning businesses or similar
locations, choose a separate installation
room in which the room air is technically
free of chemical substances.
▶
Ensure that the combustion air is not
routed through chimneys which have
previously been used with floor-standing
oil-fired boilers, or with other boilers,
which could cause soot to build up in the
chimney.
1.3.8 Risk of poisoning due to missing flue
gas monitoring device
Flue gases may escape into the installa-
tion room under unfavourable conditions. If
this happens, the flue gas monitoring device
switches the heat generator off. If a flue gas
monitoring device has not been installed, the
heat generator will continue to run.
▶
Never decommission the flue gas monitor-
ing device.
1.3.9 Risk of death due to cabinet-type
casing
Cabinet-type casing can give rise to danger-
ous situations when used on a product which
is operated with an open flue.
▶
Ensure that the product is supplied with
sufficient combustion air.
1.3.10 Risk of material damage caused by
frost
▶
Do not install the product in rooms prone
to frost.
1.3.11 Risk of death due to lack of safety
devices
The schematic drawings included in this doc-
ument do not show all safety devices re-
quired for correct installation.