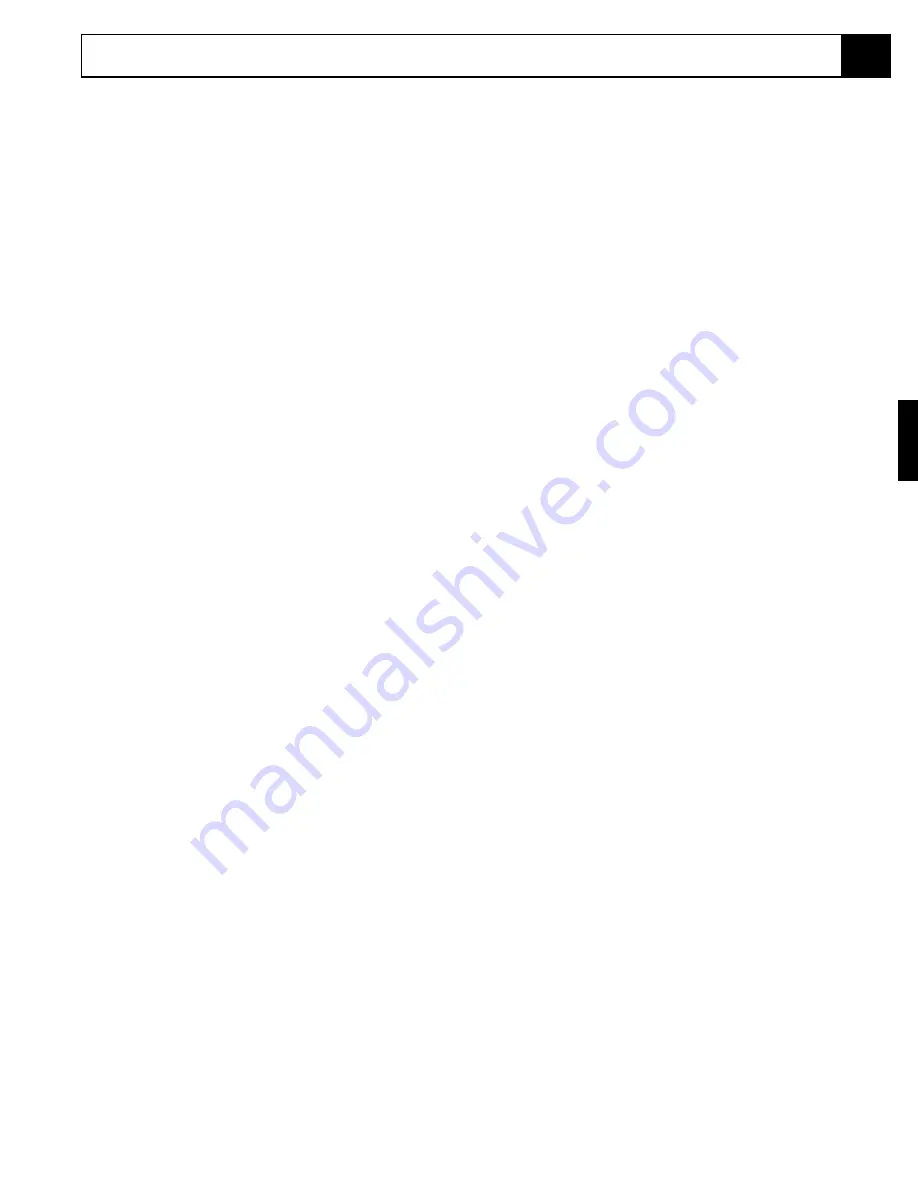
Section
3-17
AB46 Work Platform
Maintenance
3.13
Torque Hub Seal Replacement
ROLL AND LEAK TESTING
IMPORTANT: Torque hubs should always be roll
and leak tested before disassembly and after
assembly to make sure gears and sealants are
working properly.
ROLL TEST
Gears should be able to rotate by applying a constant
force to the axle. Some gear packages roll with more
difficulty than others. Do not be concerned if gears
seem to roll hard as long as they roll with consistency. If
you feel more drag only at certain points the gears are
not rolling freely and should be checked for improper
installation or defects.
LEAK TEST
The purpose of a leak test is to make sure the unit is air
tight. Pressurize hub to 5 PSI. Torque hub has a leak if
the air pressure starts to fall after hub has been pressur-
ized. Use soap and water on hub to detect location of
leaks. If a leak is detected, seal or "O" ring must be
replaced.
PRESSING TOOLS
The seal, cup and cone pressing tools are illustrated on
pages 3-20, 3-21 and 3-23. Use pressing tools identical
in size or fabricate them using the dimensions shown.
DISASSEMBLY (Figure 3-19)
CAUTION: Safety glasses should be used during
disassembly of hub.
1. Remove two pipe plugs in cover and drain the oil
from the unit.
2. Loosen and remove shoulder bolts and cap screws
from cover. Remove cover from hub.
3. Remove "O" ring. Remove thrust washer from
counterbore in cover.
4. Remove input gear from planet gears.
5. Using a punch, remove retaining ring from groove
around inside of input gear.
6. Lift carrier sub-assembly from hub. Lift ring gear
from hub. Remove "O" ring from counterbore in
hub.
7. Remove pipe plugs from side of hub body.
8. Apply a preload to output shaft to remove retaining
ring. Follow steps a & b.
a. Place bearing cone pressing tool on retaining
ring.
b. Apply pressure to fixture using a hydraulic ram
or by striking the fixture with a soft face ham
mer. Pressure should be applied until hub
rotates with difficulty.
9. Using retaining ring pliers remove retaining ring.
Remove spacer from output shaft.
10. Place spacer under hub so output shaft will fall
through bottom when pressed out.
11. Press output shaft out of hub. Output shaft may
come out with bearing cone and seal attached.
Remove seal and discard. Use a punch and hammer
to remove bearing cone. Be careful not to strike
shaft with punch.
12. If seal and cone remain in hub, press them out using
a pressing tool.
13. Lift bearing cone out of hub.
14. Stand hub on its small end. Using a punch and
hammer, remove bearing cup from counterbore of
hub. Be careful not to strike counterbore with
punch.
15. Turn hub over on larger end. Using a punch and
hammer, remove bearing cup from counterbore of
hub. Be careful not to strike counterbore.
NOTE: Carrier sub-assembly does not need to be
disassembled to replace seals.
ASSMEBLY
NOTE: Torque all hardware to torques listed on page
3-32 unless otherwise specified.
1. Oil output shaft and bearing cone. Using cone press,
press bearing cone onto end of output shaft with
retaining ring groove.
3. Stand hub on its small end. Using bearing cup
pressing tool press bearing cup down into hub.
NOTE: Make sure cup sits square with counterbore.
4. Turn hub over so it sit on large end. Using bearing
cup pressing tool press bearing cup into small end of
hub.
NOTE: Make sure cup sits square with counterbore.
5. Place output shaft into hub so end of shaft with
retaining ring groove points down.
6. Oil output shaft. Using seal pressing tool press seal
into counterbore in small end of hub. The closed
face of the seal should be up.
Summary of Contents for AB46 C
Page 1: ...AB46 I C Service Parts Manual Service Parts Manual 2 WHEEL DRIVE WORK PLATFORMS...
Page 4: ...AB46 Work Platform ii Foreword NOTES...
Page 38: ...Section 3 20 AB46 Work Platform Maintenance 3 13 Figure 3 20 Seal Pressing Tool...
Page 39: ...Section 3 21 AB46 Work Platform Maintenance 3 13 Figure 3 21 Bearing Cone Pressing Tool...
Page 40: ...Section 3 22 AB46 Work Platform Maintenance 3 13 Figure 3 22 Bearing Cup Pressing Tool...
Page 65: ...Schematics Section AB46 Work Platform 5 9 Figure 5 4 068340 002 Hydraulic Schematic 5 2...
Page 67: ...Schematics Section 5 11 AB46 Work Platform 5 3 Figure 5 6 Hydraulic Valve Ports...
Page 68: ...Section 5 12 AB46 Work Platform Schematics 5 3 5 2 Figure 5 7 Check Ports...
Page 81: ...Illustrated Parts Breakdown 6 2 Section AB46 Work Platform 6 7 NOTES...
Page 87: ...Illustrated Parts Breakdown 6 2 Section AB46 Work Platform 6 13 NOTES...
Page 89: ...Illustrated Parts Breakdown 6 2 Section AB46 Work Platform 6 15...
Page 95: ...Illustrated Parts Breakdown 6 2 Section AB46 Work Platform 6 21...
Page 97: ...Illustrated Parts Breakdown 6 2 Section AB46 Work Platform 6 23...
Page 99: ...Illustrated Parts Breakdown 6 2 Section AB46 Work Platform 6 25...
Page 105: ...Illustrated Parts Breakdown 6 2 Section AB46 Work Platform 6 31 NOTES...
Page 111: ...Illustrated Parts Breakdown 6 2 Section AB46 Work Platform 6 37 NOTES...
Page 113: ...Illustrated Parts Breakdown 6 2 Section AB46 Work Platform 6 39...
Page 115: ...Illustrated Parts Breakdown 6 2 Section AB46 Work Platform 6 41...
Page 117: ...Illustrated Parts Breakdown 6 2 Section AB46 Work Platform 6 43...
Page 119: ...Illustrated Parts Breakdown 6 2 Section AB46 Work Platform 6 45 NOTES...
Page 125: ...Illustrated Parts Breakdown 6 2 Section AB46 Work Platform 6 51 NOTES...
Page 131: ...Illustrated Parts Breakdown 6 2 Section AB46 Work Platform 6 57 NOTES...
Page 135: ...Illustrated Parts Breakdown 6 2 Section AB46 Work Platform 6 61 NOTES...
Page 137: ...Illustrated Parts Breakdown 6 2 Section AB46 Work Platform 6 63...
Page 139: ...Illustrated Parts Breakdown 6 2 Section AB46 Work Platform 6 65 NOTES...
Page 141: ...Illustrated Parts Breakdown 6 2 Section AB46 Work Platform 6 67...
Page 145: ...Illustrated Parts Breakdown 6 2 Section AB46 Work Platform 6 71...
Page 147: ...Illustrated Parts Breakdown 6 2 Section AB46 Work Platform 6 73...