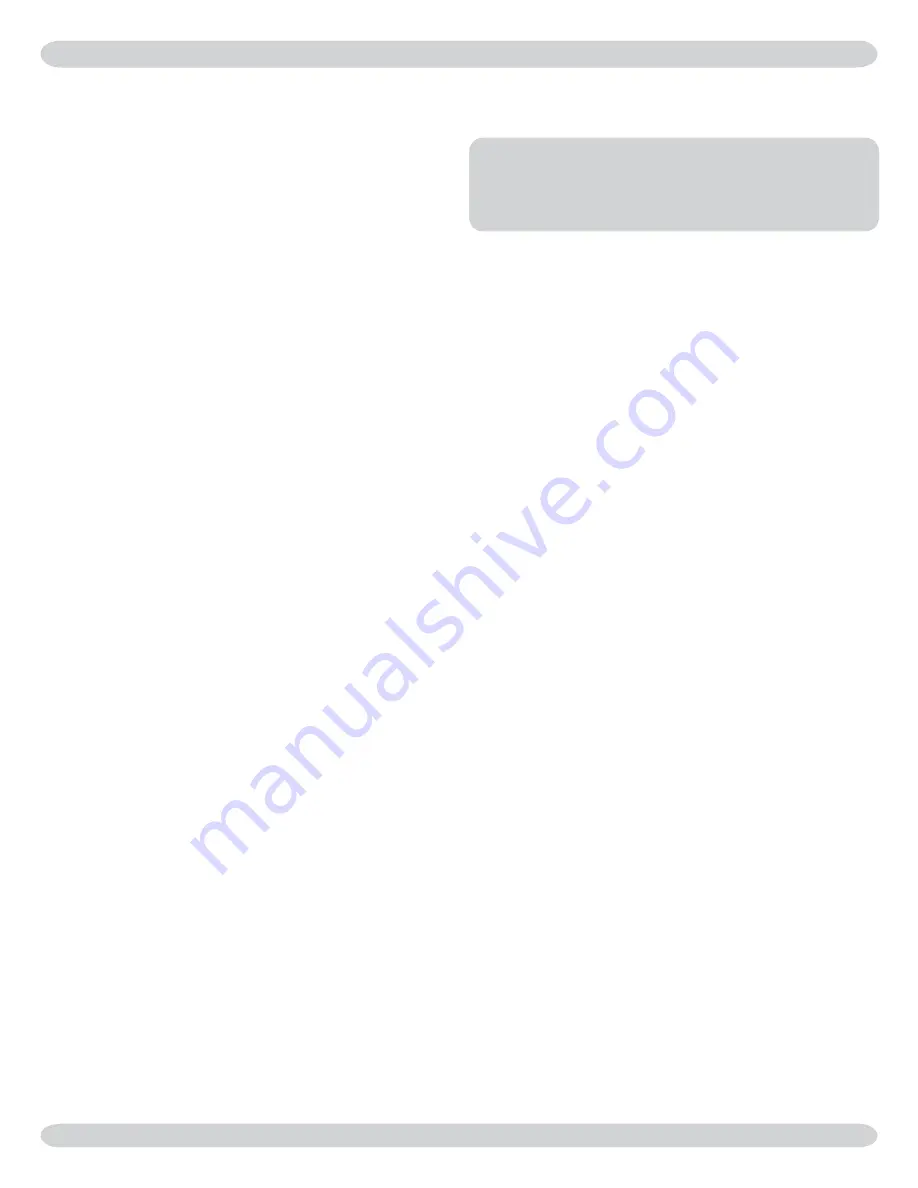
49
Monthly During Heating Season
1. Remove jacket front and top panels and check for pip-
1.
ing leaks around relief valve and other fittings. If found,
contact a qualified service agency to repair. DO NOT use
stop leak compounds.
2. Test relief valve. Refer to valve manufacturers instruc-
2.
tions packaged with relief valve.
3. Visually inspect venting and air intake system for
3.
proper function, deterioration, or leakage. If the vent
or air intake show any signs of deterioration or leakage,
contact a qualified service agency to repair or replace them
immediately and to insure proper reassembly and reseal-
ing of the vent and air intake system.
4. Visually inspect the clear vinyl condensate lines and the
4.
PVC condensate drain pipe for proper operation, leakage,
and deterioration. If the condensate lines or drain pipe
show any signs of blockage, leakage, or deterioration con-
tact a qualified service agency to clean, repair, or replace
them immediately.
5. Check the air baffle located inside 1 ½” x 2” flexible
5.
coupling, clean it if necessary and make sure to put it back.
Refer to repair parts diagram, mixer and pressure switch
assembly.
Periodically During Heating Season
Where low water cut offs are used, a periodic inspection of
the low water cut off is necessary, including flushing of float
type devices. Refer to low water cut off manufacturer’s specific
instructions.
End Of Each Heating Season - Annual Shutdown
Procedure
Follow instructions “TO TURN OFF GAS TO APPLIANCE”.
If heating system is to remain out of service during freezing
weather, and does not contain antifreeze, drain system com-
pletely. If boiler will be exposed to freezing temperatures, drain
condensate lines. Otherwise, do not drain system or boiler.
Annual Examination And Cleaning Of Boiler
Components
The following service procedures must be performed only
by a qualified service agency. Boiler owner should not at-
tempt these procedures.
Before Servicing, turn off electrical power to boiler at ser-
1.
vice switch. Close manual gas valve to turn off gas supply
to boiler.
Cleaning Flue passages between boiler sections.
2.
Any buildup of sediment or aluminum oxide (white
A.
powdery or flaky substance) in the flue passages must be
cleaned as follows:
Remove jacket front and top panels. Disconnect con-
B.
densate drain line from the barbed fitting on the bottom
of the boiler. Keep the open end of the drain line above
the water level in the condensate trap to prevent the trap
from draining. Disconnect pressure switch hose from
barbed fitting on gas valve. Disconnect 1½ x 2” flexible
coupling from air inlet. Disconnect air by-pass (½” trans-
parent vinyl tube) from the bottom of the mixer.
Remove air baffle from ½” x 2” flexible coupling and
C.
clean air baffle if necessary. Refer to repair parts diagram,
mixer and pressure switch assembly.
Confirm that manual gas valve is closed and disconnect
D.
gas line to gas valve at union. Disconnect wires to gas
valve. and igniter.
Loosen but do not remove five (5) nuts attaching mixer
E.
assembly to boiler. Remove two (2) igniter screws and
very carefully remove the igniter. Use care when remov-
ing the igniter, it is very brittle!
Remove five (5) nuts and remove mixer assembly. Re-
F.
move burner and mixer gasket.
Aluminum oxide deposits are water soluble and may
G.
be rinsed away with spraying or running water. Before
rinsing, connect a ½” I.D. hose to the barbed fitting on
the bottom of the boiler and run the hose to a bucket or
drain.
MAINTANANCE AND CLEANING
Summary of Contents for UB90-100
Page 15: ...15 Near Boiler Piping Figure 2 Single Zone Boiler Piping ...
Page 16: ...16 Figure 3 Multi zone Boiler Piping With Zone Valves Near Boiler Piping ...
Page 19: ...19 Figure 6 Diaphragm Type Expansion Tank Piping Near Boiler Piping ...
Page 20: ...20 Figure 7 Conventional closed type Expansion Tank Piping Near Boiler Piping ...
Page 27: ...27 Combustion Air and Vent Pipe Figure 11 Combustion Air and Vent Piping ...
Page 32: ...32 Electrical Wiring Figure 13 Field Wiring Connections ...
Page 53: ...53 DETAILED SEQUENCE OF OPERATION ...
Page 57: ...57 TROUBLESHOOTING CHART 2 TROUBLESHOOTING ...
Page 58: ...58 TROUBLESHOOTING CHART 3 TROUBLESHOOTING ...