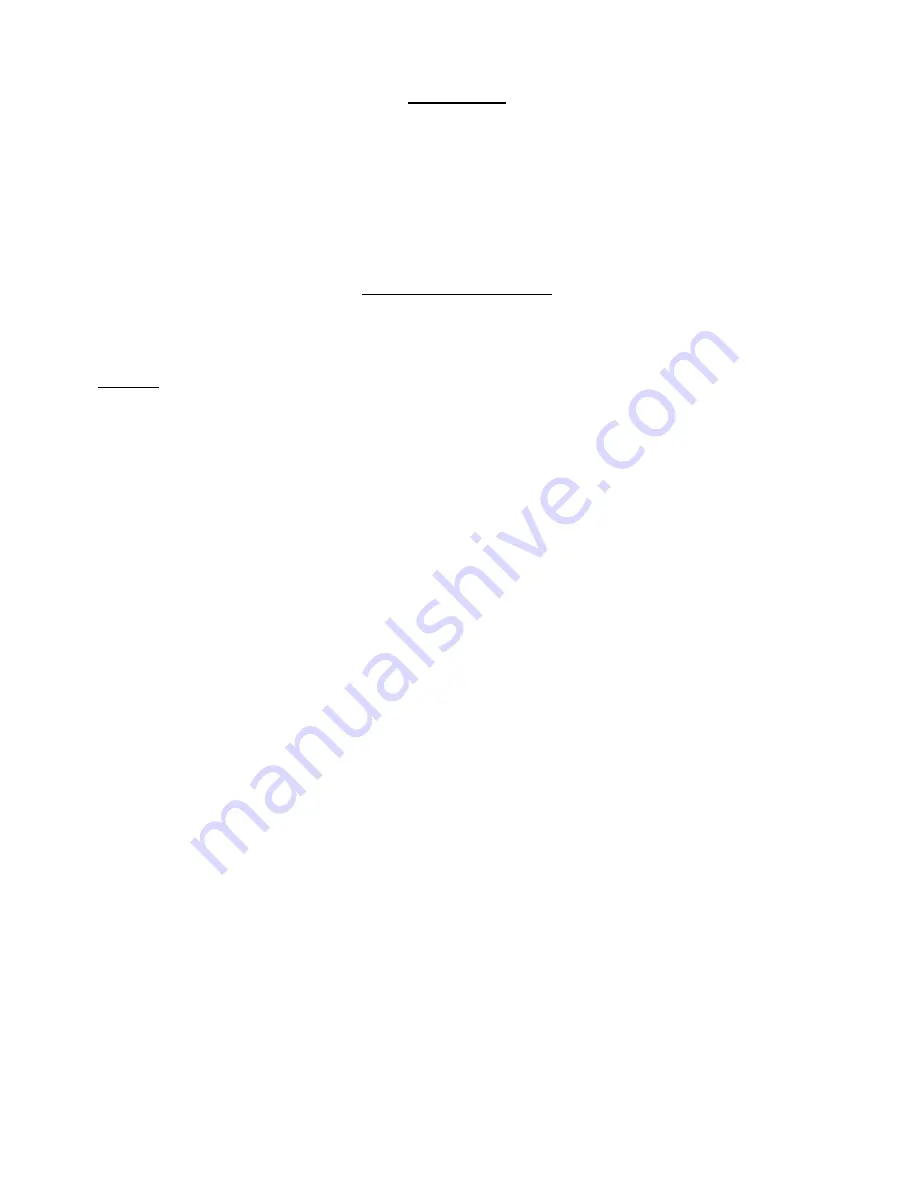
6509
LUBRICATION
Lubrication instructions are given in Figures 2 and 2A on pages 10 and 11. Operator's attention is called to lubricating
the slide bar (Fig. 4 [52]) as needed for smooth carriage motion, at least monthly with three drops of mineral oil.
The shaft of the last slice device (Fig. 4 [19]) should be lubricated as necessary with petrogel to maintain light film.
Distribute over surfaces by moving the grip and fence back and forth. Wipe excess film from shafts with a clean cloth.
MECHANICS MAINTENANCE
Every year a mechanic or service technician should perform the following inspection and carry out the respective
maintenance as required:
Warning: FOR SAFETY, TURN OFF SLICER AND DISCONNECT ELECTRICAL CORD.
1.
BELT DRIVE
- This drive features a multi-ribbed high performance belt for long trouble-free service.
Inspect belt for proper tension. If glazed or excessively worn. replace. A tensioning device automatically
allows for normal belt wear-in and stretching. However, if additional tension is required, it may be
obtained by turning adjustment nuts (Fig. 3 [52]) clockwise on take-up rod (Fig. 3 [58]) which will further
compress the tensioning spring. As a guideline, the compressed length of the spring should be
approximately 7/8".
2.
MOTOR
- Motor is pre-lubricated and requires no periodic maintenance or relubrication in normal
kitchen usage. Provision for relubrication in extreme duty applications is provided by means of oiling
orifices at both shaft end and opposite ends of motor. A light we ight electric motor oil or #10 non-
detergent oil may be used.
3.
SLICE ADJUSTMENT
- Check, by turning the slice adjustment knob (Fig. 5 [2]), to make sure that the
fence is closing completely (below "0" on knob) and that knife edge is not exposed. If fence is not closing
all the way such that the edge of the knife is exposed, check first for damage or obvious obstructions. If
there is no obvious damage to parts or obstructions, turn knob to highest number it will go, hold knob in
place and loosen set screw (Fig. 5 [10]); now hold cam (Fig. 5 [9]) in place and turn the knob to "12-1/4";
retighten set screw (Fig. 5 [10]). Check fence again to make sure that the fence is closed completely
(below "0" on knob) and that the knife is not exposed. The closed or zero set position on the knob should
be in the white colored zone of the knob's dial.
4.
CARRIAGE
- Check for free smooth operation of last slice device and for smooth travel of carriage arm
(Fig. 4 [23]). Check for excess backlash between slide bearing (Fig. 4 [50]) and carriage slide (Fig. 4
[55]). The correct lash (clearance) required for smooth carriage operation is obtained when a very slight
lash or movement can be detected. Too much lash can result in the carriage striking and damaging the
knife edge. Too little lash results in binding and a loss of smoothness in carriage travel. Lash is adjusted
by loosening locknut (Fig. 4 [47]) and turning brass rubbing screw (Fig. 4 [48]) clockwise to reduce lash
and counterclockwise to increase lash. Tighten locknut while holding rubbing screw stationary with a
screwdriver so it does not move. Grease only the side of the carriage slide (Fig. 4 [55]) on which this
brass rubbing screw slides.
5.
LUBRICATION & FUNCTION CHECK
- General lubrication should be performed in accordance
with the lubrication instructions in Fig. 2 and 2A. During this lubrication
PAGE 7