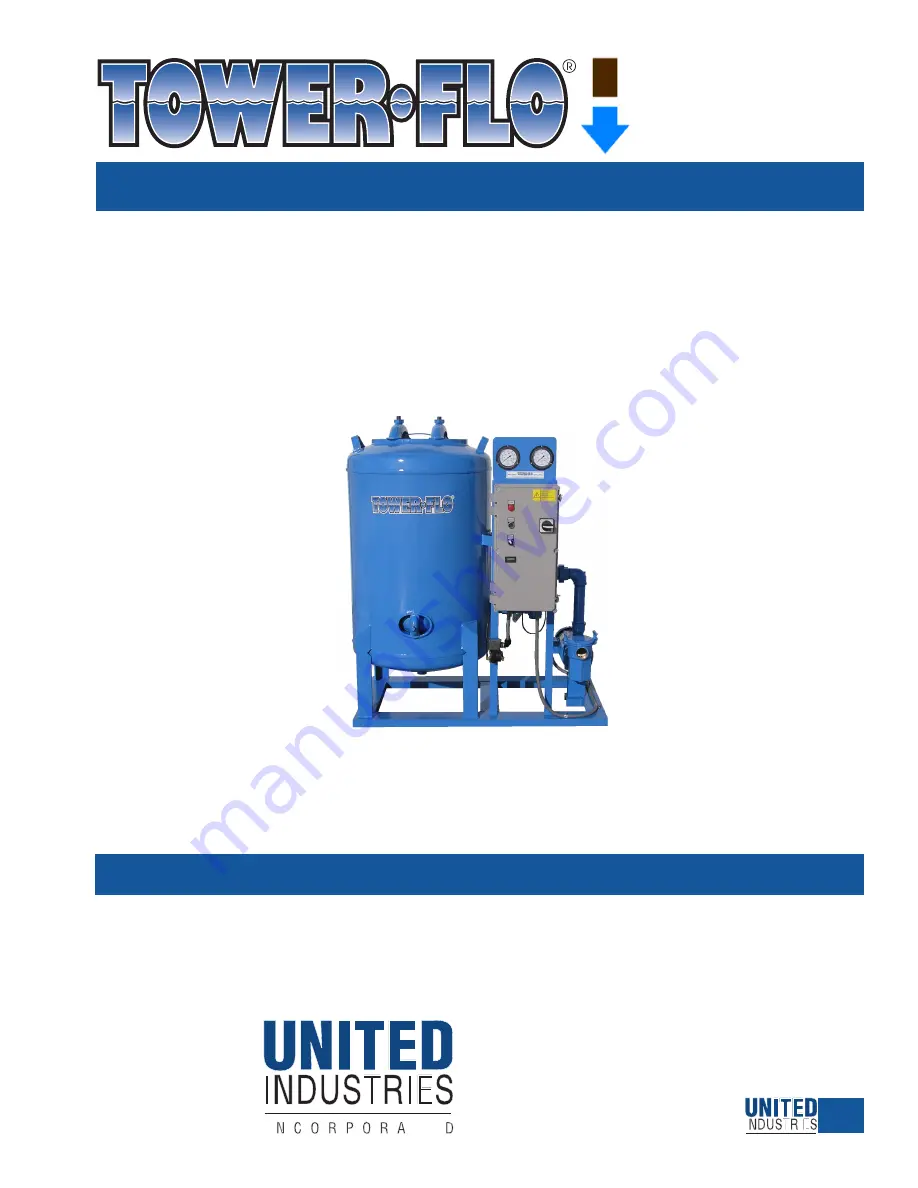
for
Series
TFH
Water Filter Systems
T
OWER-FLO
®
Division
United Industries, Inc.
P. O. Box 58
Sterling, KS 67579
800-835-3272 • 620-278-3160
Fax 800-500-3115 • 620-278-3115
www.towerflo.com
TECHNICAL MANUAL
Complete information for
Engineering, Installation, Operation & Maintenance
of Tower-Flo
®
Series TFH Water Filter Systems
1