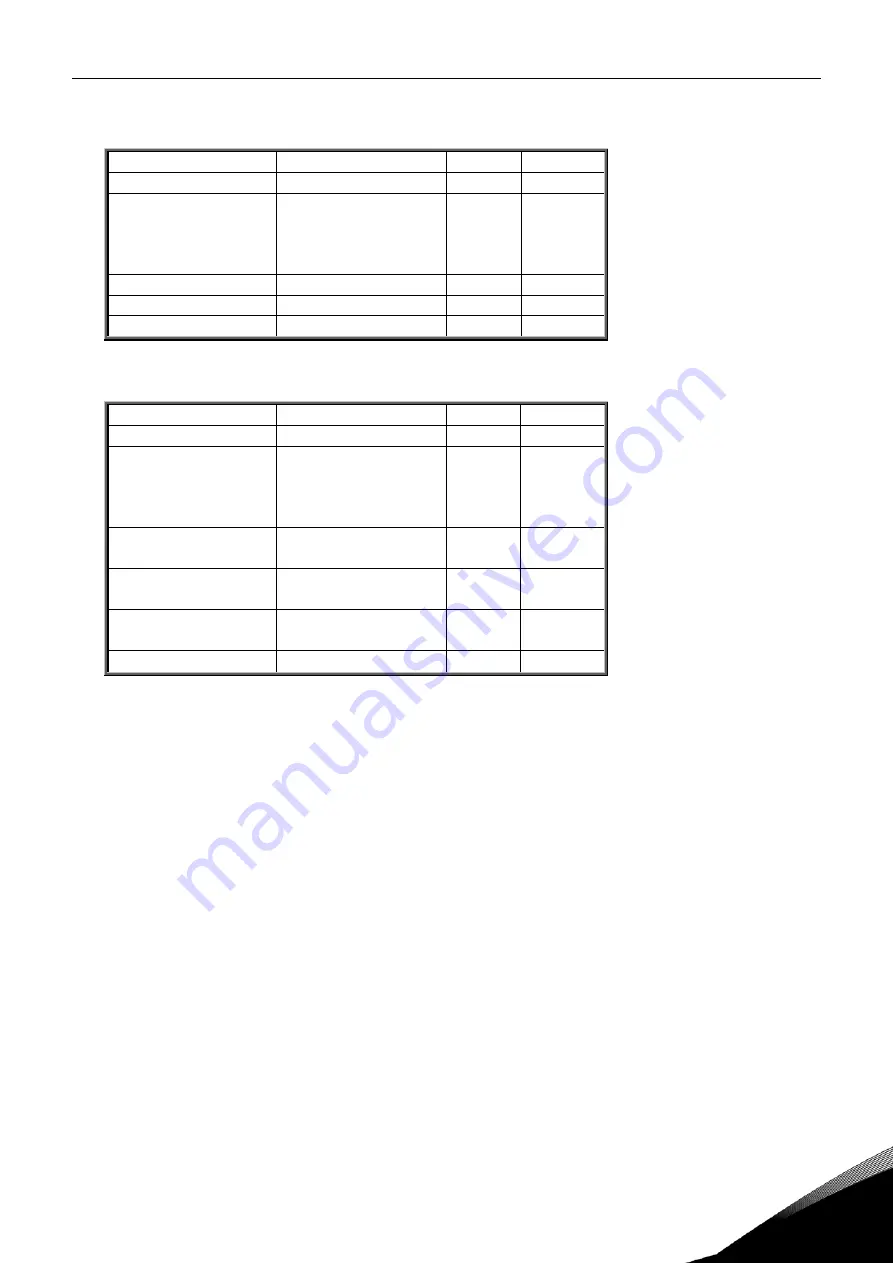
appendices
vacon • 47
24-hour s358 (0)40 837 1150 • Email: [email protected]
11
Multipurpose control application
Data
Value
Unit
Scale
Reference
Speed Reference
%
0.01%
ControlWord
Start/Stop
Command
Fault reset
Command
-
-
Process Data IN1
Torque Reference
%
0.1%
Process Data IN2
Free Analog INPUT
%
0.01%
PD3 – PD6
Not Used
-
-
PID control and Pump and fan control applications
Data
Value
Unit
Scale
Reference
Speed Reference
%
0.01%
ControlWord
Start/Stop
Command
Fault reset
Command
-
-
Process Data IN1
Reference for PID
controller
%
0.01%
Process Data IN2
Actual Value 1 to PID
controller
%
0.01%
Process Data IN3
Actual Value 2 to PID
controller
%
0.01%
PD4–PD6
Not Used
-
-
appendix d
Version 8 of the C6 Option board doesn’t work the same way than the others. Some changes are
required at end of the PLC.