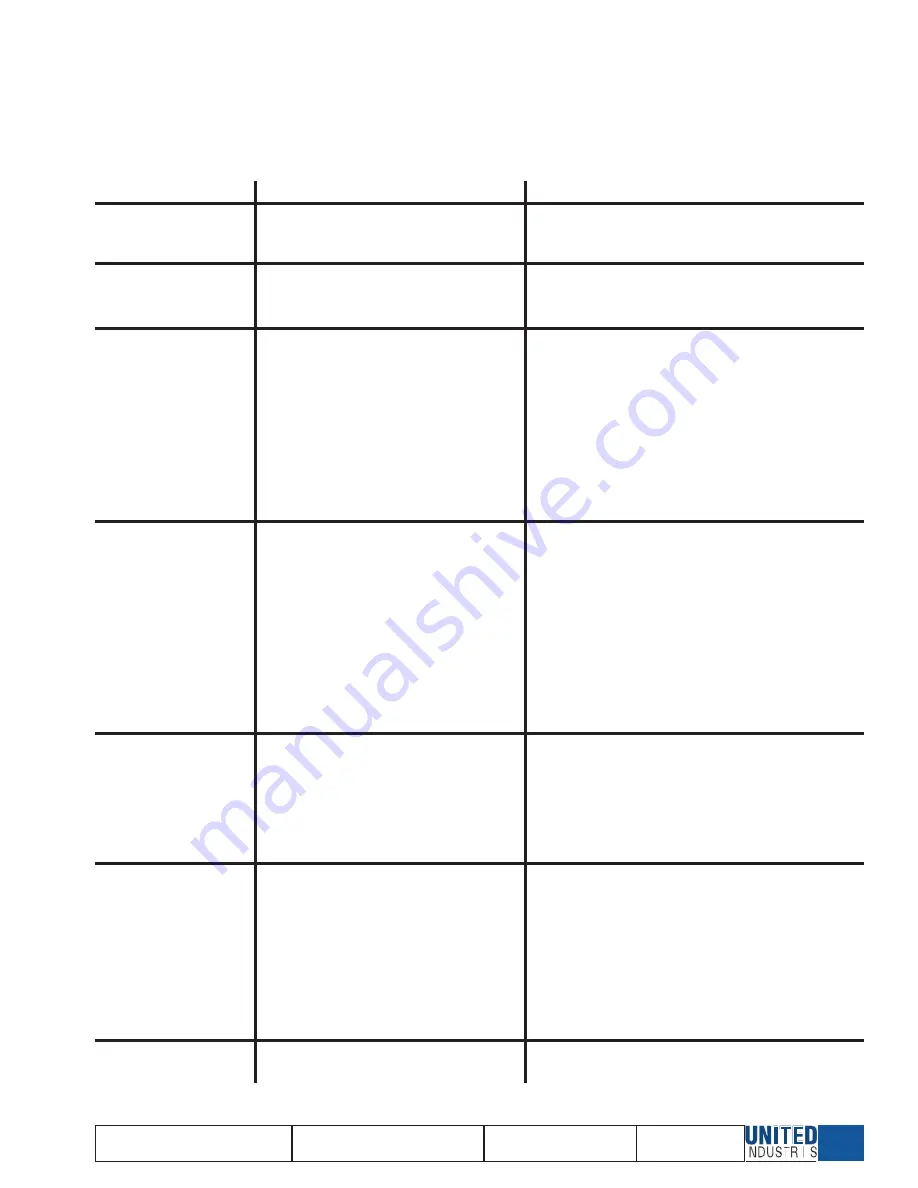
33
United Industries, Inc.
P.O. Box 58
Sterling, KS 67579
800-835-3272 • 620-278-3160
Fax 800-500-3115 • 620-278-3115
www.towerflo.com
Data presented here is the best available at the
time of publicaton. United Industries and/or its
representatives assume no liability for its use.
Form TFH-TS:10/95
TROUBLE SHOOTING
The trouble shooting pages are provided in order to give you the ability to locate and possibly remedy problems that
may occur during normal operation of your TOWER-FLO
®
Water Filter System. If you are unable to solve the prob-
lem, please do not hesitate to contact us.
PROBLEM
POSSIBLE CAUSE
SOLUTION
PUMP STOPS
A Pump motor or circuit
A Check circuit breakers, wire connections (loose, bro-
ken or incorrect), thermal protector in motor starter
tripped. Allow motor to cool, then try to restart
1
WATER LEVEL DROPS
A Gravity draining of basin; filter installed
A Prevent gravity draining by following the warning
IN BASIN
below static water level of basin and power instructions under Installation, Step 1., on page 7.
interrupted to pump during backwash
BACKWASHES TOO
A Differential pressure switch adjusted
A Using bench air, check ∆P set at 10 psi. If at 10 psi,
OFTEN OR CONSTANT
too low; virtually constant closure
increase setting by two to three psi
BACKWASH
B Differential pressure switch stuck closed B Check switch for continuity with no pressure on system
C Backwash control circuit failure
C Check circuit breakers, wire connections (loose, bro-
ken or incorrect), timers, and fuses,
D High pressure drop through filter
D Inspect filter bed for foreign material and contaminated
due to clogging
or caked sand and remove from tank. Replace with
same volume of clean, new silica sand
BACKWASHES TOO
A Differential pressure switch adjusted
A Using bench air, check ∆P set at 10 psi. If at 10 psi,
INFREQUENTLY OR
too high for backwash initiation or
decrease setting by two to three psi
NEVER
B Differential pressure switch malfunction B Check switch for continuity with no pressure on system
C No water flow
C Check for
1. Loss of pump prime
2. Clogged strainer basket
D Low pressure drop through filter
D Inspect filter bed for foreign material and contaminated
due to channeling
or caked sand and remove from tank. Replace with
same volume of clean, new silica sand
PUMP LOSES PRIME
A Strainer cover leaking
A Check lid and O-ring for defects; tighten lid clamp
B Water level too low
B Add water
C Suction line clogged or leaking
C Inspect and repair as needed
D Horizontal run over 18" in suction line
D See warning under Installation, Step 1., on page 7.
UNUSUAL NOISES
A Plumbing vibration
A Ensure all plumbing anchored properly
B Bad motor bearings
B Repair or replace motor
C Pump
C
1. Cavitation
1. See A, B, and C directly above
2. Foreign objects in pump
2. Check volute and impeller
3. Impeller out of adjustment
3. Adjust impeller by loosening the three set screws in
the shaft extension and repositioning the impeller to
center of pump volute
SAND BEING DRIVEN
A Cracked or broken lateral(s)
A Replace cracked or broken laterals
TO TOWER
1
If motor re-starts after cooling, check amperage draw at the motor and compare to Full Load Amp Draw (FLA) as noted in Your Filter’s
Specifications on page 4. If amp draw is above noted FLA draw, reduce flow on discharge side of pump.