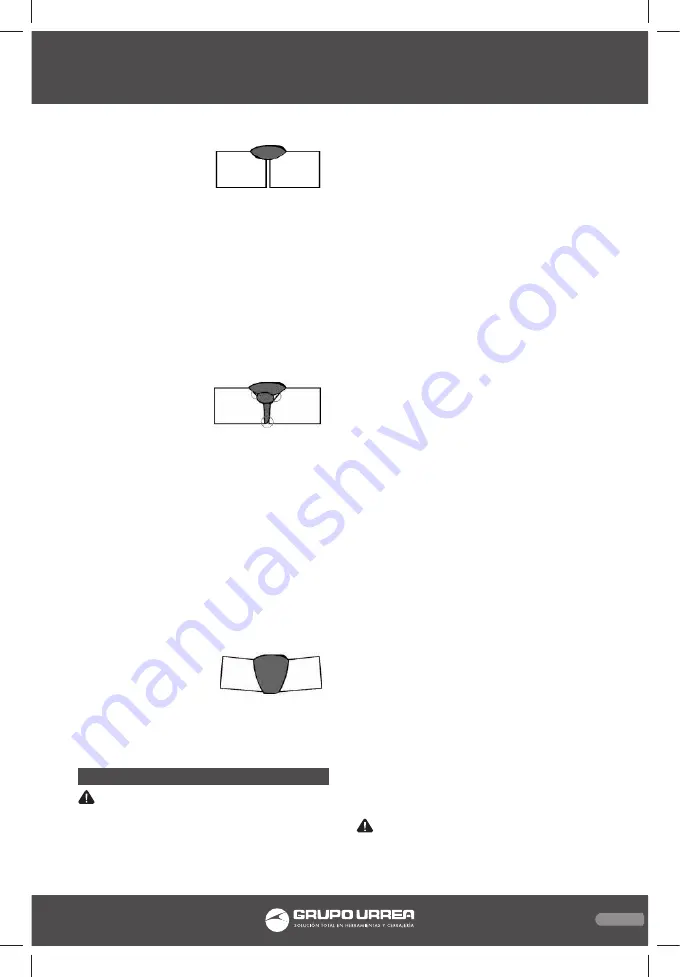
25
E N G L I S H •
User’s manual
3. Inadequate: Weld does
not contact the joint
fully, just on the surface.
a. Work pieces too thick/
close; Joint design
must allow weld to reach bottom of groove
and allow proper welding procedures.
b. Incorrect welding technique; Maintain
1/2”or less stick out. Keep arc on leading
edge of weld puddle. Hold gun at proper
angles.
c. Insufficient weld material; Increase wire feed
speed.
d. Insufficient weld heat; Reduce Welding
Speed.
NOT ADHERING PROPERLY
Gaps present between
weld and previous bead
or between weld and
workpiece.
a. Dirty workpiece; Make certain that work-
piece is clean and free from oil, coatings,
and other residues.
b. Insufficient weld material; Increase wire
feed speed.
c. Incorrect welding technique; Place stringer
bead at correct place in joint. Adjust work-
piece position or weld angle to permit
proper welding at bottom of work- piece.
Pause briefly at sides when using a weave
bead. Keep arc on leading edge of weld
puddle. Hold gun at proper angles and
make tack welds to help hold pieces.
BENT AT JOINT
a. Improper clamping;
Make sure that pieces
are clamped securely
in place.
b. Excessive heat; Weld a small portion and al-
low cooling before proceeding. Reduce wire
feed speed.
MAINTENANCE
WARNING: Make sure the Power Switch of
the Plasma welder is in its “OFF” position and
that the tool is unplugged from the electri-
cal outlet before performing any inspection,
maintenance, or cleaning procedures.
1. Periodically open the Access Panel from the
machine and, using compressed air, blow out
all dust and debris from the interior
2. Always store the welder in a clean, dry, safe
location out of reach of children and other un-
authorized people.
For optimal weld quality, clean and inspect the
contact tip and nozzle before each use, as fol-
lows: Nozzle Inspection, cleaning;
a. Turn the Nozzle (1b) counterclockwise while
pulling to remove.
b. Scrub the interior of the Nozzle clean with
a wire brush.
c. Examine the end of the nozzle(1a).The end
should be flat and even, If the end is uneven,
chipped, melted, cracked, or otherwise dam-
aged, the nozzle will adversely effect the
weld and should be replaced.
d. Reinstall the Nozzle (1a) after inspecting and
cleaning the Contact Tip.
Contact tip Inspection, cleaning, and replace-
ment
a. Make sure the entire Welding torch is com-
pletely cool before proceeding.
b. Remove the nozzle as explained above. Then
remove the contact tip.
c. Scrub the exterior of the contact tip clean
with a wire brush. Check that the contact tip
is the proper type for the wire size used.
d. Examine the hole at the end of the contact
tip for the following problems:
Shape: The hole should be an even circle,
and should not be oblong or have any
bulges in it.
Size: The Contact Tip will decrease in effi-
ciency as the center hole enlarges. A Contact
Tip that measures 150% or more the original
size* should be replaced. (*.045” or more
for .030” tips; .035” or more for .023 tips).
e. If any problems are noted with a Contact Tip
(1b), it is recommended to have it replaced.
When inspection and maintenance is complet-
ed, reinstall the Contact Tip (1b) and Nozzle
(2b).
MAINTENANCE
WARNING: Make sure the Power Switch of
the Welder is in its “OFF” position and that the
tool is unplugged from the electrical outlet be-
SOLM1020 manual.indd 25
26/11/15 2:53 p.m.