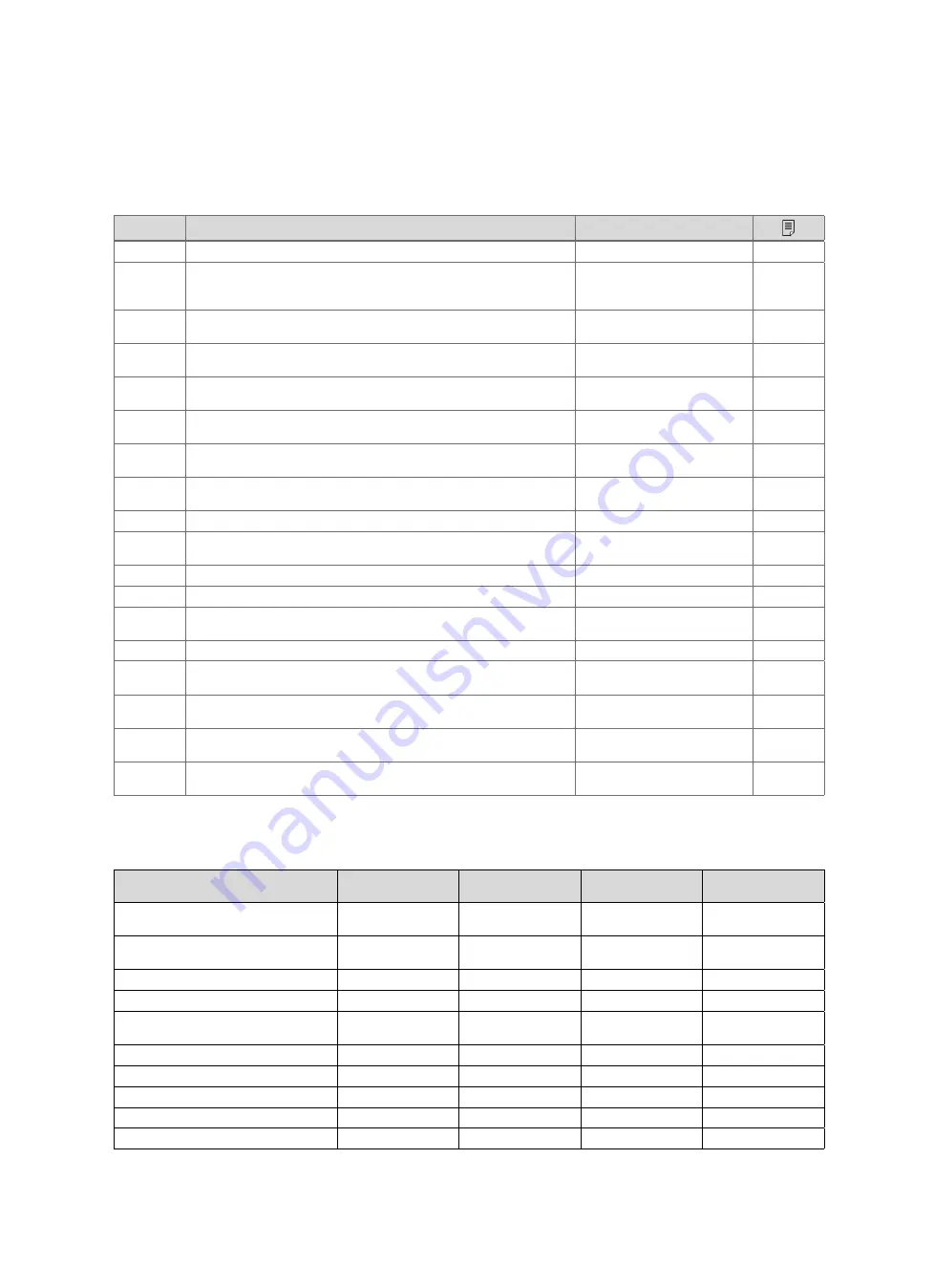
Appendix
26
Installation and maintenance instructions atmoMAG 0020271929_00
F
Inspection and maintenance interval
The table below lists the manufacturer requirements with respect to minimum inspection and maintenance intervals. If na-
tional regulations and directives require shorter inspection and maintenance intervals, you should observe these instead of
the intervals listed. Each time inspection and maintenance work is carried out, carry out the required preparatory and com-
pletion work.
#
Maintenance work
Interval
1
Remove any dirt from the product
Annually
2
Check the flue gas sensor for dirt and damage. Checking that the flue
gas sensor is working correctly by completely blocking the flue gas with
flue gas restrictors
Annually
3
Cleaning the burner
If required, at least every
2 years
17
4
Cleaning the heat exchanger
If required, at least every
2 years
18
5
Cleaning the injector rail
If required, at least every
2 years
17
6
Cleaning the down-draught diverter
If required, at least every
2 years
17
7
Check the ignition electrode and thermocouple for damage, and replace
any bent and damaged components
Annually
8
Checking the seals on the test nipples for damage and replacing any
damaged seals
Annually
9
Checking that the water flow switch (micro switch) is working correctly
Annually
10
Carry out a test operation on the product, incl. domestic hot water gener-
ation
Annually
11
Checking leak-tightness
Annually
15
12
Checking the heat input
Annually
19
13
Check the flame pattern. Flames must not touch the heat exchanger shaft
If required, at least every
2 years
14
Visually inspecting the test nipples and hoses
Annually
15
Interrupt the thermocurrent by disconnecting the connection between the
thermocouple and holding magnet. The product must be shut down
Annually
16
Checking the water valve
If required, at least every
2 years
18
17
Logging flue-gas measured values and any maintenance work that was
carried out
Annually
18
Checking the product to see if flue gas is escaping at the down-draught
diverter, with the doors and windows closed and the casing installed
Annually
G
Technical data
Technical data
–
General
MAG 114/1 G(E-
BE/FR)
MAG 114/1 G(H-
DACH)
MAG 114/1 G(LL-
DE)
MAG 114/1 G(P-
BE/FR)
Designated country (designation in
accordance with ISO 3166)
BE, FR
AT, CH, DE
EN
BE, FR
Approved gas boiler category
I
2E+
, I
3P
(BE), II
2E+3P
(FR)
II
2ELL 3P
(DE), II
2H3P
(AT, CH)
II
2ELL 3P
I
2E+
, I
3P
(BE), II
2E+3P
(FR)
Unit dimensions, height
680 mm
680 mm
680 mm
680 mm
Unit dimensions, width
350 mm
350 mm
350 mm
350 mm
Unit dimensions, depth (incl. rotary
switch)
270 mm
270 mm
270 mm
270 mm
Flue pipe connection diameter
110 mm
110 mm
110 mm
110 mm
Min. length of the flue pipe
0.5 m
0.5 m
0.5 m
0.5 m
Gas connection diameter
1/2
″
conical
1/2
″
conical
1/2
″
conical
1/2
″
conical
Water connection diameter (inlet)
G1/2
″
G1/2
″
G1/2
″
G1/2
″
Water connection diameter (outlet)
G1/2
″
G1/2
″
G1/2
″
G1/2
″