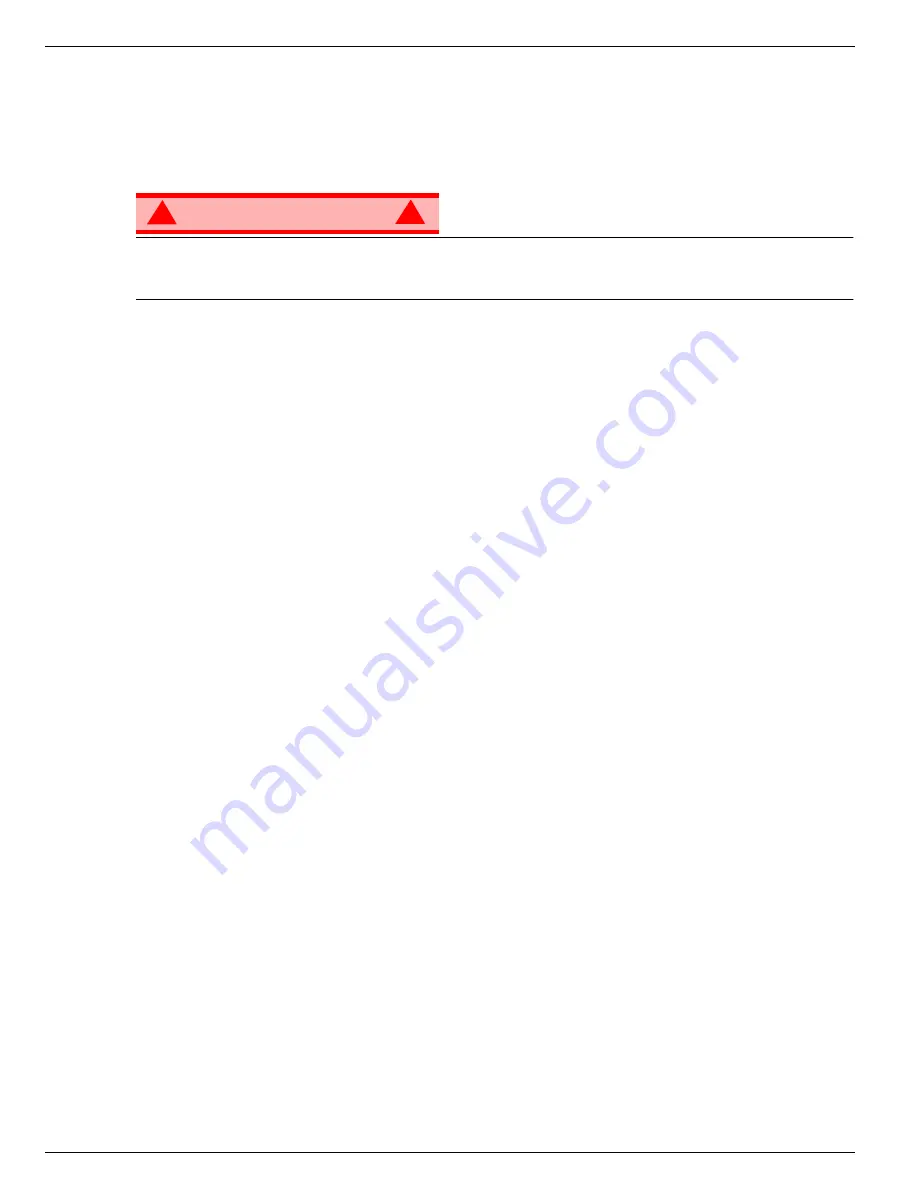
Page 12
107098-002 TM12 - Operator Manual
Daily Inspection and Maintenance Schedule
D
AILY
I
NSPECTION
AND
M
AINTENANCE
S
CHEDULE
The Complete Inspection consists of periodic visual and operational checks, along with periodic minor
adjustments that assure proper performance. Daily inspection will prevent abnormal wear and prolong the
life of all systems. Perform the inspection and maintenance items daily. Inspection and maintenance shall
be performed by personnel who are trained and familiar with mechanical and electrical procedures.
W A R N I N G
!
!
Before performing preventative maintenance, familiarize yourself with the operation of the machine.
Always block the elevating assembly whenever it is necessary to perform maintenance while the
platform is elevated.
The daily preventative maintenance checklist has been designed for machine service and maintenance.
Please photocopy the Daily Preventative Maintenance Checklist and use the checklist when inspecting
the machine.
Summary of Contents for TM12
Page 1: ...TM12 Work Platform Serial Numbers 7352 Current Publication Number 107099 002 ...
Page 4: ...Foreword Page ii Service Manual NOTES ...
Page 19: ...Labels 107098 002 TM12 Operator Manual Page 15 Figure 11 Safety Labels Locations ...
Page 82: ...Section 4 Schematics Page 4 6 107099 002 TM12 Work Platform NOTES ...