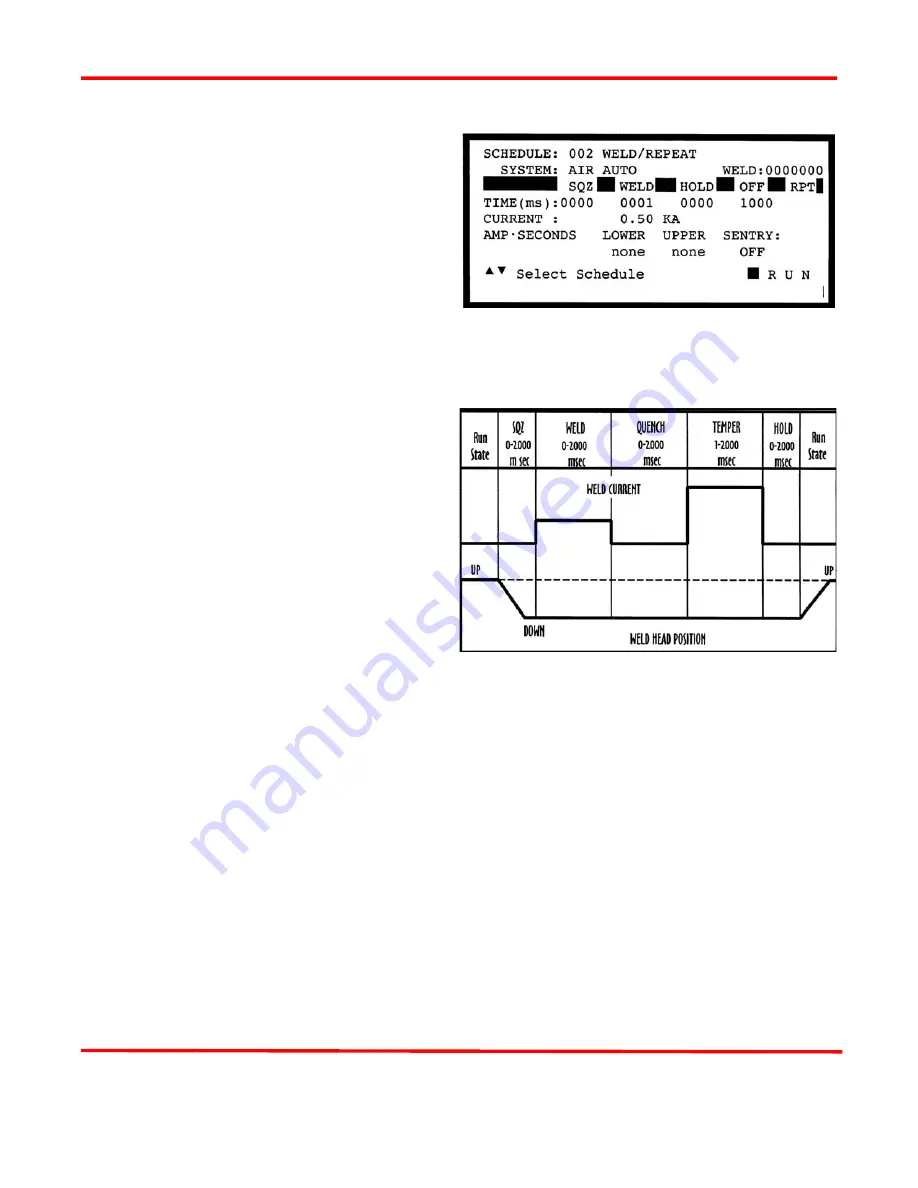
CHAPTER 6: ADVANCED WELD FUNCTIONS
MODEL HF2 2 kHz HIGH FREQUENCY RESISTANCE WELDING POWER SUPPLY
6-4
990-057
Weld/Repeat Alphanumeric Run Screen
(Figure 6-6)
To simultaneously view all pre-programmed
time periods and energy settings, press [CHNG]
to select the Alphanumeric Run screen. The 7
digit Weld Counter is displayed in the upper
right corner.
Figure 6-6. Weld/Repeat
Alphanumeric Screen.
QUENCH/TEMPER (Figure 6-7)
Quench/Temper is typically used to weld flat-to-
flat, round-to-round, or round-to-flat parts
together that are plated. Properly used,
Quench/Temper can significantly reduce weld
splash and electrode sticking.
In the normal application of Quench/Temper, the
Weld Period provides sufficient heat to displace
the plating or oxides, seat the electrodes against
the base metals, and force the parts into intimate
contact. The Quench Period allows time to
dissipate the heat generated during the Weld
Period. The Temper Period completes the
structural weld. The Temper Period weld
Figure 6-7. Quench/Temper
current should be greater than the Weld Period weld current by a factor of two or three since the first
bond significantly reduces the resistance of the interface between the parts.
Another use for Quench/Temper is to control grain refinement in the parts. In this application, the Weld
Period weld current makes the structural weld. The parts cool during the Quench Period. The low level
Temper Period weld current completes the heat treating process by providing sufficient heat to permit
grain realignment. In this application, the weld current magnitudes for both the Weld and Temper
Periods are completely opposite to those shown in Figure 6-7. 410 stainless steel is one of the materials
which must be heat treated (annealed) in order to eliminate the brittle, crystalline structure caused by the
weld current. This application of Quench/Temper is not usually used in the form just described for
welding small parts.
Quench/Temper can be used with Unitek Peco Force Fired Manual or Air Actuated Weld Heads. For
Manually Actuated Weld Heads, weld current begins when the Force Firing Switch closes. For Force
Fired Air Actuated Weld Heads, weld current begins when both levels of a two-level Foot Switch are
closed and the Force Firing Switch in the Air Actuated Weld Head closes.