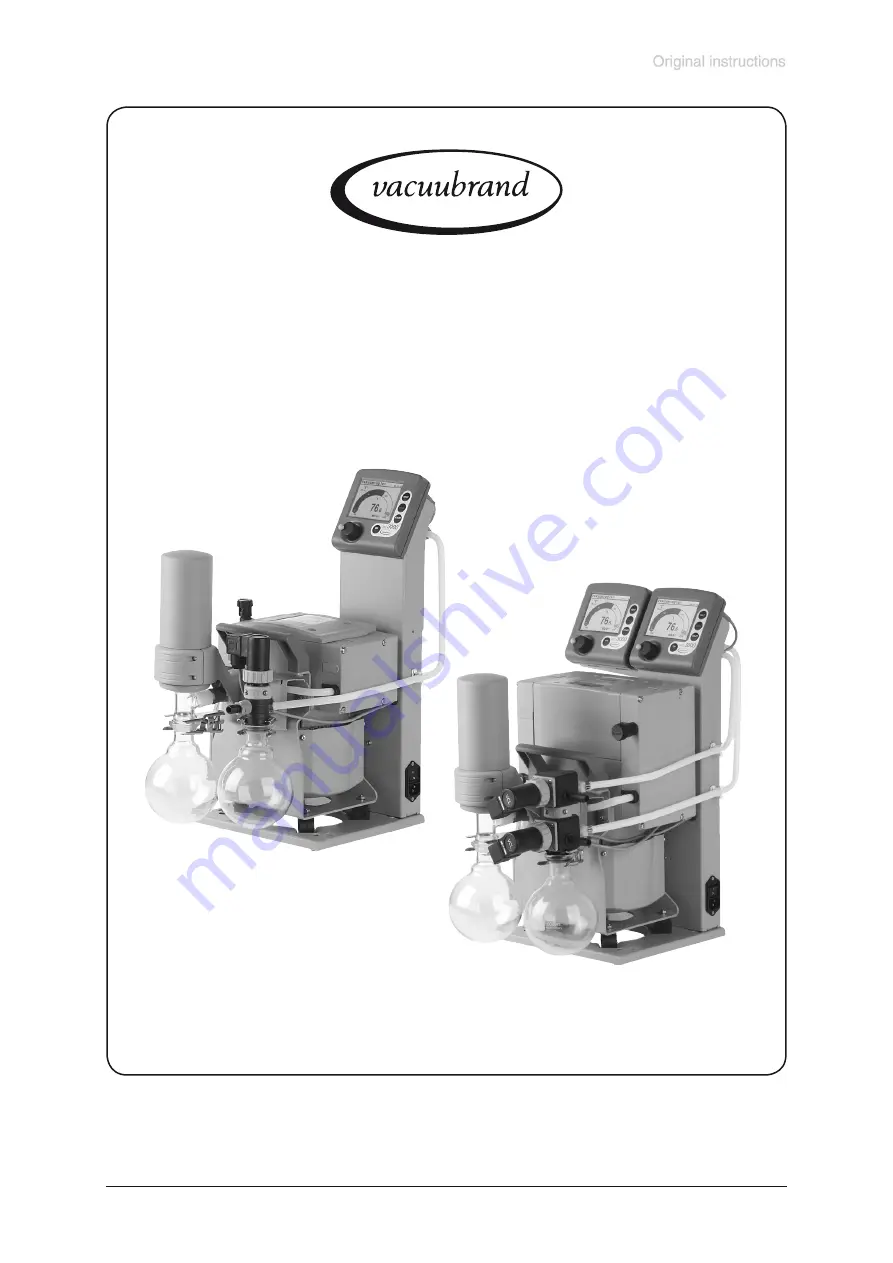
page 1 of 63
Documents are only to be used and distributed completely and unchanged. It is strictly the users´ responsibility to check carefully
the validity of this document with respect to his product. Manual-no.: 999188 / 19/05/2009
Chemistry pumping unit
Technology for Vacuum Systems
Instructions for use
PC 510 NT / PC 511 NT / PC 520 NT
PC 610 NT / PC 611 NT / PC 620 NT